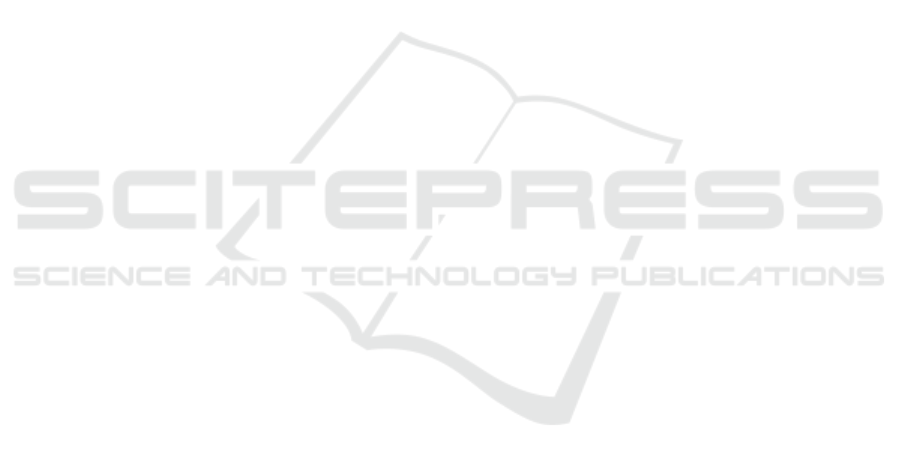
In this paper we propose a domain optimization al-
gorithm that aligns the models for efficient planning.
We can either apply this algorithm on-demand, prior
to the planning, or as an offline step. We rely on our
set-theoretic foundation to reformulate the declarative
and procedural knowledge of the domain without in-
fringing their validity. We analyze the performance
of the optimization in a simulated setup with 800 test
runs and tasks of varying lengths. The final experi-
ment is conducted on a real two-arm robotic system.
2 RELATED WORK
There are two strands in the literature that target do-
main optimization problems.
A recently very active branch are data-driven al-
gorithms, notably reinforcement learning approaches,
which optimize heuristics for a specific domain.
These methods show very good performances for
some easy to simulate problems, like board games
(Silver et al., 2016), (Silver et al., 2017) or com-
puter games (Mnih et al., 2013), (Vinyals et al., 2019).
However, application on real-world scenarios are still
difficult due to the limited data available. Attempts
to overcome this include large scale pick and place
setups with hundreds of robots (Kalashnikov et al.,
2018) and, due to the difficult nature of physics, hard
but rather short tasks (Xie et al., 2019).
In (Schmitt et al., 2019) reinforcement learning is
used in combination with an abstraction layer. This
layer allows eased simulation, ensures viability, like
collision-free movements, and provides an interface
for real-world execution that handles small devia-
tions. Still, training requires large datasets and pro-
cessing power. Additionally, the trained model is a
black box and thus hard to debug or transfer. In our
approach we rely on models and rules rather than sin-
gle data points that define the behavior of the resulting
system. The explicit representation enables introspec-
tion, which is a key feature during development and
for industrial environments. Additionally, less com-
putational power is needed for our approach. How-
ever, it lacks theoretical optimality and still requires
experts to program. In (N
¨
agele et al., 2018) another
approach, which relies on domain specific heuristics
is proposed. In this case, however, the heuristics are
computed online by analyzing the desired goal. Ge-
ometric interdependencies are broken up and the re-
sulting plan is executed in simulation.
Another strand of related work covers optimiza-
tion of modeled domains. In (Kang and Nnaji, 1993)
a scheme for aligned and manually designed domains
is elaborated. This, however, covers a single domain
only and brings in its benefits only when strictly fol-
lowed. In a real-world scenario different parties bring
in their modules, which are used for completely dif-
ferent problems as well, to compose the overall do-
main. Therefore, it is very hard to align everyone to
a common scheme. In our approach each party ful-
fills their user-role with the representation they pre-
fer. Just before planning, we harmonize the represen-
tations automatically.
For this type of optimization many algorithms that
operate on discrete, mainly PDDL domains have been
proposed. Two strands can be identified for algo-
rithms which either transform the problem to suite the
planner, or pick a planner, which can cope with the
characteristics of the original problem.
Portfolio planners, such as (Seipp et al., 2012),
(Katz et al., 2018) apply different planners with dif-
ferent heuristics on the domain and try to switch to the
most appropriate combination for the current problem
formulation.
In (Haslum et al., 2007), (Vallati et al., 2015) au-
tomated optimization algorithms for PDDL-domains
are proposed, which allow even non-experts to ap-
ply generic planning algorithms on general PDDL-
domains. In (Areces et al., 2014) a formalization for
an optimization scheme was found, that was formerly
applied manually on the domains. This even allows
an engineer to inspect the optimized formulation to
validate and further optimize it easily. However, it
comes with the difficulties and limitations of PDDL
to handle continuous domains.
3 APPROACH
Before we discuss our new domain optimization algo-
rithm, we highlight the properties of its set-theoretic
foundation, which was introduced in (Kast et al.,
2019a).
Our new algorithm is effective in combination
with a hierarchical planner only. We point out the rel-
evant properties of an example hierarchical planning
algorithm, which was proposed in (Kast et al., 2019b).
3.1 Declarative Knowledge
Following the line of (Kast et al., 2019a), we call el-
ements of the declarative knowledge concepts. For
us, a concept C is a subset of some concept base B
Γ
which is a set of instances that is not necessarily fi-
nite. Concepts with the same concept base B
Γ
belong
to the same concept class Γ. The partial order more-
detailed than M
Γ
between two concepts holds true if
each instance described by the first concept is also an
ICINCO 2020 - 17th International Conference on Informatics in Control, Automation and Robotics
760