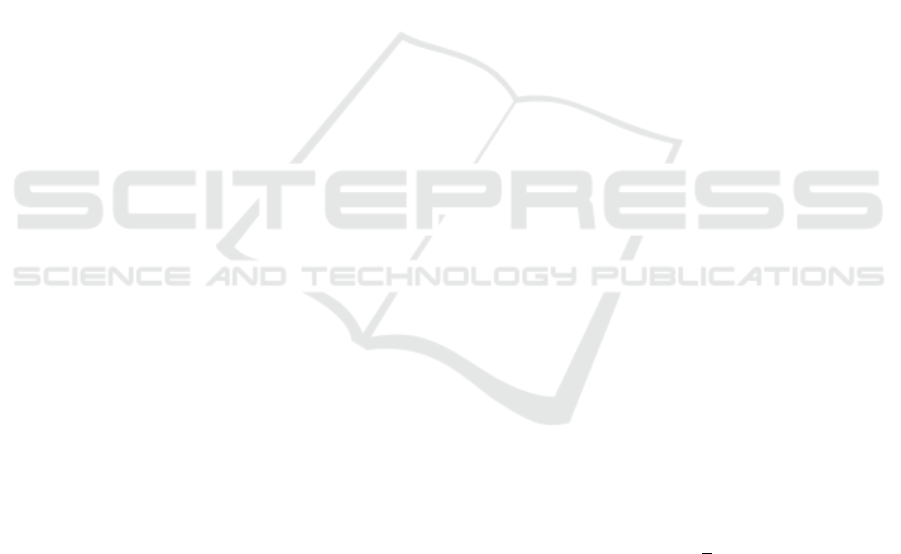
6 CONCLUSION
In this work, the problem of MPC control design for a
four-tank benchmark model was considered. First, it
was shown that under suitable constraints the nonlin-
ear continuous time system can be stabilized by a lin-
ear discrete time controller. Moreover, we have con-
ducted simulations that show the good performance
of the control algorithm.
Further work will provide tighter estimates of the
region where stability and feasibility can be guaran-
teed. Another promising research direction is the use
of hybrid/multi model in order to enhance the control
performance and robustness.
ACKNOWLEDGEMENTS
The authors would like to thank the Regional Council
Hautes-de-France for its support.
REFERENCES
Alvarado, I., Limon, D., de la Pe
˜
na, D. M., Maestre, J.,
Ridao, M., Scheu, H., Marquardt, W., Negenborn, R.,
Schutter, B. D., Valencia, F., and Espinosa, J. (2011).
A comparative analysis of distributed mpc techniques
applied to the hd-mpc four-tank benchmark. Journal
of Process Control, 5:800–815.
Boyd, S. and Vandenberghe, L. (2004). Convex optimiza-
tion. Cambridge university press.
Cueli, J. R. and Bordons, C. (2008). Iterative nonlinear
model predictive control. stability, robustness and ap-
plications. Control Engineering Practice, 16(9):1023
– 1034.
Dua, P., Doyle, F. J., and Pistikopoulos, E. N. (2006).
Model-based blood glucose control for type 1 diabetes
via parametric programming. IEEE transactions on
bio-medical engineering, 53:1478–1491.
Fele, F., Maestre, J. M., and Camacho, E. F. (2017). Coali-
tional control: Cooperative game theory and control.
IEEE Control Systems Magazine, 37(1).
Huang, Y., Wang, H., Khajepour, A., He, H., and Ji, J.
(2017). Model predictive control power management
strategies for hevs: A review. Journal of Power
Sources, 341:91–106.
Johansson, K. H. (2000). The quadruple-tank process: a
multivariable laboratory process with an adjustable
zero. IEEE Trans. Contr. Sys. Techn., 8:456–465.
Kailath, T. (1980). Linear systems, volume 156. Prentice-
Hall Englewood Cliffs, NJ.
Kalman, R. E. et al. (1960). Contributions to the theory of
optimal control. Bol. soc. mat. mexicana, 5(2):102–
119.
Maiworm, M., B
¨
athge, T., and Findeisen, R. (2015).
Scenario-based model predictive control: Recur-
sive feasibility and stability. IFAC-PapersOnLine,
48(8):50 – 56. 9th IFAC Symposium on Advanced
Control of Chemical Processes ADCHEM 2015.
Mayne, D., Rawlings, J., Rao, C., and Scokaert, P. (2000).
Constrained model predictive control: Stability and
optimality. Automatica, 36(6):789 – 814.
Pannocchia, G. (2012). Course on model predictive control.
bio engineering and robotics research center, pages
1–33.
Qin, S. J. and Badgwell, T. A. (2003). A survey of indus-
trial model predictive control technology. Control en-
gineering practice, 11(7):733–764.
Rawlings, J. B. and Mayne, D. Q. (2009). Model predictive
control: Theory and design, nob hill pub. Madison,
Wisconsin.
Richter, S., Jones, C. N., and Morari, M. (2009). Real-time
input-constrained mpc using fast gradient methods. In
Proceedings of the 48h IEEE Conference on Decision
and Control (CDC) held jointly with 2009 28th Chi-
nese Control Conference, pages 7387–7393. IEEE.
Scokaert, P. O. and Rawlings, J. B. (1998). Constrained
linear quadratic regulation. IEEE Transactions on au-
tomatic control, 43(8):1163–1169.
Segovia, P., Rajaoarisoa, L., Nejjari, F., Duviella, E., and
Puig, V. (2019). A communication-based distributed
model predictive control approach for large-scale sys-
tems. In 58th IEEE Conference on Decision and Con-
trol (CDC). IEEE.
Seung Cheol Jeong and PooGyeon Park (2005). Con-
strained mpc algorithm for uncertain time-varying
systems with state-delay. IEEE Transactions on Au-
tomatic Control, 50(2):257–263.
Tabuada, P. (2007). Event-triggered real-time scheduling of
stabilizing control tasks. IEEE Transactions on Auto-
matic Control, 52(9):1680–1685.
APPENDIX
Proof of Lemma 1
Proof. Solving the optimization problem (4) with
any discretization time h < h leads to an LQR con-
troller K associated with a Cost x
0
0
Q
f
x
0
Such that
(A − BK)
0
Q
f
(A − BK)− Q
f
= −Q.
Since A = I + hA + o(h),B = hB + o(h), defining
W (h) := I + h(A − BK)
(W (h) + o(h))
0
Q
f
(W (h) + o(h)) − Q
f
< −Q/2
h(A − BK +o(h))
0
Q
f
+ hQ
f
(A − BK) + o(h) < −Q/2,
Therefore there exist h small enough such that
(A − BK)
0
Q
f
+ Q
f
(A − BK) < −S,
Implementation of Centralized MPC on the Quadruple-tank Process with Guaranteeing Stability
61