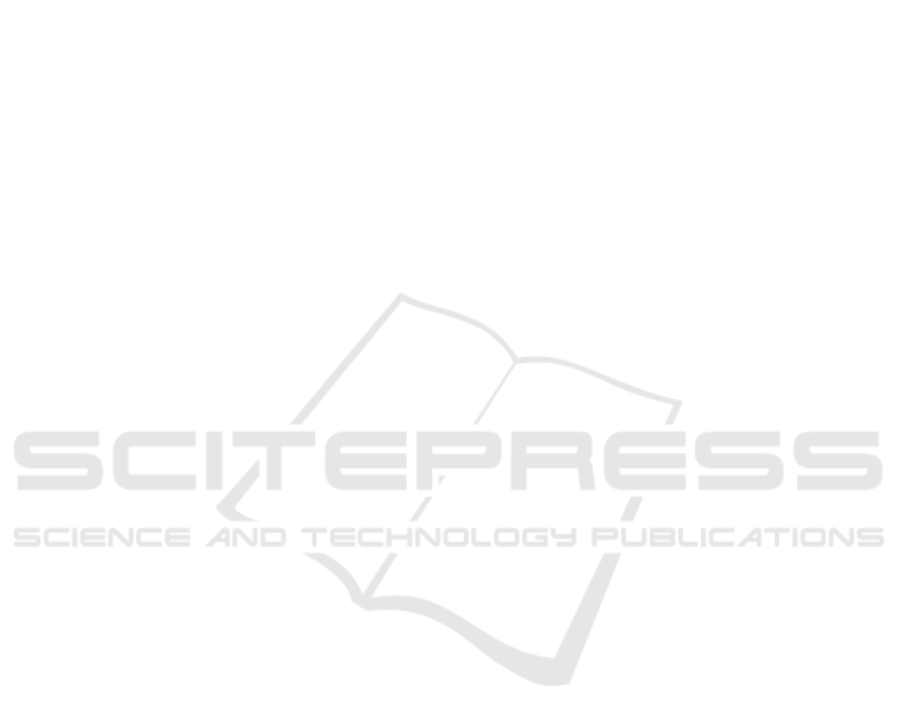
Reduced Error Model for Learning-based Calibration of Serial
Manipulators
Nadia Schillreff and Frank Ortmeier
Chair of Software Engineering, Otto-von-Guericke-University Magdeburg, Germany
Keywords:
Modeling, Parameter Identification, Calibration.
Abstract:
In this work a reduced error model for a learning-based robot kinematic calibration of a serial manipula-
tor is compared with a complete error model. To ensure high accuracy this approach combines the geo-
metrical (structural inaccuracies) and non-geometrical influences like for e.g. elastic deformations that are
configuration-dependent without explicitly defining all underlying physical processes that contribute to po-
sitioning inaccuracies by using a polynomial regression method. The proposed approach is evaluated on a
dataset obtained using a 7-DOF manipulator KUKA LBR iiwa 7. The experimental results show the reduction
of the mean Cartesian error up to 0.16 mm even for a reduced error model.
1 INTRODUCTION
For a robot manipulator that is mainly used in repet-
itive applications (e.g. pick-and-place operations)
where the desired poses (position and orientation) of
the manipulator’s end-effector (EE) can be manually
taught, high repeatability is important to successfully
perform defined tasks. This ability to repeat a known
pose has submilimeter values for modern manipula-
tors. However if a task is unique, the robot is mostly
given a target pose defined in some relative or abso-
lute coordinate system. Such situations arise often
when robot’s poses are obtained through a simulation
during which the layout of the working environment
and a model of the robot are used. This requires spe-
cial attention to the accuracy of the simulated robot
model, and whether it corresponds to the actual kine-
matics of the robot.
The process of robot calibration that consists of
developing a mathematical model and identification
of parameters that are able to reflect the actual be-
havior of the investigated robot can be divided into
three categories (Elatta et al., 2004). The first is joint
calibration, which is also called first level calibra-
tion, where the difference between the actual joints
displacements and the encoder signals is considered.
Level two involves kinematic calibration, where the
robots kinematic parameters are determined. Level
three takes into account non-kinematic error sources
like elasticity of the links or the backlash of the joints.
The main sources for positioning inaccuracies
can be divided into geometric and non-geometric
errors.nGeometric errors are present when nominal
kinematic parameters of the robot do not correspond
to actual parameters due to for ex. manufacturing er-
rors.
Non-geometric errors include among others the
link and joint compliance, elastic deformations, trans-
mission nonlinearities, and thermal expansion. To in-
clude these effects into the robotic model the under-
lying processes can be expressed with gear or elastic
models as in (Klimchik et al., 2015) or (Marie et al.,
2013). Considering all sources that can potentially
contribute to the end-effector positioning errors, it is
difficult to model all relevant parameters explicitly.
Instead, learning-based approaches are proposed
to model the behaviour of a robot. This allows us
to solve the calibration problem as a function esti-
mation task based on the measured data. In general
errors of the robot’s EE may originate from five fac-
tors (Liou et al., 1993): environmental (e.g. tem-
perature or the warm-up process), parametric (e.g.
Kinematic parameter variation due to manufacturing
and assembly errors, influence of dynamic parame-
ters, friction and other nonlinearities), measurement
(resolution and nonlinearity of joint position sensors),
computational (computer round-off and steady-state
control errors) and application (e.g. installation er-
rors). To be able to reflect different influences in the
model, experiments that include variations of the rel-
evant factors would have to be conducted. This work
considers the influence of only a limited amount of
478
Schillreff, N. and Ortmeier, F.
Reduced Error Model for Learning-based Calibration of Serial Manipulators.
DOI: 10.5220/0009835804780483
In Proceedings of the 17th International Conference on Informatics in Control, Automation and Robotics (ICINCO 2020), pages 478-483
ISBN: 978-989-758-442-8
Copyright
c
2020 by SCITEPRESS – Science and Technology Publications, Lda. All rights reser ved