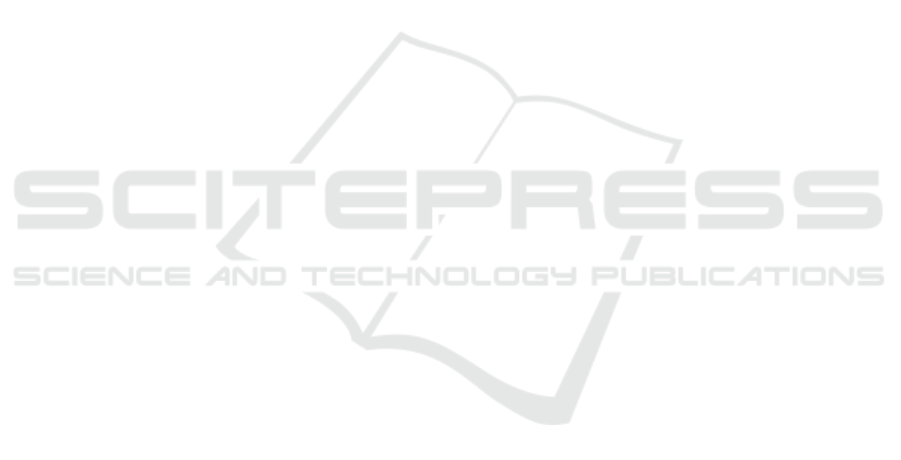
In future works, we intend to differentiate between
the multiple faults that can occur all at once by us-
ing smart IoT devices. Also, we investigate for re-
ducing time for fault type identification by inserting a
database knowledge directive. Finally, we plan to add
a policy to manage and actions to handle the overloads
devices.
REFERENCES
Alvarez-Mesa, M., Chi, C. C., Juurlink, B., George, V.,
and Schierl, T. (2012). Parallel video decoding in the
emerging hevc standard. In 2012 IEEE International
Conference on Acoustics, Speech and Signal Process-
ing (ICASSP), pages 1545–1548. IEEE.
Bradley, K. and Strosnider, J. K. (1998). An application
of complex task modeling. In Proceedings. Fourth
IEEE Real-Time Technology and Applications Sympo-
sium (Cat. No. 98TB100245), pages 85–90. IEEE.
Casado-Vara, R., De la Prieta, F., Rodriguez, S., Sitton, I.,
Calvo-Rolle, J. L., Venayagamoorthy, G. K., Vega, P.,
and Prieto, J. (2019). Adaptive fault-tolerant tracking
control algorithm for iot systems: Smart building case
study. In International Workshop on Soft Computing
Models in Industrial and Environmental Applications,
pages 481–490. Springer.
Choi, J., Jeoung, H., Kim, J., Ko, Y., Jung, W., Kim, H.,
and Kim, J. (2018). Detecting and identifying faulty
iot devices in smart home with context extraction. In
2018 48th Annual IEEE/IFIP International Confer-
ence on Dependable Systems and Networks (DSN),
pages 610–621. IEEE.
Chudzikiewicz, J., Furtak, J., and Zielinski, Z. (2015).
Fault-tolerant techniques for the internet of military
things. In 2015 IEEE 2nd World Forum on Internet of
Things (WF-IoT), pages 496–501. IEEE.
Di Modica, G., Gulino, S., and Tomarchio, O. (2019). Iot
fault management in cloud/fog environments. In Pro-
ceedings of the 9th International Conference on the
Internet of Things, pages 1–4.
Jeong, B., Yoo, S., Lee, S., and Choi, K. (2000). Hardware-
software cosynthesis for run-time incrementally re-
configurable fpgas. In Proceedings 2000. Design
Automation Conference.(IEEE Cat. No. 00CH37106),
pages 169–174. IEEE.
Kannan, R., Manohar, S. S., and Kumaran, M. S. (2019).
Iot-based condition monitoring and fault detection for
induction motor. In Proceedings of 2nd International
Conference on Communication, Computing and Net-
working, pages 205–215. Springer.
Lee, H. (2017). Framework and development of fault de-
tection classification using iot device and cloud envi-
ronment. Journal of Manufacturing Systems, 43:257–
270.
Min, D., Xiao, Z., Sheng, B., Quanyong, H., and Xuwei, P.
(2014). Design and implementation of heterogeneous
iot gateway based on dynamic priority scheduling al-
gorithm. volume 36, pages 924–931. Sage Publica-
tions Sage UK: London, England.
Power, A. and Kotonya, G. (2019). Providing fault toler-
ance via complex event processing and machine learn-
ing for iot systems. In Proceedings of the 9th Inter-
national Conference on the Internet of Things, pages
1–7.
Radia Bendimerad, Kamel Smiri, A. J. (2019). Performance
estimation within iot system. In IINTEC. 2019 inter-
national conference on Internet of Things. Embedded
Systems and Communications. IEEE.
Spanias, A. S. (2017). Solar energy management as an in-
ternet of things (iot) application. In 2017 8th Interna-
tional Conference on Information, Intelligence, Sys-
tems & Applications (IISA), pages 1–4. IEEE.
Su, P. H., Shih, C.-S., Hsu, J. Y.-J., Lin, K.-J., and Wang, Y.-
C. (2014). Decentralized fault tolerance mechanism
for intelligent iot/m2m middleware. In 2014 IEEE
World Forum on Internet of Things (WF-IoT), pages
45–50. IEEE.
Tsai, F.-K., Chen, C.-C., Chen, T.-F., and Lin, T.-J. (2019).
Sensor abnormal detection and recovery using ma-
chine learning for iot sensing systems. In 2019 IEEE
6th International Conference on Industrial Engineer-
ing and Applications (ICIEA), pages 501–505. IEEE.
Zieliski, Z., Chudzikiewicz, J., and Furtak, J. (2019). An
approach to integrating security and fault tolerance
mechanisms into the military iot. In Security and
Fault Tolerance in Internet of Things, pages 111–128.
Springer.
Fault Detection and Co-design Recovery for Complex Task within IoT Systems
491