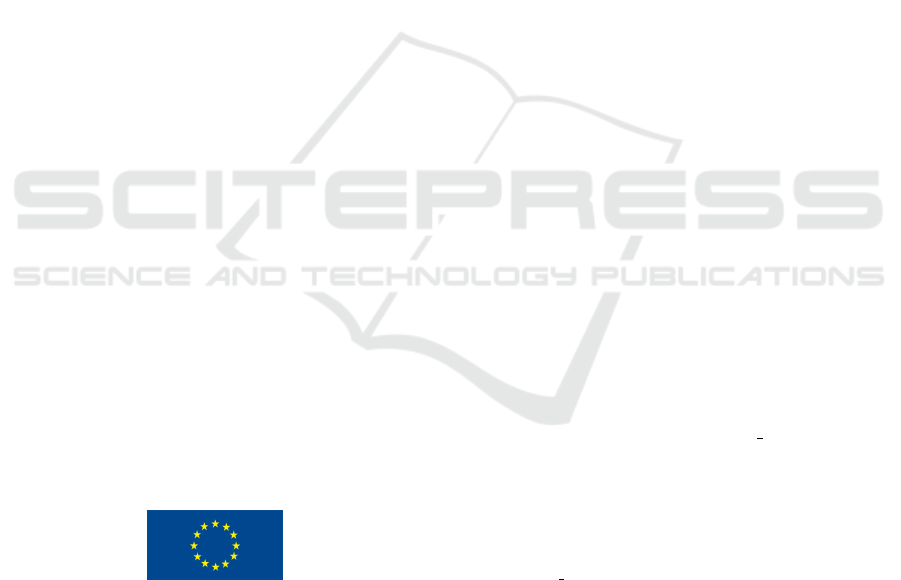
a good tracking of the reference speed by the maxon
drive, as the NEDC profile is easily recognisable.
Finally, the estimated consumed energy per kilo-
meter at the EV battery terminals is displayed in Fig-
ure 17 (considering the same assumptions as for Fig-
ure 14). The final value of this plot (168 Wh/km) is
17.5 % higher than the claimed consumption of the
modelled EV, i.e. 143 Wh/km (BMW, 2017). Such
an overestimation can be expected, since the raw es-
timation of the motor and converter efficiencies are
very probably underestimations.
7 CONCLUSIONS
In this work, the MBST methodology has been suc-
cessfully applied to a downscaled XiL test setup used
for the validation of EV powertrains, thanks to ade-
quate scaling factors. Validation has been performed
on the NEDC. The results also show the influence of
the control strategy on the tracking of the speed pro-
file and suggests a possible future use of the small-
scale bench for control optimisation.
In future work, the authors will build on this work
to increase the power level of the SuT and show
the scalability of the proposed framework to real EV
components. Additionally, the didactic side of this
downscaled setup will be further exploited by further
extending its instrumentation. The present PMSM
used in SuT will also be exchanged with an induc-
tion motor of similar power to enable testing this type
of traction motors.
ACKNOWLEDGEMENTS
This project was partially funded by the European
Union’s Horizon 2020 research and innovation pro-
gram under grant agreement No 769506.
The content of this publication does not reflect the of-
ficial opinion of the European Union. Responsibility
for the information and views expressed therein lies
entirely with the authors.
REFERENCES
Blochwitz, T., Otter, M.,
˚
Akesson, J., Arnold, M., Clauß,
C., Elmqvist, H., Friedrich, M., Junghanns, A.,
Mauss, J., Neumerkel, D., Olsson, H., and Viel,
A. (2012). Functional mockup interface 2.0: The
standard for tool independent exchange of simulation
models. In Proceedings of the 9th International Mod-
elica Conference.
BMW (2017). Specifications. the new bmw i3. In BMW
media information, pages 1–8.
Ciceo, S., Mollet, Y., Sarrazin, M., Van der Auweraer, H.,
and Martis, C. (2016). Model-based design and test-
ing for electric vehicle energy consumption analysis.
Electrotehnic
˘
a, Electronic
˘
a, Automatic
˘
a, 64:46–51.
EtherCAT Technology group (2019). EtherCAT. www.
ethercat.org. Accessed: 2019-08-05.
Fathy, H. K., Filipi, Z. S., Hagena, J., and Stein, J. (2006).
Review of hardware-in-the-loop simulation and its
prospects in the automotive area. Proceedings of SPIE
- The International Society for Optical Engineering,
6228.
Fiori, C., Ahn, K., and Rakha, H. A. (2016). Power-
based electric vehicle energy consumption model:
Model development and validation. Applied Energy,
168:257–268.
Gomes, C., Thule, C., Larsen, P. G., and Vangheluwe, H.
(2017). Co-simulation: State of the art.
Joos, A. J. (2019). Implementation of a small-scale elec-
trical drive system in Hardware-in-the-Loop simula-
tions. Master’s thesis, Brussels Faculty of Engineer-
ing.
Obelics consortium (2019). Homepage - Obelics. obelics.
eu. Accessed: 2019-08-05.
Petersheim, M. D. and Brennan, S. (2009). Scal-
ing of hybrid-electric vehicle powertrain components
for hardware-in-the-loop simulation. Mechatronics,
19:1078–1090.
Popp, A., Sarrazin, M., Van der Auweraer, H., Fodorean,
D., Birte, O., Karoly, B., and Martis, C. (2015). Real-
time co-simulation platform for electromechanical ve-
hicle applications. 2015 9th International Symposium
on Advanced Topics in Electrical Engineering, pages
240–243.
Real-Time Linux Wiki (2016). Real-Time Linux Wiki.
rt.wiki.kernel.org/index.php/Main Page. Accessed:
2020-04-01.
Siemens Digital Industries Software (2019). Model-
based system testing: Efficiently combining test
and simulation for model-based development.
https://www.plm.automation.siemens.com/media/
global/en/Model-based%20system%20testing%
20WP tcm27-67978.pdf.
Stettinger, G., Horn, M., Benedikt, M., and Zehetner, J.
(2014). Model-based coupling approach for non-
iterative real-time co-simulation. In 2014 European
Control Conference (ECC), pages 2084–2089.
Szirtes, T. and R
´
ozsa, P., editors (2007). Applied Di-
mensional Analysis and Modeling, pages 133 – 161.
Butterworth-Heinemann, Burlington, 2nd edition.
Texas Instruments (2017). InstaSPIN-FOC and InstaSPIN-
MOTION User’s Guide. http://www.ti.com/lit/ug/
spruhj1g/spruhj1g.pdf. Accessed: 2019-08-05.
Van der Auweraer, H., Sarrazin, M., and Marques dos San-
tos, F. (2017). Model-based system testing: A new
ICINCO 2020 - 17th International Conference on Informatics in Control, Automation and Robotics
602