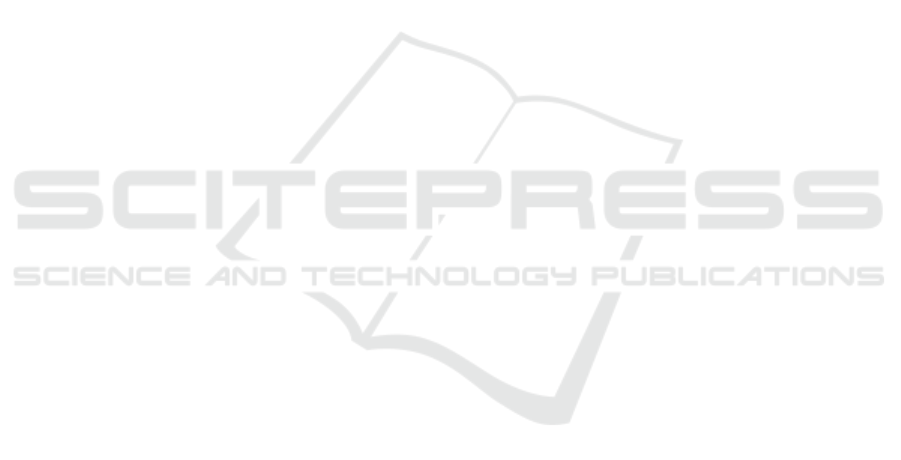
swivel-mounted camera is limited. Therefore, it must
be considered to what extent the angle between the
normal of the POI and the vector of the optical axis
of the camera may deviate. In addition, a minimum
distance between the copter and the component may
be required for safety reasons.
The route should contain all viewpoints from
which all POIs can be inspected. Therefore, it is im-
portant to keep the route through all the viewpoints as
short as possible and optimize the route lenght. Since
the search for the shortest route in three-dimensional
space is NP-hard (LaValle, 2006), procedures must be
considered that offer an almost optimal solution for
this problem in polynomial time. In the course of op-
timizing the route length, it is therefore important to
keep the number of viewpoints as small as possible,
while still ensuring an optimal view of all POIs.
This work is dedicated to exactly these two parts,
the viewpoint and trajectory planning. This involves
the fully automated inspection of predefined areas on
the component. It is examined how viewpoints can be
planned offline on the prerequisites mentioned above
and a route based on them. The designed procedure
is tested simulatively and the results of the trajectory
planning are evaluated using benchmark data sets.
2 RELATED WORK
Work that is specifically dedicated to the fully auto-
mated inspection of technical infrastructures by UAVs
usually aims to achieve complete visual coverage
of the entire surface of the respective infrastructure,
which is the aim of the Coverage Path Planning (Gal-
ceran and Carreras, 2013; Danner and Kavraki, 2000).
A detailed summary of the current inspection scenar-
ios provided by UAVs is provided by (Jordan et al.,
2018). According to the work of (Bircher et al.,
2015), the most adaptable approaches to the inspec-
tion scenario are those that use two-step optimiza-
tion. In a first step, viewpoints are computed that
cover the entire surface of the infrastructure, which
can be achieved by solving the Art Gallery problem
(O’Rourke, 1987; Gonz
´
alez-Banos, 2001). In a sec-
ond step, a route or trajectory is calculated that con-
nects all viewpoints, which can be modeled by solv-
ing the Traveling Salesman Problem (Laporte, 1992).
A concrete CPP solution for UAVs is described
by (Bircher et al., 2015), in which the surface of
the infrastructure is represented by a triangle mesh
and a viewpoint is calculated for each triangle, from
which the triangle is completely visible. In the sec-
ond step a route through all viewpoints is planned.
To do this, viewpoints are connected directly to each
other if there is no obstacle between them, otherwise
the RRT* search algorithm (Karaman and Frazzoli,
2011) is used to connect both viewpoints. RRT* is
an extension of the Rapidly Exploring Random Tree
(RRT) search algorithm by (LaValle, 2006).
(Englot and S. Hover, 2014) also show a two-step
procedure for the inspection of ship hulls, which has
already been successfully tested on the object. Al-
though the procedure was designed for the use of au-
tonomous underwater vehicles, it is still noteworthy
because it deals with the automated offline planning
of sensor positions relative to a component in three-
dimensional space. In the first phase, configurations
are randomly sampled by the Redundant Roadmap
Algorithm until the surface is covered. In the sec-
ond phase, an iterative solution of the RRT over all
goal-to-goal routes calculates a route that connects all
goals. Here, goal-to-goal means that the route ends at
the configuration where it started. The Local Cover-
age Algorithm (LCA) optimizes the route in terms of
length: Therefore (P, C) is the set system. The surface
to be observed depends on a finite set of geometric
primitives p
i
∈ P (i.e., POIs to be covered) and from
each configuration q
j
∈ Q (i.e., a viewpoint) a set of p
i
can be observed. The LCA is passed a coverage route
W
G
which is not yet optimized. The algorithm se-
lects any goal q
j
∈ W
G
per iteration and tries to find a
configuration q
0
j
that observes all primitives, that also
observes q
j
and at the same time reduces the costs
for the route section W
q−1,q+1
. Finding an optimized
route stage is done by RRT
∗
||
, a variant of the RRT*
algorithm by (Karaman and Frazzoli, 2011). To get
an optimized route section W
0
q−1,q+1
with q
0
j
as inter-
mediate configuration, RRT
∗
||
will calculate in parallel
an optimal collision free route from q
j−1
to q
0
j
and
one from q
0
j
to q
j+1
. For this purpose two RRT* trees
are built with q
j−1
and q
j+1
as the root. This method
was evaluated at USCGC Seneca and it was shown
that the feasible route with 192 viewpoints and 246
m could be improved to an optimized route with 169
viewpoints and 157 m length.
Works dealing with finding viewpoints usually
assume that any pose of the camera can be taken.
According to (Alarcon-Herrera et al., 2014) optimal
viewpoints can be found for a POI if the optical axis
of the camera runs along the normal vector of the POI
and a so-called standoff distance to the POI is main-
tained. The standoff distance is calculated from the
desired resolution of the POI in the image, the height
and width of the image sensor and the angle of aper-
ture of the camera. By aligning the optical angle along
the normal of the POI, the POI is centered in the pic-
ture, which ensures maximum visibility of the POI.
ICINCO 2020 - 17th International Conference on Informatics in Control, Automation and Robotics
72