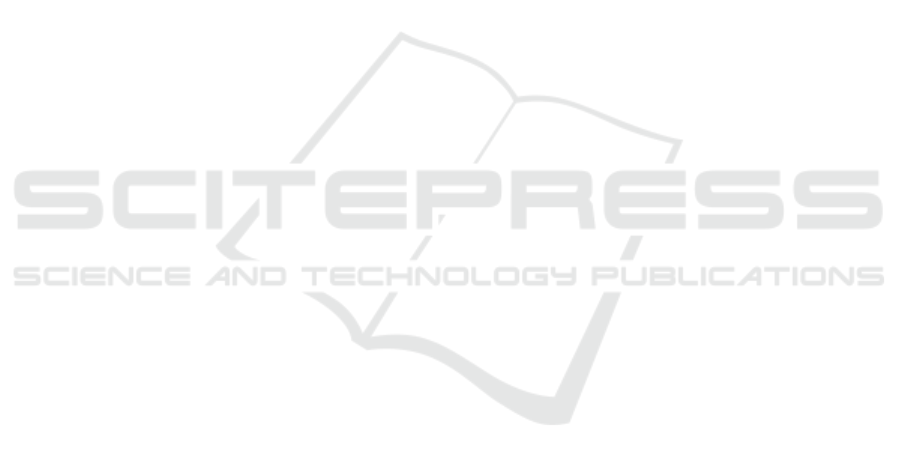
trol strategy was applied taking into account the cal-
culation of the CoG, the inertia and the allocation ma-
trix instantaneously. The simulations have shown sat-
isfactory results of the Backstepping controller. The
flight test and implementation of the control laws are
in the final phase.
Adaptive control laws and optimization of the en-
ergy consumption will be treated in our future works.
REFERENCES
Avant, T., Lee, U., Katona, B., and Morgansen, K. (2018).
Dynamics, hover configurations, and rotor failure
restabilization of a morphing quadrotor. In 2018
Annual American Control Conference (ACC), pages
4855–4862.
Brescianini, D. and D’Andrea, R. (2016). Design, modeling
and control of an omni-directional aerial vehicle. In
2016 IEEE international conference on robotics and
automation (ICRA), pages 3261–3266.
Desbiez, A., Expert, F., Boyron, M., Diperi, J., Viollet, S.,
and Ruffier, F. (2017). X-morf: A crash-separable
quadrotor that morfs its x-geometry in flight. In 2017
Workshop on Research, Education and Development
of Unmanned Aerial Systems (RED-UAS), pages 222–
227.
Falanga, D., Kleber, K., Mintchev, S., Floreano, D., and
Scaramuzza, D. (2018). The foldable drone: A mor-
phing quadrotor that can squeeze and fly. IEEE
Robotics and Automation Letters, 4(2):209–216.
Floreano, D. and Wood, R. J. (2015). Science, technology
and the future of small autonomous drones. Nature,
521(7553):460–466.
Kamel, M., Verling, S., Elkhatib, O., Sprecher, C., Wulkop,
P., Taylor, Z., Siegwart, R., and Gilitschenski, I.
(2018). The voliro omniorientational hexacopter: An
agile and maneuverable tiltable-rotor aerial vehicle.
IEEE Robotics & Automation Magazine, 25(4):34–44.
Mintchev, S., Daler, L., L’Eplattenier, G., Saint-Raymond,
L., and Floreano, D. (2015). Foldable and self-
deployable pocket sized quadrotor. In 2015 IEEE In-
ternational Conference on Robotics and Automation
(ICRA), pages 2190–2195.
Mintchev, S. and Floreano, D. (2016). Adaptive morphol-
ogy: A design principle for multimodal and multi-
functional robots. IEEE Robotics & Automation Mag-
azine, 23(3):42–54.
Mintchev, S., Shintake, J., and Floreano, D. (2018).
Bioinspired dual-stiffness origami. Science Robotics,
3(20):eaau0275.
Nemati, A. (2016). Designing, modeling and control of a
tilting rotor quadcopter. PhD thesis, University of
Cincinnati.
Riviere, V., Manecy, A., and Viollet, S. (2018). Ag-
ile robotic fliers: A morphing-based approach. Soft
Robotics, 5(5):541–553.
Ryll, M., Bülthoff, H. H., and Giordano, P. R. (2015). A
novel overactuated quadrotor uav: Modelling, con-
trol and experimental validation. IEEE Transactions
on Control Systems Technology, Institute of Electrical
and Electronics Engineers, 23(2):510–556.
Sanket, N. J., Singh, C. D., Ganguly, K., Fermüller, C., and
Aloimonos, Y. (2018). Gapflyt: Active vision based
minimalist structure-less gap detection for quadro-
tor flight. IEEE Robotics and Automation Letters,
3(4):2799–2806.
Xiong, H., Hu, J., and Diao, X. (2019). Optimize energy
efficiency of quadrotors via arm rotation. Journal of
Dynamic Systems, Measurement, and Control, 141(9).
Zhao, M., Anzai, T., Shi, F., Chen, X., Okada, K., and
Inaba, M. (2018). Design, modeling, and control of
an aerial robot dragon: A dual-rotor-embedded multi-
link robot with the ability of multi-degree-of-freedom
aerial transformation. IEEE Robotics and Automation
Letters, 3(2):1176–1183.
ICINCO 2020 - 17th International Conference on Informatics in Control, Automation and Robotics
544