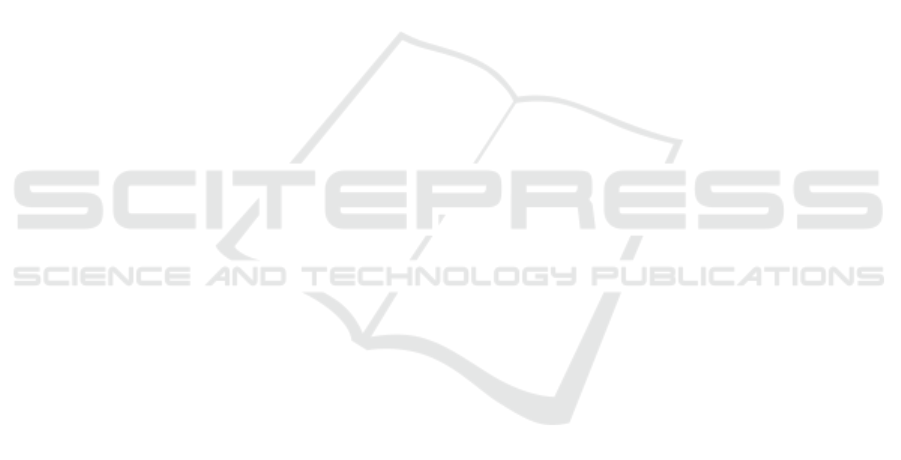
5 CONCLUSIONS
In this paper, a new adaptive fault-tolerant control
allocation algorithm is proposed. The proposed al-
gorithm integrates online effectiveness matrix and
bias faults estimation with the control allocation al-
gorithm. The actuator and bias faults are considered
under actuator amplitude and rate constraints. The ef-
fectiveness of the proposal is shown by using a marine
surface vehicle model where the proposed algorithm
showed good performance in terms of control allo-
cation. Future works foresees the implementation of
this class of adaptive control allocation strategies on
real redundant marine vehicles.
ACKNOWLEDGEMENTS
The authors want to thank Ing. Paolo Folino and Ing.
Vincenzo D’Angelo by AppliCon S.r.l for providing
us with the mathematical model of the autonomous
marine vehicle they developed in their master’s the-
ses and for useful discussions and assistance in their
vehicle control and guidance aspects.
REFERENCES
Casavola, A. and Garone, E. (2010). Fault-tolerant adaptive
control allocation schemes for overactuated systems.
International Journal of Robust and Nonlinear Con-
trol, 20(17):1958–1980.
Chu, Z., Xiang, X., Zhu, D., Luo, C., and Xie, D. (2018).
Adaptive fuzzy sliding mode diving control for au-
tonomous underwater vehicle with input constraint.
International Journal of Fuzzy Systems, 20(5):1460–
1469.
D’Angelo, V. (2018). Strategie di gestione delle missioni
e controllo di un veicolo marino autonomo di superfi-
cie. Master’s thesis, University of Calabria. Master’s
thesis in Automation Engineering.
Folino, P. (2018). Strategie di guida e navigazione per un
veicolo marino autonomo di superficie. Master’s the-
sis, University of Calabria. Master’s thesis in Automa-
tion Engineering.
He, C., Feng, Z., and Ren, Z. (2012). Flocking of multi-
agents based on consensus protocol and pinning con-
trol. In Proceedings of the 10th World Congress on In-
telligent Control and Automation, pages 1311–1316.
IEEE.
Ismail, Z. H., Faudzi, A., and Dunnigan, M. W. (2014).
Fault-tolerant region-based control of an underwater
vehicle with kinematically redundant thrusters. Math-
ematical Problems in Engineering, 2014.
Khan, H. Z. I., Rajput, J., Ahmed, S., Sarmad, M., and
Sharjil, M. (2018). Robust control of overactuated au-
tonomous underwater vehicle. In 2018 15th Interna-
tional Bhurban Conference on Applied Sciences and
Technology (IBCAST), pages 269–275. IEEE.
Liu, X., Zhang, M., and Yao, F. (2018). Adaptive fault
tolerant control and thruster fault reconstruction for
autonomous underwater vehicle. Ocean Engineering,
155:10–23.
Patel, H. R. and Shah, V. A. (2018). A framework for fault-
tolerant control for an interacting and non-interacting
level control system using ai. In ICINCO (1), pages
190–200.
Tohidi, S. S., Yildiz, Y., and Kolmanovsky, I. (2016). Fault
tolerant control for over-actuated systems: An adap-
tive correction approach. In 2016 American Control
Conference (ACC), pages 2530–2535. IEEE.
Tohidi, S. S., Yildiz, Y., and Kolmanovsky, I. (2017). Adap-
tive control allocation for over-actuated systems with
actuator saturation. IFAc-PapersOnLine, 50(1):5492–
5497.
Wang, B. and Zhang, Y. (2017). An adaptive fault-
tolerant sliding mode control allocation scheme for
multirotor helicopter subject to simultaneous actuator
faults. IEEE Transactions on Industrial Electronics,
65(5):4227–4236.
Wang, Y., Wilson, P. A., Liu, X., et al. (2015). Adaptive
neural network-based backstepping fault tolerant con-
trol for underwater vehicles with thruster fault. Ocean
Engineering, 110:15–24.
Zhang, M., Liu, X., and Wang, F. (2017). Backstepping
based adaptive region tracking fault tolerant control
for autonomous underwater vehicles. The Journal of
Navigation, 70(1):184–204.
ICINCO 2020 - 17th International Conference on Informatics in Control, Automation and Robotics
88