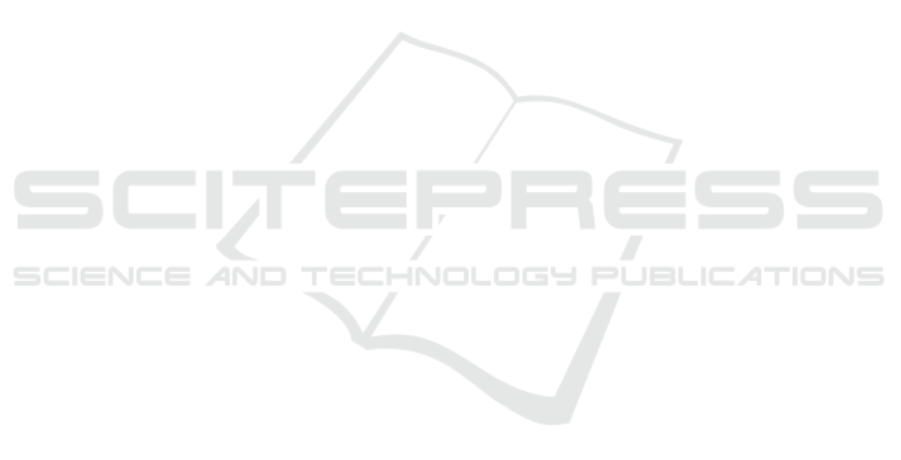
ACKNOWLEDGEMENTS
Work was supported by the RFBR (Russian Founda-
tion for Basic Research)(Grant No. 19-08-01234).
REFERENCES
Akhmetzyanov, A. (2019). Github repository.
https://github.com/AydarAkhmetzyanov/Deep-
Learning-based-cable-driven-robot-kinematics-
error-compensation-with-Transfer-Learning.
Alias, C., Nikolaev, I., Correa Magallanes, E. G., and
Noche, B. (2018). An overview of warehousing appli-
cations based on cable robot technology in logistics.
In 2018 IEEE International Conference on Service
Operations and Logistics, and Informatics (SOLI),
pages 232–239.
Duka, A.-V. (2014). Neural network based inverse kinemat-
ics solution for trajectory tracking of a robotic arm.
Procedia Technology, 12:2027.
Fadeev, M. and Maloletov, A. (2019). Control of the four-
cable-driven parallel robot with the help of the inverse
kinematic model. In Proceedings of the 6th Inter-
national Young Scientists Conference on Information
Technologies, Telecommunications and Control Sys-
tems (ITTCS 2019).
Izard, J.-B., Dubor, A., Herv, P.-E., Cabay, E., Culla, D.,
Rodriguez, M., and Barrado, M. (2017). Large-scale
3d printing with cable-driven parallel robots. page
6976.
Klimchik, A., Bondarenko, D., Pashkevich, A., Briot, S.,
and Furet, B. (2014). Compliance error compensation
in robotic-based milling. CoRR, abs/1409.6231.
Klimchik, A., Pashkevich, A., Chablat, D., and Hovland,
G. (2013). Compliance error compensation tech-
nique for parallel robots composed of non-perfect se-
rial chains. Robotics and Computer-Integrated Manu-
facturing, 29(2):385 – 393.
Krizhevsky, A., Sutskever, I., and Hinton, G. E. (2017). Im-
agenet classification with deep convolutional neural
networks. Commun. ACM, 60(6):8490.
Maloletov, A., Fadeev, M., and Klimchik, A. (2019). Error
analysis in solving the inverse problem of the cable-
driven parallel underactuated robot kinematics and
methods for their elimination. IFAC-PapersOnLine,
52:1156–1161.
Mikolov, T., Chen, K., Corrado, G., and Dean, J. (2013).
Efficient estimation of word representations in vector
space.
Morris, M. and Shoham, M. (2009). Applications and the-
oretical issues of cable-driven robots.
Narvekar, S. and Stone, P. (2018). Learning curriculum
policies for reinforcement learning.
Pane, Y., Nageshrao, S., Kober, J., and Babuska, R. (2019).
Reinforcement learning based compensation methods
for robot manipulators. Engineering Applications of
Artificial Intelligence, 78:236–247.
Rasheed, T., Long, P., and Caro, S. (2020). Wrench-
Feasible Workspace of Mobile Cable-Driven Parallel
Robots. Journal of Mechanisms and Robotics, 12(3).
031009.
Torrey, L., Shavlik, J., Walker, T., and Maclin, R. (2009).
Transfer Learning via Advice Taking, volume 262,
pages 147–170.
Wang, H., Zhang, R., Chen, W., Wang, X., and Pfeifer, R.
(2016). A cable-driven soft robot surgical system for
cardiothoracic endoscopic surgery: preclinical tests in
animals. Surgical Endoscopy, 31:3152–3158.
Wu, Y., Klimchik, A., Caro, S., Furet, B., and Pashkevich,
A. (2015). Geometric calibration of industrial robots
using enhanced partial pose measurements and design
of experiments. Robotics and Computer-Integrated
Manufacturing, 35:151 – 168.
Zhao, G., Zhang, P., Ma, G., and Xiao, W. (2019). System
identification of the nonlinear residual errors of an in-
dustrial robot using massive measurements. Robotics
and Computer-Integrated Manufacturing, 59:104 –
114.
Deep Learning with Transfer Learning Method for Error Compensation of Cable-driven Robot
559