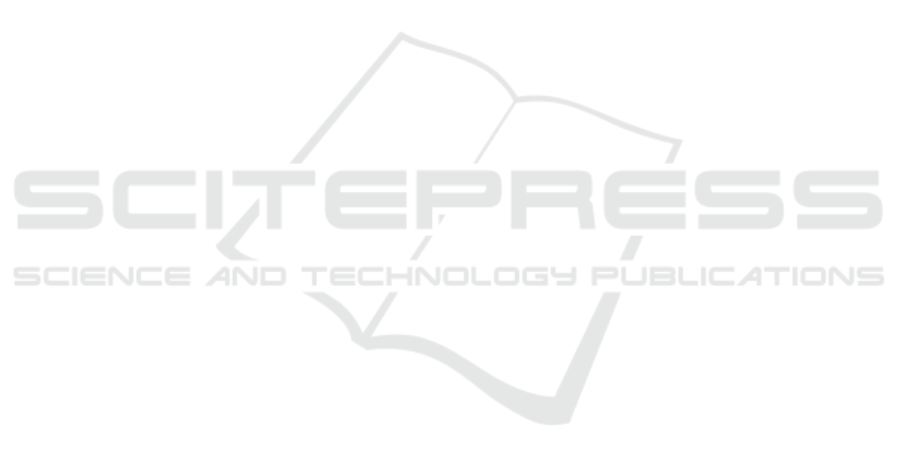
help to identify the relevant features for off-road nav-
igation. The control system of the vehicle could be
evaluated using the same simulated sensor set as the
real systems. Safety-critical navigation and inclina-
tion tests can be performed which is not possible for
the real system. The other scenario shows an excava-
tor in an open-pit mine (Fig. 9b). The evaluation of
rock recognition was done in simulation and the re-
sults transferred to the real machine. Periodical tests
with the real machine show that the developed meth-
ods are easily transferable to the real world.
7 CONCLUSION
The paper presented a simulation framework tailored
to autonomous commercial vehicles operating in clut-
tered off-road environments. For this purpose, it in-
tegrated the Unreal Engine 4 and the robot control
framework Finroc. Short-comings of current simu-
lation systems have been identified, starting with a
review of the state of the art in robot simulation.
Next, the integration of frameworks and communica-
tion were explained. Different sensors, special driv-
ing kinematics, and complex body actuation were
described and an application overview provided. It
could be observed that the simulation and real-world
testing gap could be significantly reduced.
Future and current work aims to integrate more
sensor systems, e.g. radar, and disturbances, like real-
istic ferro-magnetic behavior of vehicle frames. Fur-
ther, automated testing should be regarded that allows
a statistical evaluation of the control behavior and al-
lows unit testing of control functionality.
ACKNOWLEDGEMENTS
Thanks to A. Matheis for the project work Realis-
tic Simulation of GPS Signal Quality for Autonomous
Robots by using Virtual Satellites, Project Report,
Robotics Research Lab, TU Kaiserslautern, unpub-
lished, supervised by P. Wolf, Feb. 13, 2018.
REFERENCES
Aguero, C., Koenig, N., Chen, I., Boyer, H., Peters, S.,
Hsu, J., Gerkey, B., Paepcke, S., Rivero, J., Manzo,
J., Krotkov, E., and Pratt, G. (2015). Inside the virtual
robotics challenge: Simulating real-time robotic dis-
aster response. Automation Science and Engineering,
IEEE Transactions on, 12(2):494–506.
Carpin, S., Lewis, M., Wang, J., Balakirsky, S., and Scrap-
per, C. (2007). Usarsim: a robot simulator for re-
search and education. In Robotics and Automation,
2007 IEEE International Conference on, pages 1400
– 1405. IEEE.
Dosovitskiy, A., Ros, G., Codevilla, F., Lopez, A., and
Koltun, V. (2017). Carla: An open urban driving sim-
ulator. In 1st Conference on Robot Learning (CoRL
2017), pages 1–16, Mountain View, United States.
Freese, M., Singh, S., Ozaki, F., and Matsuhira, N. (2010).
Virtual robot experimentation platform v-rep: A ver-
satile 3d robot simulator. In N. Ando et. al., edi-
tor, International Conference on Simulation, Model-
ing and Programming for Autonomous Robots (SIM-
PAR), volume 6472 of Lecture Notes in Computer Sci-
ence, pages 51–62. Springer.
Goodin, C., Carrillo, J. T., McInnis, D. P., Cummins, C. L.,
Durst, P. J., Gates, B. Q., and Newell, B. S. (2017).
Unmanned ground vehicle simulation with the virtual
autonomous navigation environment. In 2017 Interna-
tional Conference on Military Technologies (ICMT),
pages 160–165.
Goodin, C., Doude, M., Hudson, C., and Carruth, D. (2018).
Enabling off-road autonomous navigation-simulation
of lidar in dense vegetation. Electronics, 7:154.
Groll, T., Hemer, S., and Berns, K. (2015). Autonomous
backhoe loader. In 6. Fachtagung Baumaschinen-
technik 2015: Maschinen, Prozesse, Vernetzung, vol-
ume 49 of Schriftenreihe der Forschungsvereinigung
Bau- und Baustoffmaschinen e.V., pages 351–366.
Guerra, W., Tal, E., Murali, V., Ryou, G., and Karaman, S.
(2019). Flightgoggles: Photorealistic sensor simula-
tion for perception-driven robotics using photogram-
metry and virtual reality. CoRR, abs/1905.11377.
Hirschm
¨
uller, H. (2008). Stereo processing by semiglobal
matching and mutual information. IEEE Transac-
tions on pattern analysis and machine intelligence,
30(2):328–341.
Jiang, F. and Hao, Q. (2019). Pavilion: Bridging photo-
realism and robotics. In 2019 International Con-
ference on Robotics and Automation (ICRA), pages
8285–8290.
M
¨
uller, M., Casser, V., Lahoud, J., Smith, N., and Ghanem,
B. (2017). Sim4cv: A photo-realistic simulator for
computer vision applications. International Journal
of Computer Vision.
Reichardt, M., F
¨
ohst, T., and Berns, K. (2013). On software
quality-motivated design of a real-time framework for
complex robot control systems. In Proceedings of the
7th International Workshop on Software Quality and
Maintainability (SQM), in conjunction with the 17th
European Conference on Software Maintenance and
Reengineering (CSMR), Genoa, Italy.
Santerre, R., Geiger, A., and Banville, S. (2017). Geometry
of gps dilution of precision: Revisited. GPS Solut.,
21(4):1747–1763.
Shah, S., Dey, D., Lovett, C., and Kapoor, A. (2017). Air-
sim: High-fidelity visual and physical simulation for
autonomous vehicles. In Field and Service Robotics,
pages 621–635. Springer.
Wettach, J., Schmidt, D., and Berns, K. (2010). Sim-
ulating vehicle kinematics with simvis3d and new-
ton. In Proceedings of the 2nd International Confer-
ence on Simulation, Modeling, and Programming for
Autonomous Robots (SIMPAR’10), pages 156–167,
Darmstadt, Germany. Springer-Verlag Berlin.
SIMULTECH 2020 - 10th International Conference on Simulation and Modeling Methodologies, Technologies and Applications
278