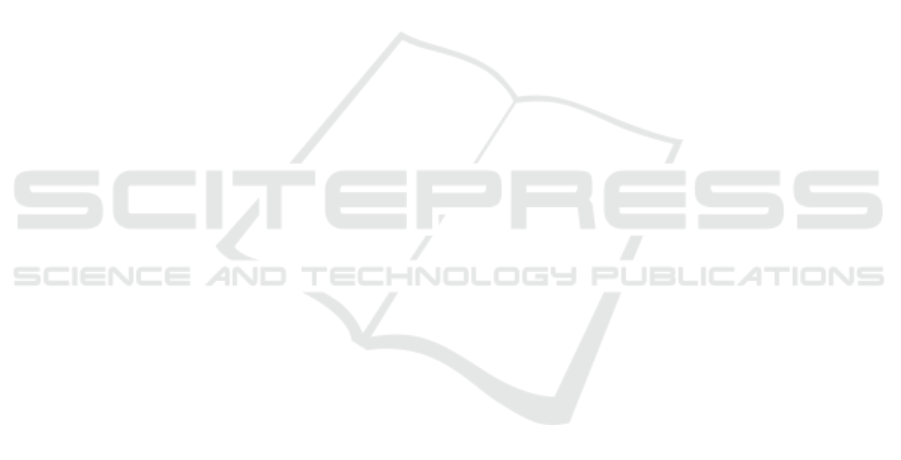
lation of a huge mathematical program, which can-
not be solved directly by current mathematical pro-
gramming solvers. Finally, the use of classical de-
composition methods, such as the Benders’ decom-
position approach, is not straightforward as it would
imply sub-problems involving binary and/or integer
decision variables. The mixed-integer program mod-
eling the problem is thus computationally intractable
as such.
However, solution approaches exploiting the nat-
ural hierarchy between decisions relative to the sys-
tem design and decisions relative to the daily op-
eration schedules have been investigated in several
works. Weber et al. (2007) thus studied the optimal
design of a multi-energy system. A two-level opti-
mization method is implemented. The master opti-
mization level explores the set of possible system de-
signs with the use of an evolutionary algorithm. For
each considered system design, the slave optimiza-
tion level calculates the optimal cost by linear pro-
gramming. This approach does not provide a guaran-
teed optimal solution and the formulation of the slave
sub-problems as linear programs does not allow to ac-
curately model the way the system operates in prac-
tice. Iyer and Grossmann (1998) also use a bi-level
method to optimize the choice and sizes of equipment
for utility systems. At the design optimization level,
the problem aims at fixing the system infrastructure.
All binary decision variables relative to the opera-
tion schedules are removed from this master problem.
Each time a potential infrastructure is found, the op-
eration optimization level solves a set of single-period
scheduling sub-problems taking the current system
infrastructure as input data. Design cuts are used to
tighten the gap between the solutions found at both
levels. Yokoyama et al. (2015) consider local energy
supply systems and propose a customized Branch &
Cut algorithm exploiting the hierarchical relationship
between the design and operation decision variables
of the mathematical program. The upper level prob-
lem corresponds to the initial optimization problem
in which all operational integer and binary variables
are kept but relaxed to be continuous. Each time an
integer feasible solution is found at the upper level,
a sequence of single-period independent operation
sub-problems is solved to check the feasibility and
value of the current design solution. Note that Iyer
and Grossmann (1998) and Yokoyama et al. (2015)
both consider a single-phase variant of the problem,
i.e. a variant in which all design decisions are one-
shot decisions. Moreover, their design infrastruc-
ture did not allow short-term intra-day energy stor-
age. This allows them to consider single-period (i.e.
one-hour) scheduling sub-problems rather than multi-
period (i.e. 24-hour) scheduling sub-problems, which
significantly decreases the size of these sub-problems.
In the present work, we propose a solution ap-
proach for the optimal design, over a multi-phase in-
vestment horizon, of a local district cooling system
in which intra-day ice storage is allowed. This ap-
proach relies on three key elements. First, we seek
to reduce the size of the initial optimization problem.
We thus consider a deployment plan involving a lim-
ited number of phases, some of which spanning sev-
eral years. Moreover, we use the clustering approach
described in Zatti et al. (2019) to select a small set
of typical days to represent with the smallest pos-
sible loss of accuracy the various conditions under
which the system will be operated. Second, we build
a piecewise linear approximation of the performance
curves of each chiller and propose a way to exploit
their convexity to reduce the size of the formulation
of the operation scheduling sub-problems. This re-
sults in the formulation of a large-size mixed-integer
linear program (MILP). Thirdly, we develop an ex-
act solution algorithm based on the hierarchical de-
composition method recently proposed by Yokoyama
et al. (2015) to solve this MILP.
The remaining of the paper is organized as fol-
lows. Section 2 gives a detailed description of the
problem under study. In Section 3, the approximation
of the nonlinear performance curves and the cluster-
ing method used to identify typical days are first pre-
sented. The formulation of the optimization problem
as an MILP is then provided. Section 4 introduces the
hierarchical decomposition algorithm used to solve
this MILP. In Section 5, the results of our preliminary
computational experiments based on a real-life case
study in China are reported.
2 PROBLEM PRESENTATION
Before the actual construction of a cooling system,
a thorough and reliable system design is necessary.
The system design consists in selecting the appropri-
ate chillers and in sizing the ice storage capacity to
be installed. The main objective is to design a sys-
tem which will be able to meet the clients’ cooling
demand at all time while leading to the lowest long-
term investments and operation costs.
2.1 Resources
A chiller is a machine that removes heat from a liq-
uid by using a variety of techniques such as vapor-
compression. We consider here electric-powered
chillers which are used to cool water. These chillers
ICORES 2021 - 10th International Conference on Operations Research and Enterprise Systems
318