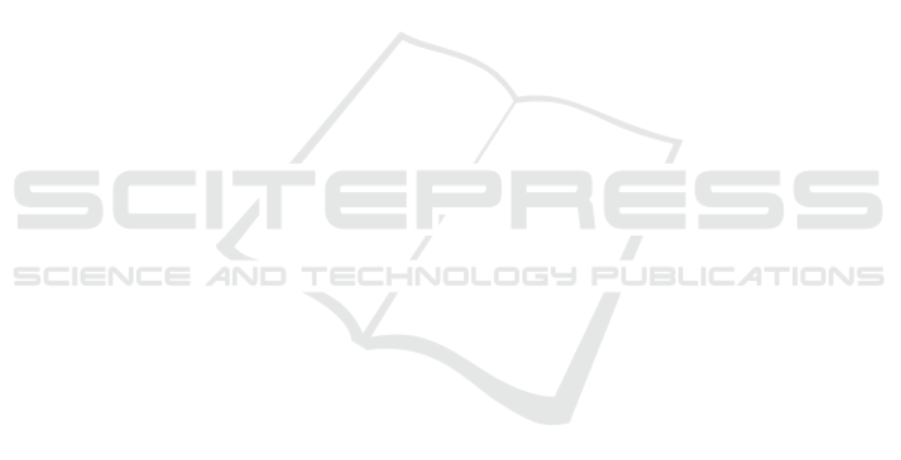
CPPS and products.
We introduced the CPPS-RA approach for link-
ing effects and causes to assets in a multi-view CEN
to validate informal Cause-Effect hypotheses and ex-
plore potential causes for risks to the CPPS and prod-
ucts, even across discipline boundaries. The CEN
model elements provide the foundation for specifying
the engineering and operational data required for test-
ing the hypotheses. We defined the CPPS-RA meta-
model to represent core concepts for integrated CPPS
engineering views for risk assessment. We evaluated
the CPPS-RA approach in a feasibility study with a
conceptual prototype with the use case Screwing Sys-
tem, which is representative for discrete manufactur-
ing.
The CPPS-RA approach provides the following
benefits: (1) Causes linked to CPPS engineering data
elements in a CEN facilitate the automated evalua-
tion of hypotheses based on data, even across disci-
pline boundaries; and (2) the CEN allows validating
the cause-effect pathway, i.e., to what extent a CEN
element linked to a cause is connected to the CEN el-
ement linked to an effect.
Future Work. Combination of model- and data-
driven CPPS risk assessment. Building on the CPPS-
RA results of hypotheses linked to a CEN, we plan
to explore the combination of model- and data-driven
CPPS analysis based on data from CPPS engineering
and operation.
Security and Countermeasures. Going beyond
product quality concerns, we plan to combine the risk
assessment regarding functional quality and informa-
tion security aspects with iterative cause-effect anal-
ysis to address the risk for large CPPSs that are part
of the critical infrastructure. We plan to extend the
CPPS-RA approach to represent countermeasures that
address weaknesses of assets or links to mitigate risks
to a CPPS or product. For more details on future work
refer to (Biffl et al., 2020).
ACKNOWLEDGEMENTS
The financial support by the Christian Doppler Re-
search Association, the Austrian Federal Ministry for
Digital and Economic Affairs and the National Foun-
dation for Research, Technology and Development is
gratefully acknowledged.
REFERENCES
Atkinson, C., Tunjic, C., and M
¨
oller, T. (2015). Fundamen-
tal realization strategies for multi-view specification
environments. In 2015 IEEE 19th Int. Enterprise Dis-
tributed Object Computing Conf., pages 40–49.
Biffl, S., L
¨
uder, A., and Gerhard, D., editors (2017). Multi-
Disciplinary Engineering for Cyber-Physical Produc-
tion Systems. Springer.
Biffl, S., L
¨
uder, A., Meixner, K., Rinker, F., Engelbrecht,
C., Eckhart, M., and Winkler, D. (2020). Multi-View-
Model Risk Assessment for Positioning and Joining
Simulation (Case Study). Technical Report CDL-SQI
2020-05 CDL-SQI-2020-05, CDL-SQI, Institute for
Information Systems Engineering, TU Wien. https:
//qse.ifs.tuwien.ac.at/cdl-sqi-2020-05/.
Biffl, S., L
¨
uder, A., Rinker, F., Waltersdorfer, L., and Win-
kler, D. (2019). Engineering data logistics for agile
automation systems engineering. In Sec. and Quality
in Cyber-Physical Sys. Eng., pages 187–225. Springer.
DIN60812 (2015). Din en 60812:2015-08: Failure mode
and effects analysis (fmea).
Drath, R., Lueder, A., Peschke, J., and Hundt, L. (2008).
Automationml-the glue for seamless automation engi-
neering. In Emerging Tech. and Factory Automation.
ETFA 2008. IEEE Int. Conf., pages 616–623. IEEE.
Foehr, M. (2013). Integrated consideration of product qual-
ity within factory automation systems. dissertation,
Otto v. Guericke Universit
¨
at, Germany.
Henning, K. (2013). Recommendations for implement-
ing the strategic initiative INDUSTRIE 4.0. acatech–
National Academy of Science and Engineering.
H
¨
ofig, K., Klein, C., Rothbauer, S., Zeller, M., Vorderer,
M., and Koo, C. H. (2019). A meta-model for process
failure mode and effects analysis (pfmea). In 2019
24th IEEE Int. Conf. on Emerging Tech. and Factory
Automation (ETFA), pages 1199–1202. IEEE.
Hopkin, P. (2018). Fundamentals of Risk Management: Un-
derstanding, Evaluating and Implementing Effective
Risk Management. Kogan Page, 5th edition edition.
IEC 62714 (2018). Engineering data exchange format for
use in industrial automation systems engineering –
automation markup language. Int. Standard, Second
Edition, Int. Electrotechnical Commission, Geneva, 2.
Kaiser, B., Liggesmeyer, P., and M
¨
ackel, O. (2003). A new
component concept for fault trees. In Proc. Wsh. on
Safety critical sys. and sw.-Volume 33, pages 37–46.
Liu, H.-C., Liu, L., and Liu, N. (2013). Risk evaluation
approaches in failure mode and effects analysis: A lit-
erature review. Expert sys. with app.s, 40(2):828–838.
L
¨
uder, A., Pauly, J.-L., Rinker, F., and Biffl, S. (2019).
Data exchange logistics in engineering networks ex-
ploiting automated data integration. In IEEE ETFA,
pages 657–664. IEEE.
Meier, J., Klare., H., Tunjic., C., Atkinson., C., Burger.,
E., Reussner., R., and Winter., A. (2019). Single
underlying models for projectional multi-view envi-
ronments. In Proc. MODELSWARD, pages 119–130.
SciTePress.
Sitte, J. and Winzer, P. (2010). Demand-compliant design.
IEEE Trans. on Systems, Man, and Cybernetics-Part
A: Systems and Humans, 41(3):434–448.
Stamatis, D. (2019). Risk Management Using Failure Mode
and Effect Analysis (FMEA). Quality Press.
MODELSWARD 2021 - 9th International Conference on Model-Driven Engineering and Software Development
170