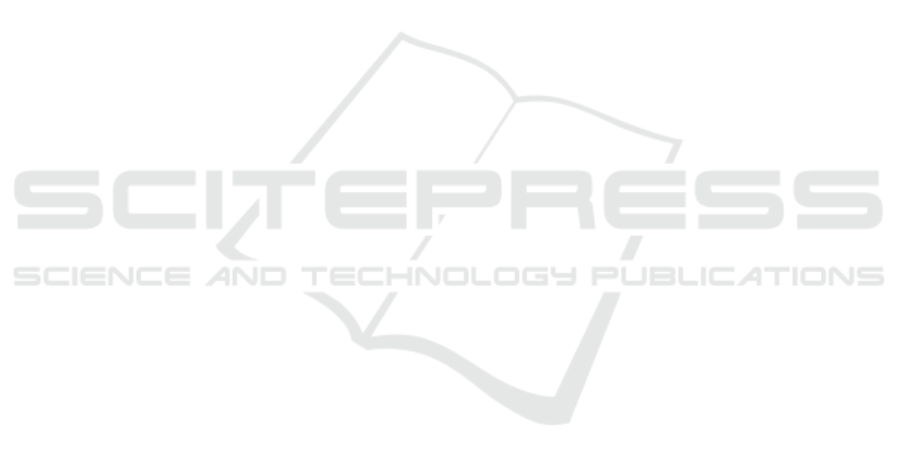
Coelen, V., Deppe, C., Gomaa, M., Hofmann, T., Karras,
U., Niemueller, T., Rohr, A., and Ulz, T. (2019). The
RoboCup Logistics League Rulebook for 2019.
Coles, A., Coles, A., Fox, M., and Long, D. (2010).
Forward-chaining Partial-order Planning. In Pro-
ceedings of the 20th International Conference on In-
ternational Conference on Automated Planning and
Scheduling (ICAPS), pages 42–49. AAAI Press.
Gebser, M., Kaminski, R., Kaufmann, B., and Schaub, T.
(2019). Multi-shot ASP solving with clingo. Theory
and Practice of Logic Programming, 19(1):27–82.
Hertle, A. and Nebel, B. (2018). Efficient auction based
coordination for distributed multi-agent planning in
temporal domains using resource abstraction. In Pro-
ceedings of the 41st German Conference on Artificial
Intelligence (KI).
Hofmann, T., Matar
´
e, V., Neumann, T., Sch
¨
onitz, S., Henke,
C., Limpert, N., Niemueller, T., Ferrein, A., Jeschke,
S., and Lakemeyer, G. (2018). Enhancing Software
and Hardware Reliability for a Successful Partici-
pation in the RoboCup Logistics League 2017. In
RoboCup 2017: Robot World Cup XXI, pages 486–
497. Springer International Publishing.
Ingrand, F., Chatila, R., Alami, R., and Robert, F. (1996).
PRS: A High Level Supervision and Control Lan-
guage for Autonomous Mobile Robots. In Pro-
ceedings of the IEEE International Conference on
Robotics and Automation.
Kitano, H., Asada, M., Kuniyoshi, Y., Noda, I., and Osawa,
E. (1997). RoboCup: The Robot World Cup Initiative.
In Proceedings of the 1st International Conference on
Autonomous Agents.
Leofante, F.,
´
Abrah
´
am, E., Niemueller, T., Lakemeyer,
G., and Tacchella, A. (2019). Integrated Synthe-
sis and Execution of Optimal Plans for Multi-Robot
Systems in Logistics. Information Systems Frontiers,
21(1):87–107.
Niemueller, T., Ferrein, A., and Lakemeyer, G. (2010).
A Lua-based behavior engine for controlling the hu-
manoid robot Nao. In RoboCup 2009: Robot Soccer
World Cup XIII.
Niemueller, T., Hofmann, T., and Lakemeyer, G. (2018).
CLIPS-based Execution for PDDL Planners. In 2nd
ICAPS Workshop on Integrated Planning, Acting, and
Execution (IntEx).
Niemueller, T., Hofmann, T., and Lakemeyer, G. (2019).
Goal reasoning in the CLIPS Executive for integrated
planning and execution. In Proceedings of the 29th
International Conference on Automated Planning and
Scheduling (ICAPS), pages 754–763.
Niemueller, T., Karpas, E., Vaquero, T., and Timmons, E.
(2016a). Planning competition for logistics robots in
simulation. In 4th ICAPS Workshop on Planning and
Robotics (PlanRob).
Niemueller, T., Lakemeyer, G., and Ferrein, A. (2013). In-
cremental task-level reasoning in a competitive fac-
tory automation scenario. In AAAI Spring Symposium
on Designing Intelligent Robots.
Niemueller, T., Lakemeyer, G., and Ferrein, A. (2015). The
RoboCup Logistics League as a Benchmark for Plan-
ning in Robotics. In 2nd ICAPS Workshop on Plan-
ning in Robotics (PlanRob).
Niemueller, T., Neumann, T., Henke, C., Sch
¨
onitz, S.,
Reuter, S., Ferrein, A., Jeschke, S., and Lakemeyer,
G. (2017a). Improvements for a Robust Production
in the RoboCup Logistics League 2016. In RoboCup
2016: Robot World Cup XX, pages 589–600. Springer
International Publishing.
Niemueller, T., Zug, S., Schneider, S., and Karras, U.
(2016b). Knowledge-Based Instrumentation and Con-
trol for Competitive Industry-Inspired Robotic Do-
mains. KI - K
¨
unstliche Intelligenz, 30(3):289–299.
Niemueller, T., Zwilling, F., Lakemeyer, G., L
¨
obach, M.,
Reuter, S., Jeschke, S., and Ferrein, A. (2017b).
Cyber-Physical System Intelligence. In Industrial In-
ternet of Things: Cybermanufacturing Systems, pages
447–472. Springer International Publishing.
Roberts, M., Apker, T., Johnson, B., Auslander, B., Well-
man, B., and Aha, D. W. (2015). Coordinating robot
teams for disaster relief. In Proceedings of the 28th
Florida Artificial Intelligence Research Society Con-
ference. AAAI Press.
Roberts, M., Hiatt, L., Coman, A., Choi, D., Johnson, B.,
and Aha, D. (2016a). ActorSim, A Toolkit for Study-
ing Cross-Disciplinary Challenges in Autonomy. In
AAAI Fall Symposium on Cross-Disciplinary Chal-
lenges for Autonomous Systems.
Roberts, M., Shivashankar, V., Alford, R., Leece, M.,
Gupta, S., and Aha, D. W. (2016b). Goal Reasoning,
Planning, and Acting with ActorSim, The Actor Sim-
ulator. In Proceedings of the 4th Annual Conference
on Advances in Cognitive Systems, volume 4.
Roberts, M., Vattam, S., Alford, R., Auslander, B., Karneeb,
J., Molineaux, M., Apker, T., Wilson, M., McMahon,
J., and Aha, D. W. (2014). Iterative Goal Refinement
for Robotics. In 1st ICAPS Workshop on Planning in
Robotics (PlanRob).
Sch
¨
apers, B., Niemueller, T., and Lakemeyer, G.
(2018). ASP-based time-bounded planning for logis-
tics robots. In Proceedings of the 28th International
Conference on Automated Planning and Scheduling
(ICAPS).
Shivashankar, V., Kuter, U., Nau, D., and Alford, R. (2012).
A Hierarchical Goal-based Formalism and Algorithm
for Single-agent Planning. In Proceedings of the
11th International Conference on Autonomous Agents
and Multiagent Systems, pages 981–988. International
Foundation for Autonomous Agents and Multiagent
Systems.
Ulz, T., Ludwiger, J., and Steinbauer, G. (2019). A
Robust and Flexible System Architecture for Fac-
ing the RoboCup Logistics League Challenge. In
RoboCup 2018: Robot World Cup XXII, pages 488–
499. Springer International Publishing.
Wilson, M. A., McMahon, J., Wolek, A., Aha, D. W.,
and Houston, B. H. (2018). Goal reasoning for au-
tonomous underwater vehicles: Responding to unex-
pected agents. AI Communications, 31(2):151–166.
Multi-Agent Goal Reasoning with the CLIPS Executive in the RoboCup Logistics League
91