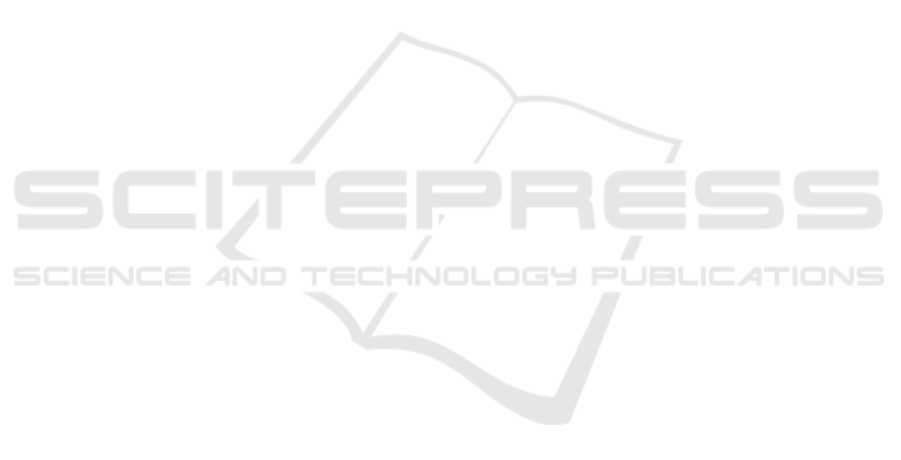
or partially satisfied tends towards zero. The average
of non-priority pickup requests is greater than the av-
erage of priority pickup requests since the majority of
sites served are the priority in the delivery and not in
the collection. The total time is the biggest despite the
distance is no longer this is due to the bigger service
time.
We find that the pickup profit Pp
j
Eq(6) allows
us to serve a large number of pickup priority sites as
well as delivery priority sites, since, most of the sites
served, in this case, are the priority in pickup and de-
liveries. For all the criteria we notice that the average
number of partially satisfying pickup requests is very
small since the quantity of Big-bag waste generated
by construction sites is low below 3/4 vehicle capac-
ity, which allows them to be collected easily.
Our heuristic SBH combines all the criteria de-
scribed previously in a weighted manner according
to Table 1. This combination noted H in Figures 1
and 2 allows obtaining good results on all compara-
tive metrics. Indeed, our heuristic satisfies the highest
number of priority delivery requests 34.2, and a sig-
nificant number of non-priority delivery requests 5.8.
The average pickup requests totally satisfied is also
important compared to the other criteria. The average
amount of pallet delivery and pallet pickup are com-
parable to the ones obtained by d
i, j
and T
i, j
. The total
time duration taken by our heuristic is highest because
the priority sites are not necessarily nearby in addition
to the time of loading and unloading of vehicles.
5 CONCLUSION
In the present paper, we described a new variant of
the vehicle routing problem with pickup and deliv-
ery, named MTPDSPMTW for multi-trip pickup and
delivery problem, with split loads, profits, and multi-
ple time windows. This new variant allows modelling
a real-world problem encountered in the construction
industry and combines for the first time characteristics
that have been studied separately in the literature on
vehicle routing problems. These are multi-trip, split
loads, profit, time window and the use of heteroge-
neous vehicles. The issue is that not all customers can
be served because the number of vehicles is limited,
and partial service is allowed, so the difficulty arises
in selecting the customers to be included in the tour
while prioritizing service satisfaction for customers
with a high priority (maximizing profit), and allow-
ing non-priority customers to be included to to fill the
residual capacity and/or time of the vehicles. We pro-
posed a new insertion score based on six criterai, that
is embedded in a construction heuristic (SBH). Nu-
merical results on new instances show that all pro-
posed criteria have a non-zero weight in the score and
that the combination of all criteria gives the most sig-
nificant results in relation to the objective of maxi-
mizing the number of priority customers completely
satisfied. The effectiveness of these results has been
validated by our industrial partners, and have been re-
tained for further experimentation. The next step is
to develop metaheuristic approaches to improve ob-
tained results.
REFERENCES
Chentli, H., Ouafi, R., and Ramdane-Cherif-Khettaf, W.
(2018). A selective adaptive large neighborhood
search heuristic for the profitable tour problem with
simultaneous pickup and delivery services. RAIRO -
Operations Research, 52(4):1295–1328.
Haddad, M., Martinelli, R., Vidal, T., Ochi, L., Mar-
tins, S., Souza, M., and Hartl, R. (2018). Large
neighborhood-based metaheuristic and branch-and-
price for the pickup and delivery problem with split
loads. European Journal of Operational Research.
L
´
opez-Ib
´
a
˜
nez, M., Dubois-Lacoste, J., P
´
erez C
´
aceres, L.,
Birattari, M., and St
¨
utzle, T. (2016). The irace pack-
age: Iterated racing for automatic algorithm configu-
ration. Operations Research Perspectives, 3:43 – 58.
Nagy, G., Wassan, N. A., Speranza, M. G., and Archetti,
C. (2015). The vehicle routing problem with divis-
ible deliveries and pickups. Transportation Science,
49(2):271–294.
Nowak, M., Ergun, z., and White, C. C. (2008). Pickup
and delivery with split loads. Transportation Science,
42(1):32–43.
Parragh, S., Doerner, K., and Hartl, R. (2008). A survey on
pickup and delivery problems: Part ii: Transportation
between pickup and delivery locations. Journal f
¨
ur
Betriebswirtschaft, 58:81–117.
Parragh, S. N., Doerner, K. F., and Hartl, R. F. (2007). A
survey on pickup and delivery models part ii : Trans-
portation between pickup and delivery locations.
Sun, P., Veelenturf, L. P., Hewitt, M., and Van Woensel, T.
(2020). Adaptive large neighborhood search for the
time-dependent profitable pickup and delivery prob-
lem with time windows. Transportation Research Part
E: Logistics and Transportation Review, 138:101942.
Yin, C., Bu, L., and Gong, H. (2013). Mathematical model
and algorithm of split load vehicle routing problem
with simultaneous delivery and pickup. International
Journal of Innovative Computing, Information and
Control, 9:4497–4508.
Multi-trip Pickup and Delivery Problem, with Split Loads, Profits and Multiple Time Windows to Model a Real Case Problem in the
Construction Industry
207