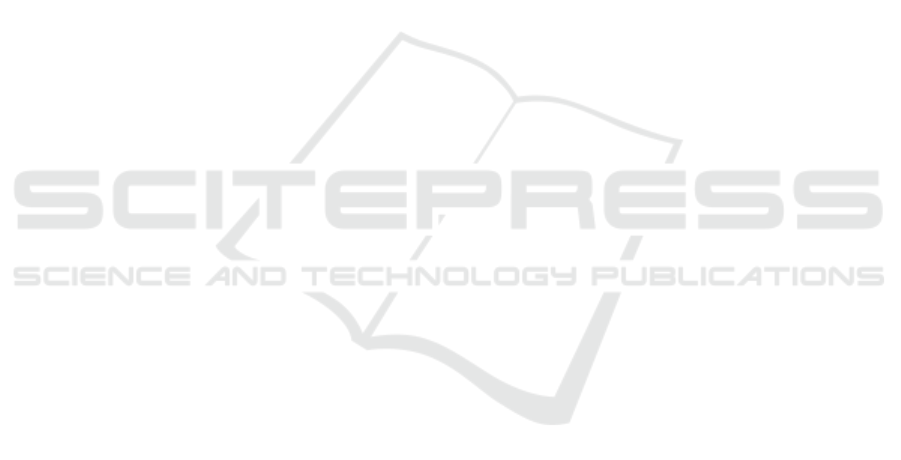
ACKNOWLEDGEMENT
The financial support by the Christian Doppler Re-
search Association, the Austrian Federal Ministry for
Digital & Economic Affairs and the National Foun-
dation for Research, Technology and Development is
gratefully acknowledged.
REFERENCES
Atkinson, C., Burger, E., Meier, J., Reussner, R., and
Winter, A. (2019). Preface to the 1st workshop on
view-oriented software engineering (vose). In 2019
ACM/IEEE 22nd International Conference on Model
Driven Engineering Languages and Systems Compan-
ion (MODELS-C), pages 370–370. IEEE.
Atkinson, C., Gerbig, R., and K
¨
uhne, T. (2014). Comparing
multi-level modeling approaches. In MULTI@ MoD-
ELS, pages 53–61.
Batory, D. S. and Altoyan, N. (2020). Aocl : A Pure-Java
Constraint and Transformation Language for MDE.
In Proceedings of the 8th International Conference
on Model-Driven Engineering and Software Develop-
ment - Volume 1: MODELSWARD,, pages 319–327.
SCITEPRESS.
Biffl, S., L
¨
uder, A., Rinker, F., and Waltersdorfer, L.
(2019). Efficient engineering data exchange in multi-
disciplinary systems engineering. In International
Conference on Advanced Information Systems Engi-
neering, pages 17–31. Springer.
Bruneliere, H., Perez, J. G., Wimmer, M., and Cabot, J.
(2015). Emf views: A view mechanism for integrating
heterogeneous models. In International Conference
on Conceptual Modeling, pages 317–325. Springer.
Dotoli, M., Fay, A., Mi
´
skowicz, M., and Seatzu, C. (2019).
An overview of current technologies and emerging
trends in factory automation. International Journal
of Production Research, 57(15-16):5047–5067.
Ebert, C., Gallardo, G., Hernantes, J., and Serrano, N.
(2016). Devops. Ieee Software, 33(3):94–100.
Feldmann, S., Kernschmidt, K., Wimmer, M., and Vogel-
Heuser, B. (2019). Managing inter-model inconsis-
tencies in model-based systems engineering: Appli-
cation in automated production systems engineering.
Journal of Systems and Software, 153:105–134.
Garcia, J. and Cabot, J. (2018). Stepwise adoption of con-
tinuous delivery in model-driven engineering. In In-
ternational Workshop on Software Engineering As-
pects of Continuous Development and New Paradigms
of Software Production and Deployment, pages 19–
32. Springer.
Grangel-Gonz
´
alez, I. (2016). Semantic data integration for
industry 4.0 standards. In European Knowledge Ac-
quisition Workshop, pages 230–237. Springer.
Jouault, F., Allilaire, F., B
´
ezivin, J., and Kurtev, I. (2008).
ATL: A model transformation tool. Science of com-
puter programming, 72(1-2):31–39.
L
¨
uder, A., Kirchheim, K., Pauly, J., Biffl, S., Rinker, F., and
Waltersdorfer, L. (2019). Supporting the data model
integrator in an engineering network by automating
data integration. In 2019 IEEE 17th International
Conference on Industrial Informatics (INDIN), vol-
ume 1, pages 1229–1234.
Ponsard, C., Darquennes, D., Ramon, V., and Deprez, J.-C.
(2020). Assessment of EMF Model to Text Generation
Strategies and Libraries in an Industrial Context. In
MODELSWARD, pages 433–440.
Rinker, F., Waltersdorfer, L., Meixner, K., and Biffl, S.
(2019). Towards support of global views on common
concepts employing local views. In 24th IEEE Inter-
national Conference on Emerging Technologies and
Factory Automation, ETFA 2019, Zaragoza, Spain,
September 10-13, 2019, pages 1686–1689. IEEE.
Sabou, M., Ekaputra, F. J., and Biffl, S. (2017). Seman-
tic web technologies for data integration in multi-
disciplinary engineering. In Multi-Disciplinary En-
gineering for Cyber-Physical Production Systems,
pages 301–329. Springer.
Sanchis, R., Garc
´
ıa-Perales,
´
O., Fraile, F., and Poler, R.
(2020). Low-code as enabler of digital transforma-
tion in manufacturing industry. Applied Sciences,
10(1):12.
Scheeren, I. and Pereira, C. E. (2014). Combining
model-based systems engineering, simulation and
domain engineering in the development of indus-
trial automation systems: Industrial case study.
In 2014 IEEE 17th International Symposium on
Object/Component/Service-Oriented Real-Time Dis-
tributed Computing, pages 40–47. IEEE.
Strahilov, A. and H
¨
ammerle, H. (2017). Engineering work-
flow and software tool chains of automated produc-
tion systems. In Multi-Disciplinary Engineering for
Cyber-Physical Production Systems, pages 207–234.
Springer.
Tisi, M., Mottu, J., Kolovos, D. S., de Lara, J., Guerra,
E., Ruscio, D. D., Pierantonio, A., and Wimmer, M.
(2019). Lowcomote: Training the next generation of
experts in scalable low-code engineering platforms.
volume 2405 of CEUR Workshop Proceedings, pages
73–78. CEUR-WS.org.
Toulm
´
e, A. (2006). Presentation of EMF Compare Utility.
In Eclipse Modeling Symposium, pages 1–8.
Tunjic, C. and Atkinson, C. (2015). Synchronization of pro-
jective views on a single-underlying-model. In Pro-
ceedings of the 2015 Joint MORSE/VAO Workshop on
Model-Driven Robot Software Engineering and View-
based Software-Engineering, pages 55–58.
Waltersdorfer, L., Rinker, F., Kathrein, L., and Biffl, S.
(2020). Experiences with technical debt and manage-
ment strategies in production systems engineering. In
Proceedings of the 3rd International Conference on
Technical Debt, pages 41–50.
Wortmann, A., Barais, O., Combemale, B., and Wimmer,
M. (2020). Modeling languages in Industry 4.0: an ex-
tended systematic mapping study. Software and Sys-
tems Modeling, 19(1):67–94.
Continuous Integration in Multi-view Modeling: A Model Transformation Pipeline Architecture for Production Systems Engineering
293