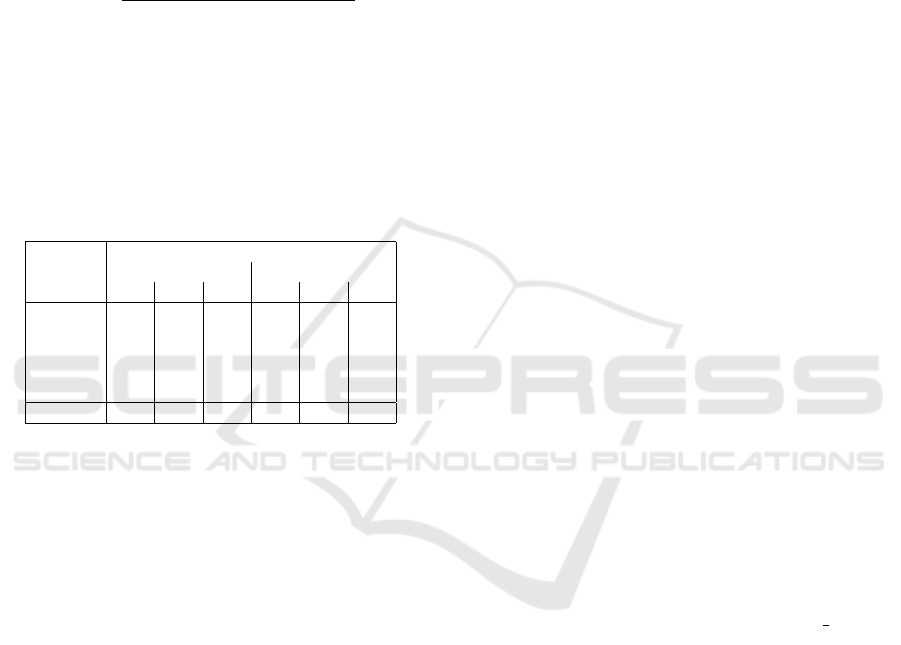
covered by the carts. Also under this respect Pol-
icy 1 gives the best result, returning an average cart
mileage 15,7% shorter than that attained by Policy 2
(last row of Table 3). As for route length distribution,
the largest cart mileage with Policy 1 is from 11,6 to
12,9 km shorter than with Policy 2. In absolute terms,
Policy 1 also improves the mileage unbalance of Pol-
icy 2 of amounts ranging between 15,4% and 16,8%.
However, the relative unbalance
U
R
=
longest route − shortest route
longest route
is quite large with both policies, from 48.0% to 51.6%
(51.2% with Policy 2). To correctly read this informa-
tion one has however to consider that program (1)-(3)
tends to assign less lots to longer routes, so as to com-
pensate travel and load/unload time.
Table 3: Mileage balance. Kilometres per cart to complete
operation: average, maximum and unbalance (diff.) per
sample and scheduling policy.
cart mileage (km)
sample id. Policy 1 Policy 2
avg. max diff. avg. max diff.
1 41.4 63.9 31.5 49,5 76.7 37.8
2 42.6 64.2 30.8 50.6 77.1 37.0
3 39.3 62.8 31.7 46.2 75.4 38.0
4 39.6 62.1 31.2 46.5 74.5 37.4
5 38.5 63.8 31.5 48.9 76.6 37.5
tot. avg. 41.2 48.9
Finally, a simple test of the robustness of the
method against parameter variation was done with a
new run of all samples, randomly choosing cart speed
and load/unload time uniformly picked in 1, 2 ± 0, 1
m/s and 15±2 s. With both Policy 1 and 2, this exper-
iment returned a total completion time substantially
close to the values found with constant parameters.
5 CONCLUSIONS
We tackled a challenging vehicle routing problem
arising in the wafer fab of LFoundry, Italy. The prob-
lem has the form of dial-a-ride on a rectilinear topol-
ogy. We developed a math-heuristic that decomposes
the problem into a routing and a scheduling part.
Routes are obtained by solving an integer linear pro-
gram, then are assigned to vehicles by solving a bot-
tleneck matching problem; carts schedules are found
by a simple heuristic method.
The output of the method developed was used in
a large scale numerical test, from which we got clear
indications of possible improvement of plant opera-
tion. The improvement becomes more sensible if a
more accurate estimate of scheduling time is used in
the routing: this entails a trade-off between CPU time
and solution quality although, in general, the method
is very efficient in computational terms and compliant
with on-line operation. To address the rare cases of
non-compliancy, one should accelerate the resolution
of program (1)-(3), which largely dominates the to-
tal solution time. Future research could then consider
to exploit and strengthen, if possible, the highlighted
m-centre structure of the model.
Further improvements of solution quality could be
obtained by refining individual cart scheduling, also
considering different policies. Prior to algorithm im-
plementation in the plant, additional effort should fi-
nally be devoted to construct a simulation model of
the manufacturing sub-system to observe the effect
of an optimized transportation sub-system on the pro-
cess of request generation.
ACKNOWLEDGEMENT
The authors gratefully acknowledge the supportive
cooperation of the team at LFoundry: Mariagrazia
Colotti, Sergio D’Alberto, Fabio Di Vito, Vincenzo
Greco, Massimo Ianni and Raffaele Porzio.
REFERENCES
Burkard, R. and Derigs, U. (1980). The bottleneck match-
ing problem. In Assignment and Matching Problems:
Solution Methods with FORTRAN-Programs, Lecture
Notes in Economics and Mathematical Systems, 184:
60–71. Springer, Berlin-Heidelberg.
Calik, H., Labb
´
e, M., and Yaman, H. (2015). p-Center
Problems. In: Laporte G., Nickel S., Saldanha da
Gama F. (eds) Location Science, Springer, Cham.
https://doi.org/10.1007/978-3-319-13111-5 4
Garfinkel, R. (1971). An improved algorithm for the bot-
tleneck assignment problem. Operations Research,
19(7): 1747–1751.
Guan, D.J. (1998). Routing a vehicle of capacity greater
than one. Discrete Applied Mathematics, 81: 41–57
Ho, S., Szeto, W., Huo, Y., Leung, J., Petering, M., and Tou,
T. (2018). A survey of dial-a-ride problems: Litera-
ture review and recent developments. Transportation
Research B, 111: 395–421.
Pundir, P., Porwal, S., and Singh, B. (2015). A new algo-
rithm for solving linear bottleneck assignment prob-
lem. Journal of Institute of Science and Technology,
20(2): 101–102.
Wang, F., Lim, A., and Xu, Z. (2006). The one-commodity
pickup and delivery travelling salesman problem on a
path or a tree. Networks, 48(1): 24–35
ICORES 2021 - 10th International Conference on Operations Research and Enterprise Systems
286