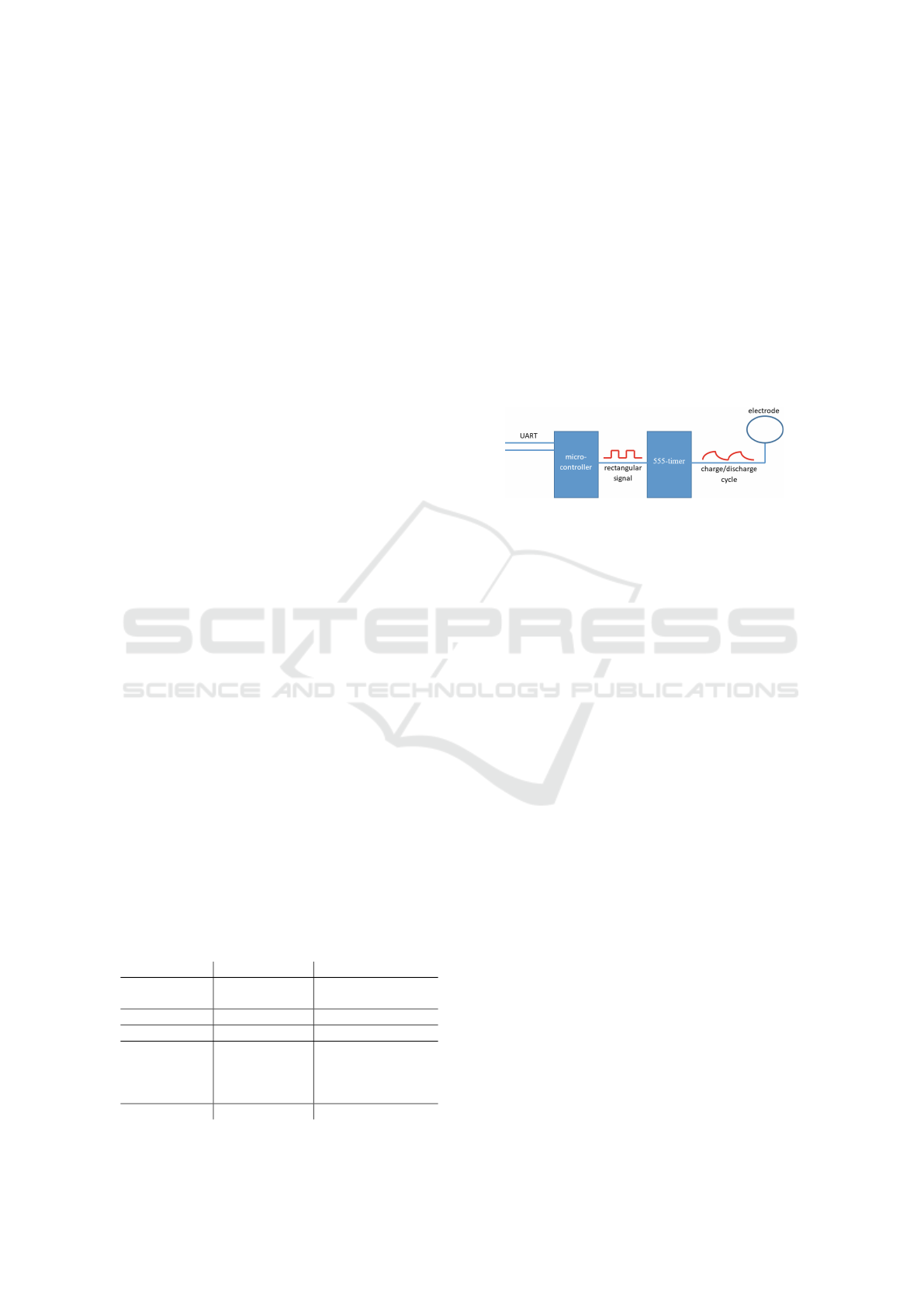
Linoc from being a prototyping toolkit only for be-
ginners, we included design goal 4.
Another important aspect learned while using
other toolkits was, that no matter how many sensors
can be attached to a board, there is always a use case
where you need more. While some toolkits like Open-
CapSense have a CAN-bus interface to combine mul-
tiple boards, it is still a task that takes up several hours
to connect and reprogram them. That is why we added
design goal 5. In this way, the user is able to acquire
higher dimensional data by adding more sensors.
After explaining why we choose these design
goals, we will now focus on how we implemented
them in hardware and software.
4 HARDWARE
4.1 Microcontroller
The microcontroller used on the Linoc board has to
fulfil several requirements; The choice of the micron-
controller is a critical step because most of these re-
quirements have to be covered by the controller itself.
To be precise, the controller affects the design goals 1,
3 and 4. The ESP32 from Espressif fulfills all of these
requirements. It features Wi-Fi, Bluetooth and Eth-
ernet connectivity as high level protocols. For intra-
board communication, the user can choose between
several low level protocols such as UART, I
2
C, Inter-
IC Sound (I
2
C), CAN bus and SPI to name only the
most common ones. This makes the ESP32 a good
processor for our needs of high connectivity. The
ESP32 has enough memory to support a Real-Time
Operating System (RTOS). This allows for complex
use cases as we planed in goal 4.
Since the ESP32 is the direct successor of the
ESP8266, which was (and still is) very popular in the
maker-scene and for Internet of Things (IoT) prod-
ucts, there are a couple of toolchains for different pro-
gramming languages available.
Table 1: Programming languages and toolchains available
for the ESP32.
Toolchain Language Editor
ESP-IDF
C/C++
with FreeRTOS
Eclipse IDE
Mongoose OS C & JavaScript Browser page
MicroPython Python -
PlatformIO C/C++
Atom editor,
Eclipse IDE,
Visual Studio Code,
...
Arduino C++ Arduino IDE
Table 1 lists a selection of possible languages and
editors for the ESP32. Note that this not only is in
favor of our design goal 3, but also goal 2. This is
because the ESP32 is, amongst others, also Arduino
compatible. Arduino is a commonly used language by
beginners when it comes to embedded programming.
4.2 Capacitive Measurements
The Linoc prototyping toolkit features two capacitive
loading mode sensors. The sensors were added di-
rectly onto the board, so that in contrast to other pro-
totyping toolkits, there is no need to add more exter-
nal hardware.
Figure 4: Model of the capacitive sensor.
The capacitive group’s main component is the 555
timer which generates the charging cycles on the elec-
trode, as shown in Figure 4, with a constant charg-
ing current. Since the current is constant, the charg-
ing process is influenced by the environment. When
a conductive objects approaches the electrode, the
resulting capacity between electrode and object in-
creases. Hence, the time needed to charge this ca-
pacitor with the same amount of current increases.
A pulse counter module in the microcontroller then
counts the number of cycles per second, which is the
final measurement parameter. The microcontroller is
also able to dis- and re-enables the 555 timers so that
it is possible to prevent cross talk when multiple sen-
sors are active at the same time.
Linoc also features a shield for both capacitive
sensors to support coaxial cable or to minimize en-
vironmental influences on selected parts of the elec-
trode. The shield is realized by a simple voltage fol-
lower, implemented with an opamp, of the capacitive
feed line.
4.3 Electric Potential Sensing
Besides the two capacitive sensors, Linoc features
two electric potential sensors. Electric potential sens-
ing is another form of capacitive sensing. The main
differences between a capacitive loading mode sen-
sor and an electric potential sensor are the detection
range, the mode of operation and the energy con-
sumption. Electric potential sensing can detect mov-
ing conductive objects in a distance of up to two me-
ters(von Wilmsdorff et al., 2018), while the range of
SENSORNETS 2021 - 10th International Conference on Sensor Networks
52