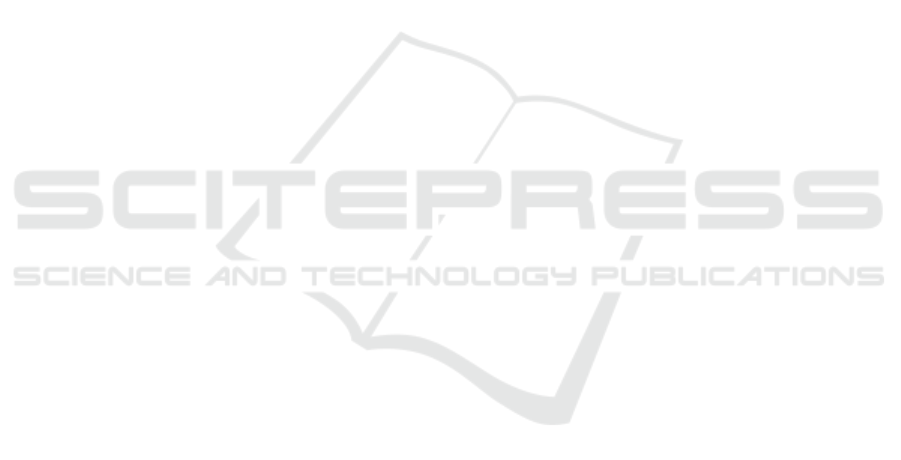
rithm by 29% after 16 hours and by 7% after three
days. The study also showed that SODA can solve
the optimization problem over a complex network of
production processes and SODA is able to scale well
for such a network. However, the efficiency of SODA
is limited by the total budget allocated to OCBA-CO,
which is an input parameter to the algorithm.
Future research directions include: (a) dynami-
cally executing the inflate deflate phase and candidate
refinement phase of SODA to improve the exploration
of the search space; and (b) comparing SODA with an
existing Stochastic Optimization Algorithm Based on
Deterministic Approximations.
ACKNOWLEDGEMENTS
The authors are partly supported by the National Insti-
tute of Standards and Technology Cooperative Agree-
ment 70NANB12H277.
REFERENCES
Amaran, S., Sahinidis, N. V., Sharda, B., and Bury, S. J.
(2016). Simulation optimization: a review of algo-
rithms and applications. Annals of Operations Re-
search, 240(1):351–380.
Chen, C. H. and Lee, L. H. (2011). Stochastic Simulation
Optimization: An Optimal Computing Budget Alloca-
tion. World Scientific Publishing Company, Hacken-
sack, NJ, USA.
Chen, C.-H., Lin, J., Y
¨
ucesan, E., and Chick, S. E. (2000).
Simulation budget allocation for further enhancing the
efficiency of ordinal optimization. Discrete Event Dy-
namic Systems, 10(3):251–270.
Dabney, J. B. and Harman, T. L. (2001). Mastering
SIMULINK 4. Prentice Hall, Upper Saddle River, NJ,
USA, 1st edition.
Deb, K., Pratap, A., Agarwal, S., and Meyarivan, T. (2002).
A fast and elitist multiobjective genetic algorithm:
NSGA-II. IEEE Transactions on Evolutionary Com-
putation, 6(2):182–197.
Durillo, J. J. and Nebro, A. J. (2011). jMetal: A Java frame-
work for multi-objective optimization. Advances in
Engineering Software, 42(10):760 – 771.
Klemmt, A., Horn, S., Weigert, G., and Wolter, K.-J.
(2009). Simulation-based optimization vs. mathemat-
ical programming: A hybrid approach for optimiz-
ing scheduling problems. Robotics and Computer-
Integrated Manufacturing, 25(6):917–925.
Krishnamoorthy, M., Brodsky, A., and Menasc, D. A.
(2018). Stochastic decision optimisation based on de-
terministic approximations of processes described as
closed-form arithmetic simulation. Journal of Deci-
sion Systems, 27(sup1):227–235.
Krishnamoorthy, M., Brodsky, A., and Menasc
´
e, D. (2015).
Optimizing stochastic temporal manufacturing pro-
cesses with inventories: An efficient heuristic algo-
rithm based on deterministic approximations. In Pro-
ceedings of the 14th INFORMS Computing Society
Conference, pages 30–46.
Krishnamoorthy, M., Brodsky, A., and Menasc
´
e, D. A.
(2017). Stochastic optimization for steady state pro-
duction processes based on deterministic approxima-
tions. Technical Report GMU-CS-TR-2017-3, 4400
University Drive MSN 4A5, Fairfax, VA 22030-4444
USA.
Krishnamoorthy, M., Brodsky, A., and Menasc
´
e, D. A.
(2020). Source code for SODA algorithm.
Lee, L. H., Pujowidianto, N. A., Li, L. W., Chen, C. H., and
Yap, C. M. (2012). Approximate simulation budget
allocation for selecting the best design in the presence
of stochastic constraints. IEEE Transactions on Auto-
matic Control, 57(11):2940–2945.
Nebro, A., Durillo, J., Garc
´
ıa-Nieto, J., Coello Coello,
C., Luna, F., and Alba, E. (2009). Smpso: A new
pso-based metaheuristic for multi-objective optimiza-
tion. In 2009 IEEE Symposium on Computational In-
telligence in Multicriteria Decision-Making (MCDM
2009), pages 66–73. IEEE Press.
OpenModelica (2009). Efficient Traceable Model-
Based Dynamic Optimization - EDOp, https://
openmodelica.org/research/omoptim/edop. Open-
Modelica.
Paraskevopoulos, D., Karakitsos, E., and Rustem, B.
(1991). Robust Capacity Planning under Uncertainty.
Management Science, 37(7):787–800.
Provan, G. and Venturini, A. (2012). Stochastic simula-
tion and inference using modelica. In Proceedings
of the 9th International Modelica Conference, pages
829–837.
Thieriota, H., Nemera, M., Torabzadeh-Tarib, M., Fritzson,
P., Singh, R., and Kocherry, J. J. (2011). Towards
design optimization with openmodelica emphasizing
parameter optimization with genetic algorithms. In
Modellica Conference. Modelica Association.
Thompson, S. D. and Davis, W. J. (1990). An integrated ap-
proach for modeling uncertainty in aggregate produc-
tion planning. IEEE Transactions on Systems, Man,
and Cybernetics, 20(5):1000–1012.
Xu, J., Zhang, S., Huang, E., Chen, C., Lee, L. H., and
Celik, N. (2016). MO
2
TOS: Multi-fidelity optimiza-
tion with ordinal transformation and optimal sam-
pling. Asia-Pacific Journal of Operational Research,
33(03):1650017.
Zitzler, E. and K
¨
unzli, S. (2004). Indicator-based selection
in multiobjective search. In Proceedings of the 8th
International Conference on Parallel Problem Solving
from Nature, 2004, pages 832–842. Springer.
Zitzler, E., Laumanns, M., and Thiele, L. (2001). SPEA2:
Improving the strength pareto evolutionary algorithm.
Technical Report 103, Computer Engineering and
Networks Laboratory (TIK), Swiss Federal Institute
of Technology (ETH), Zurich, Switzerland.
ICORES 2021 - 10th International Conference on Operations Research and Enterprise Systems
294