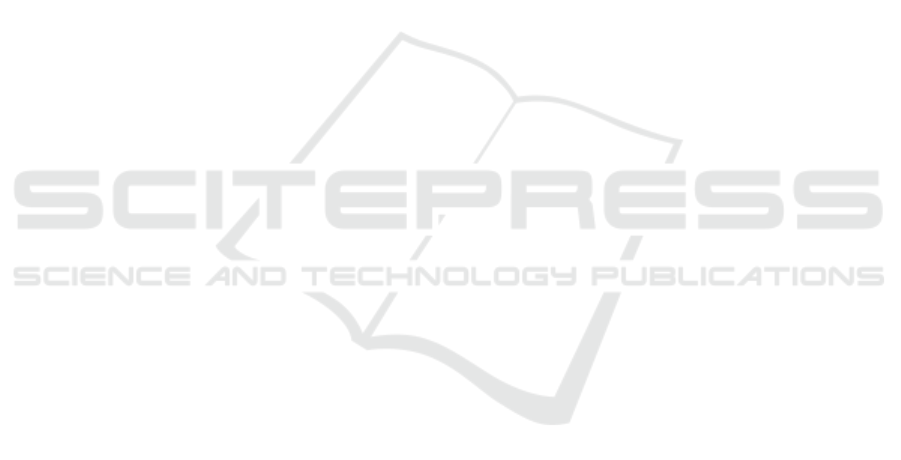
design and it can also be easily implemented on board
thanks to its simplicity and robustness.
Further developments may consist in the
realization of a more complex motorcycle model,
considering it as a multi-body system of four bodies:
the front and rear wheels, the rear assembly
(including frame, engine and fuel tank), the front
assembly (including steering column, handle-bar, and
front fork). Moreover, a suspension system at the
front and at the rear could also be considered; in this
way, it could be analyzed the degrees of freedom of
the motorcycle in the longitudinal plane such as the
pitch motion and the vertical displacement.
The model developed could also be completed
with a rider leaning model for the roll stabilization. In
particular, it could be implemented a rider control in
which the rider tries to stabilize the motorcycle by
inclining left and right his upper body in such a way
to not consider the roll angle fixed to its steady-state
value, in order to have a better description of
transverse dynamics.
REFERENCES
Bruni, S., Meijaard, J. P., Rill, G., Schwab, A. L., 2020.
State-of-the-art and challenges of railway and road
vehicle dynamics with multibody dynamics
approaches. Multibody System Dynamics, 49(1).
Cossalter, V., 2014. Motorcycle dynamics. Lulu.com.
Cossalter, V., Lot, R., 2002. A motorcycle multi-body
model for real time simulations based on the natural
coordinates approach. Vehicle System Dynamics, 37(6),
423–447.
Dugoff, H., Fancher, P. S., Segel, L., 1969. Tire
Performance Characteristics Affecting Vehicle
Response to Steering and Braking Control Inputs.
Escalona, J. L., Kłodowski, A., Muñoz, S., 2018. Validation
of multibody modeling and simulation using an
instrumented bicycle: from the computer to the road.
Multibody System Dynamics, 43(4), 297–319.
Escalona, J. L., Recuero, A. M., 2012. A bicycle model for
education in multibody dynamics and real-time
interactive simulation. Multibody System Dynamics,
27(3), 383–402.
Farroni, F., Russo, M., Sakhnevych, A., Timpone, F., 2019.
TRT EVO: Advances in real-time thermodynamic tire
modeling for vehicle dynamics simulations.
Proceedings of the Institution of Mechanical Engineers,
Part D: Journal of Automobile Engineering, 233(1),
121–135.
Farroni, F., Sakhnevych, A., Timpone, F., 2019. A three-
dimensional multibody tire model for research comfort
and handling analysis as a structural framework for a
multi-physical integrated system. Proceedings of the
Institution of Mechanical Engineers, Part D: Journal of
Automobile Engineering, 233(1), 136–146.
Genovese, A., Carputo, F., Maiorano, A., Timpone, F.,
Farroni, F., Sakhnevych, A., 2020. Study on the
Generalized Formulations with the Aim to Reproduce
the Viscoelastic Dynamic Behavior of Polymers.
Applied Sciences, 10(7), 2321.
Genovese, A., Farroni, F., Papangelo, A., Ciavarella, M.,
2019. A Discussion on Present Theories of Rubber
Friction, with Particular Reference to Different Possible
Choices of Arbitrary Roughness Cutoff Parameters.
Lubricants, 7(10), 85.
Genta, G., 1997. Motor Vehicle Dynamics. World Scientific
Publishing Co. Pte. Ltd.
Gillespie, T. D., 1996. Fundamentals of Vehicle Dynamics
- Thomas D.Gillespie (pp. 1–294).
Herlihy, D. V., 2004. Bicycle : the history. Yale University
Press.
Koenen, C., 1983. The dynamic behaviour of a motorcycle
when running straight ahead and when cornering.
Kooijman, J. D. G., Schwab, A. L., 2011. A review on
handling aspects in bicycle and motorcycle control.
Proceedings of the ASME Design Engineering
Technical Conference, 4(PARTS A AND B), 597–607.
Leonelli, L., Mancinelli, N., 2015. A multibody motorcycle
model with rigid-ring tyres: Formulation and
validation. Vehicle System Dynamics, 53(6), 775–797.
Limebeer, D. J. N., Sharp, R. S., Evangelou, S., 2002.
Motorcycle steering oscillations due to road profiling.
Journal of Applied Mechanics, Transactions ASME,
69(6), 724–739.
Lowell, J., McKell, H. D., 1982. The stability of bicycles.
American Journal of Physics, 50(12), 1106–1112.
Pacejka, H. B., & Sharp, R. S., 1991. Shear Force
Development by Pneumatic Tyres in Steady State
Conditions: A Review of Modelling Aspects. Vehicle
System Dynamics, 20(3–4), 121–175.
Pacejka, H. B., 2006. Tire and Vehicle Dynamics.
Rajput, B., Bayliss, M., Transactions, D. C.-S., 2007. A
simplified motorcycle model. JSTOR.
Romano, L., Sakhnevych, A., Strano, S., Timpone, F.,
2019. A hybrid tyre model for in-plane dynamics.
Vehicle System Dynamics, 1–23.
Sakai, H., 1990. Study on Cornering Properties of Tire and
Vehicle. Tire Science and Technology, 18(3), 136–169.
Schwab, A. L., Meijaard, J. P., Papadopoulos, J. M., 2004.
Benchmark Results on the Linearized Equations of
Motion of an Uncontrolled Bicycle.
Seffen, K. A., Parks, G. T., Clarkson, P. J., 2001.
Observations on the controllability of motion of two-
wheelers. Proceedings of the Institution of Mechanical
Engineers, Part I: Journal of Systems and Control
Engineering, 215(2), 143–156.
Sharp, R. S., 1971. The Stability and Control of
Motorcycles. Journal of Mechanical Engineering
Science, 13(5), 316–329.
Sharp, R. S., Alstead, C. J., 1980. The Influence of
Structural Flexibilities on the Straight-running Stability
of Motorcycles. Vehicle System Dynamics, 9(6), 327–
357.
Non-linear Motorcycle Dynamic Model for Stability and Handling Analysis with Roll Motion and Longitudinal Speed Regulation
299