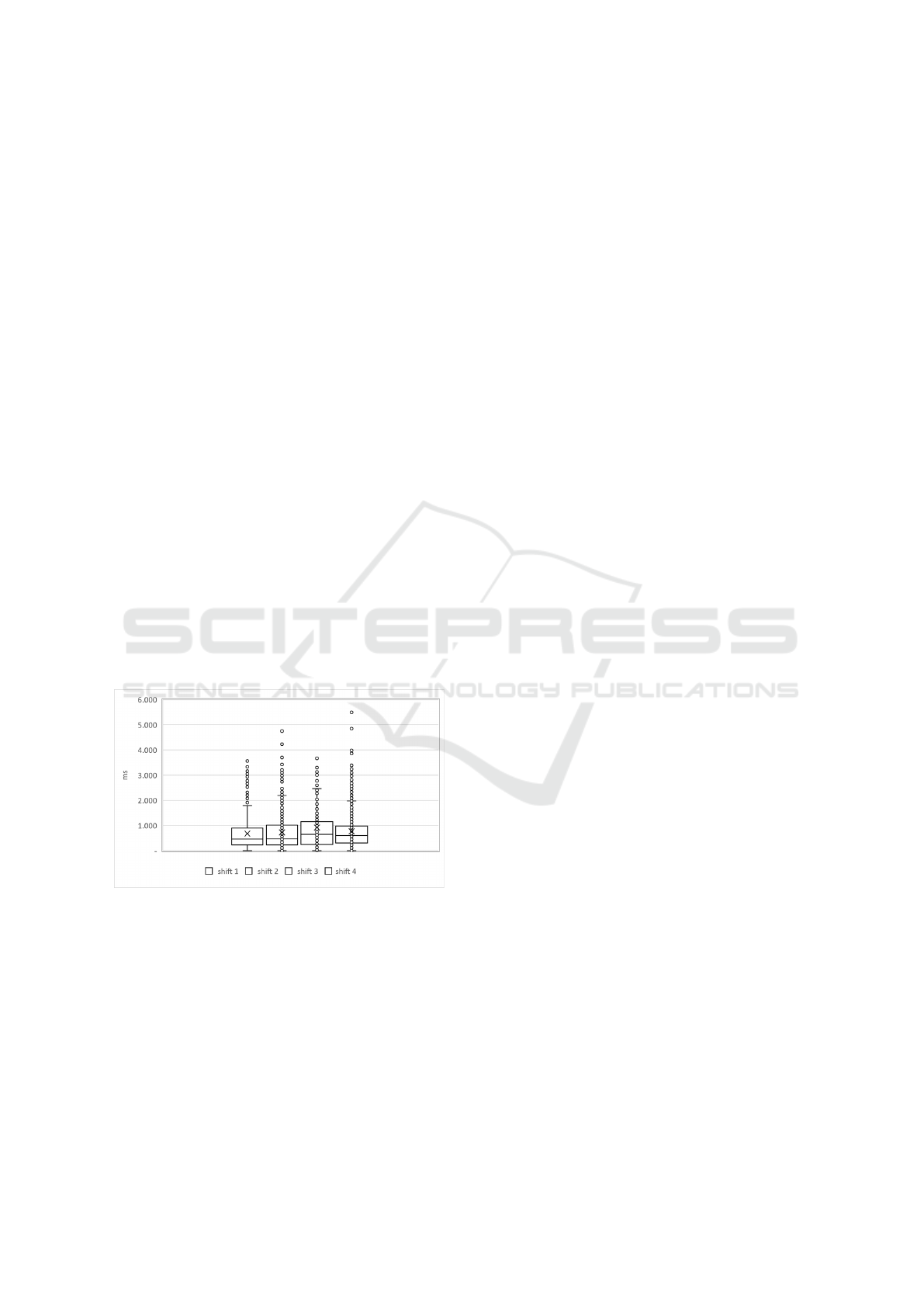
it is not possible to change it. Tabu search might find
this improvement and make the change, but it might
take time to find it.
Regarding rescheduling, MAS-TD, Tabu Search,
and Disp-ALG can update schedules when major
events occur at the mine. However, the produc-
tion results and the needed computation time that the
methods take to generate the schedules differs among
them. Disp-ALG is the fastest method to update the
schedules; however, its schedules are the worst in
terms of production rates compared to the generated
schedules by MAS-TD and Tabu Search.
In the simulation, MAS-TD applied a reschedul-
ing strategy for the complete schedule because it aims
at the maximum production level. This strategy takes
much more time than the time required by Disp-ALG
(as is shown in Table 5), because it generates all the
schedules from scratch. However, some assignments
can be made within a short time frame, due to two
reasons: first, the algorithms that generate the sched-
ules in MAS-TD are anytime algorithms, i.e., they can
be stopped at any time, and still will generate a fea-
sible schedule solution. Second, the negotiation pro-
cess is fast and many assignments can be computed
within a few seconds. This allows the fleet to con-
tinue working based on a preliminary generated as-
signment, while MAS-TD continues to generate the
schedules. Figure 13 shows that most of the success-
ful negotiations, i.e., assignments computed, are done
in less than one second in all scenarios.
Figure 13: Box and whiskers diagram shows that the mean
of the duration of the successful negotiations is around 0.5
seconds.
7 CONCLUSIONS
A major process in open-pit mines is material han-
dling. In this process, dispatching a truck becomes a
complex decision because of the stochasticity of the
process and the dynamics of the environment. In gen-
eral, a centralized system supports this process. As
an alternative to currently used systems, we present
a multiagent system (MAS-TD) with agents that rep-
resent real world equipment items. In addition, the
agents can react to the dynamics of the mine envi-
ronment and generate new schedules when equipment
items encounter failures.
To evaluate the proposed MAS, we compare it
against a Tabu Search procedure. Our results demon-
strate that the MAS-TD is a more appropriate method
than the Tabu Search procedure to solve the truck
dispatching problem in open-pit mines, because the
MAS-TD generates more efficient schedules than the
Tabu Search procedure. In addition, when critical
events occur in the mine environment, the MAS-TD
regenerates its schedules and achieves a higher pro-
duction than the schedules generated by Tabu Search
and regenerated by Disp-ALG.
In our further research, we will consider more sce-
narios that include other events such as shovel and
truck delays. To decrease the time needed by MAS-
TD for rescheduling, we will evaluate a partial regen-
eration of the schedules.
REFERENCES
Adams, K. K. and Bansah, K. K. (2016). Review of Op-
erational Delays in Shovel-Truck System of Surface
Mining Operations. In 4th UMaT Biennial Interna-
tional Mining and Mineral Conference, pages 60–65,
Tarkwa, Ghana.
Alarie, S. and Gamache, M. (2002). Overview of Solu-
tion Strategies Used in Truck Dispatching Systems
for Open Pit Mines. International Journal of Surface
Mining, Reclamation and Environment, 16(1):59–76.
Bakhtavar, E. and Mahmoudi, H. (2020). Development of
a scenario-based robust model for the optimal truck-
shovel allocation in open-pit mining. Computers and
Operations Research, 115(March 2020):104539.
Bellifemine, F., Caire, G., and Greenwood, D. (2007). De-
veloping Multi-Agent Systems with JADE. John Wiley
& Sons, Chichester, UK.
Chang, Y., Ren, H., and Wang, S. (2015). Modelling and
optimizing an open-pit truck scheduling problem. Dis-
crete Dynamics in Nature and Society, 2015:745378.
Costa, F. P. D., Souza, M. J. F., and Pinto, L. R. (2005). Um
modelo de programac¸
˜
ao matem
´
atica para alocac¸
˜
ao
est
´
atica de caminh
˜
oes visando ao atendimento de
metas de produc¸
˜
ao e qualidade. Rem: Revista Escola
de Minas, 58(1):77–81.
Glover, F. (1989). Tabu Search - Part I. Orsa Journal on
Computing, 1(3):190–206.
Icarte, G. and Herzog, O. (2019). A multi-agent system for
truck dispatching in an open-pit mine. In Lottermoser,
B., editor, Abstracts of the Second International Con-
ference Mines of the Future 13 & 14 June 2019,
Institute of Mineral Resources Engineering, RWTH
Aachen University, Aachen, Germany. Verlag Mainz.
Application of Multiagent System and Tabu Search for Truck Dispatching in Open-pit Mines
169