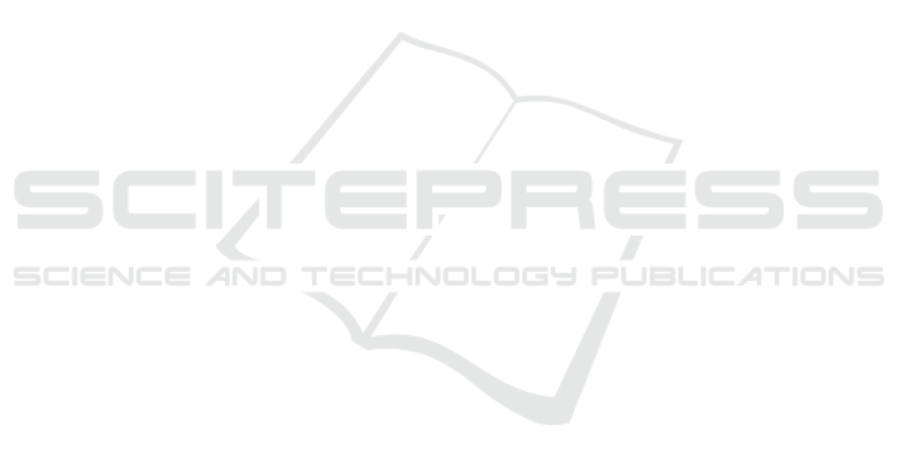
which enables the classifier to distinguish between
faulty and non-faulty condition,and also between dif-
ferent types of faults(Dai and Gao, 2013). In signal
based methods the relationship between the features
and the system current state, is extracted from the data
set without any human interference. It requires the
identification of signal patterns without having prede-
fined examples(Karlsson, 2019).
On the other hand, the core idea of Knowledge
based methods is to create a connection from fea-
ture to system condition autonomously, Which means
that the classifier will be trained by examining a huge
amount of examples and it learns the pattern neces-
sary for fault classification on its own. Therefore, this
method requires much more training data compared
to those required in signal based and model based
techniques.Knowledge based method also have dif-
ferent types based on the fault detection and diagnosis
(FDD) method utilized in them.
Hybrid technique is mainly a combination of two
of the above techniques or even all of them which is
the most common Fault Detection Technique (Cecati,
2015)(Gao et al., 2015) and hereinafter, some of the
previous research work of this topic will be cited. In
the process of developing a data-driven health moni-
toring system, two major tasks have to be solved for
improving prediction accuracy and computation ef-
ficiency: proper feature extraction from large-scale
sensory data and an accurate data analysis model. The
goal of a good health monitoring of a suspension sys-
tem is high prediction accuracy and low computation
time.
Luo et al.(Luo et al., 2018) proposed a novel
method is proposed to develop a health monitoring
system by integrating a multi- Gaussian fitting fea-
ture extraction method with a long short-term mem-
ory (LSTM) Convolutional Neural Network (CNN)
based damage identification method. Firstly, a multi-
Gaussian fitting method is devised to obtain compre-
hensive frequency-domain information of each sub-
sequence of the available vibration signals in order to
represent data of vibration signals and reduce the in-
put data size for data analysis purposes. Then this
data is feed to CNN model in order to obtain a non-
linear relation between the frequency domain features
and real time partial damage level.
In addition, Luo et al(Luo et al., 2019) intro-
duced another method of health monitor by using
Dual-Tree Complex Wavelet enhanced (DTCWT),
to obtain multi scale characteristics information of
measured signals. A deep convolutional neural net-
works (DCNN) model is then employed to automat-
ically extract useful damage features.The proposed
method proved efficient in eliminating noise from the
measured vibration signals.Finally a Contextual long
short-term memory (CLSTM) is built to capture the
nonlinear relationship between the preprocessed vi-
bration signals and corresponding partial damage val-
ues. Chen et al.(Chen et al., 2019) introduced an-
other approach to achieve the same goal by using Ex-
treme Learning Machine (ELM) along side with con-
volutional neural networks. Time series vibration sig-
nals were measured using accelerometers, while good
representative features were obtained using Wavelet
Transform (WT) to convert the one-dimensional time
signals into two-dimensional time-frequency images.
In CNN-ELM, the training samples are firstly fed into
the CNN architecture to obtain the feature maps, then
all the features are combined together and regarded as
the input of the ELM model which can be efficiently
trained by a generalized inverse operation. At the test-
ing phase, the testing samples are fed into the trained
CNN-ELM model to obtain the final diagnosis result.
Hong et al.(Hong et al., 2019) presented Multi-
Output Support vector regression (MSVR) method for
health monitoring of trains suspension system. The
main idea was to monitor the stiffness and damp-
ing coefficients the suspension system using vibration
signals measured on trains in real time. First, a simple
suspension system dynamics model is built to gener-
ate a training data set. Furthermore, key features are
extracted from frequency response curves to reflect
the impact of spring and damper degradation. Sub-
sequently, a supervised learning model based on the
(MSVR) is built to predict the stiffness and damping
coefficients of suspension systems from features ex-
tracted in the second module Once the model is built,
real time monitoring can be achieved.
KARLSSON (Karlsson, 2019) developed a
model, based on frequency response functions,to sim-
ulate the response of the four corner suspensions and
the goal was to detect which suspension is the faulty
one without quantifying the degradation value itself.
Hong et al. (Hong et al., 2019) provided different
approach based on the bode plot of the vertical ac-
celeration alongside with multi-output support vector
regression. The current paper presents an extension
to the above mentioned work, by introducing accel-
eration frequency response analysis along side with a
classification technique, in order to identify and quan-
tify the degradation percentage of the faulty suspen-
sion. A Knowledge-based condition monitoring, of
automotive suspension dampers, is developed by im-
plementing a quarter car model (QCM). The sprung
mass acceleration - frequency power spectral density
curves, for different cases of performance degrada-
tion in suspension damping and different operational
conditions, is provided in response to the random
VEHITS 2021 - 7th International Conference on Vehicle Technology and Intelligent Transport Systems
326