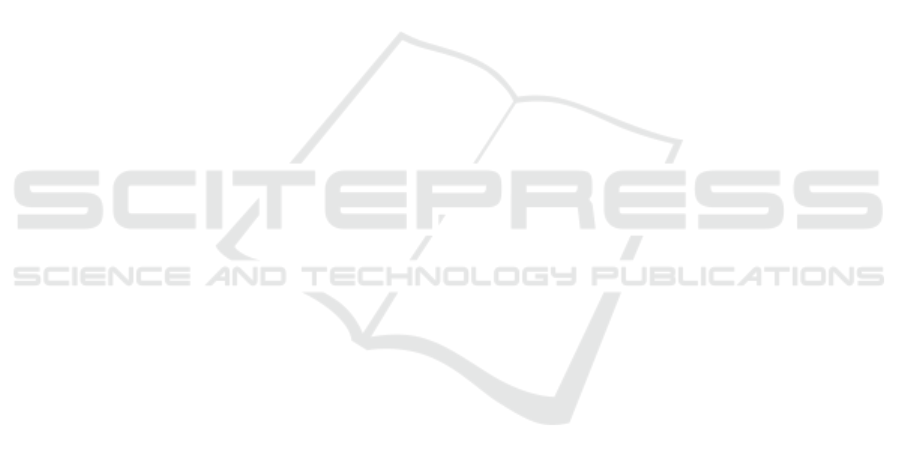
scribed in (Ladusaw, 1966). The air filter condition
is indicated by a device which floats in the air that
bypasses an air filter. The floating height is also in-
fluenced by the fan speed. So, there is an indication
area for the low and the high fan speed. In (Fraden
and Rutstein, 2007) a method is described which uses
a heated wire to measure the volume flow. If the lat-
ter drops below a predefined limit, the air filter is de-
clared to be clogged. A similar method is claimed in
(Kang et al., 2006). Herein, the temperature gradi-
ent due to a fan speed change is measured. The air
filter condition is determined by comparing the tem-
perature gradient with a predefined limit. All these
approaches have in common that they detect air filter
clogging, but they are not able to predict the remain-
ing useful life of air filters. In addition to that these
methods must be tuned for different types of air fil-
ters.
An air filter model which utilizes measurements
that are already collected in HVAC system provides
a better scalability of the desired solution. In (Kang
et al., 2007) it is claimed that deviations of the to-
tal pressure difference of fans are mainly induced by
air filters. Therefore, the condition of an air filter is
assessed by comparing the measured total pressure
difference with the one which is estimated from the
characteristic fan curve. The total pressure difference
is truly affected by the condition of air filters, but this
is not the only influence. Therefore, this approach is a
good measure for anomalies in HVAC systems. This
method is designed for a particular system and does
not generalize well. Therefore, it is necessary to use a
model of air filters which represents the resistance of
air filters to the air flow.
In (Saarela et al., 2014) a model which combines
different influences on the differential pressure devel-
opment of air filters for nuclear power plants is intro-
duced. Each influence is modelled separately. Hereby
the relationship between volume flow
˙
V and differen-
tial pressure ∆p of an air filter is described by a model
of the form which is shown in Equation 1. This equa-
tion also includes the parameters a and n. Hereinafter
this model is called type I.
∆p = a ·
˙
V
n
(1)
In (Liu et al., 2003) such a model is also used to
estimate the reduction of empty spaces between fibres
of air filters. The same model structure is also de-
scribed in (DIN Deutsches Institut f
¨
ur Normung e.V.,
2013). Whereas, (Eckhardt, 2018) uses the following
approach to model the relationship between volume
flow and differential pressure of an air filter which is
subsequently denoted as type II.
∆p = a ·
˙
V
2
(2)
This modelling approach is also used in (Kruger,
2013) and in (Verein Deutscher Ingenieure, 2004).
The latter cites (L
¨
offler, 1988) which extends the sec-
ond order term with a linear term and the associated
parameter b. This yields Equation 3. The correspond-
ing model is consecutively called type III and is also
proposed in (Kanaoka and Hiragi, 1990), (Rivers and
Murphy, 2000) and (Albers, 2017).
∆p = a ·
˙
V
2
+ b ·
˙
V (3)
As shown, in the literature there is no standard
model for air filters. In addition, there is no com-
parison with other models in any of the publications.
Furthermore, there is no agreement in the literature on
the consideration of further influences on the differen-
tial pressure, such as air density or dynamic viscosity
of air as well as filter-specific parameters such as fi-
bre thickness. While the models in (Verein Deutscher
Ingenieure, 2004), (L
¨
offler, 1988), (Kanaoka and Hi-
ragi, 1990) and (Rivers and Murphy, 2000) cover
any of these influences in detail, the model in (DIN
Deutsches Institut f
¨
ur Normung e.V., 2013) takes only
the influences of air density and dynamic viscosity of
air into account. On the other hand the models in
(Saarela et al., 2014), (Liu et al., 2003), (Eckhardt,
2018), (Kruger, 2013) and (Albers, 2017) neglect all
influences. Therefore, for a comparison of these mod-
els, it is necessary to unify the level of detail of the
models and to adapt all models in such a way that it
is possible to quantify the benefit of further measured
variables and derived influences, such as air density
and dynamic viscosity of air.
3 FILTER MODELS
During the model unification, it must be ensured that
the resulting models can be retrofitted in existing
HVAC systems with as little effort as possible. In
existing HVAC systems, the filter-specific parameters
are usually unknown. Therefore, the level of detail
of the models is reduced to such an extent that they
do not contain any filter-specific parameters. Further-
more, it must be ensured that all used models can
represent the influences of air density and dynamic
viscosity of air. The following chapters describe the
model unification procedure and the resulting models.
3.1 Exponential Model
In (DIN Deutsches Institut f
¨
ur Normung e.V., 2013)
a model is described which takes dynamic viscosity
of air and air density into account and has the same
Condition Monitoring for Air Filters in HVAC Systems with Variable Volume Flow
103