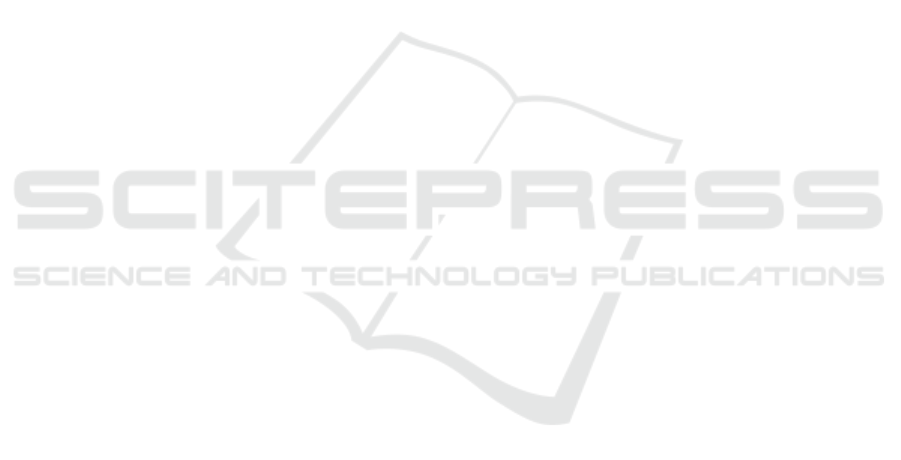
force to which the platooned vehicles are subjected
and therefore the vehicle needs less energy to
overcome that force. The slope for the reduction in
travel time, delay, and fuel consumption are
approximately -3.5%, -6.9%, and -9% respectively.
The respective coefficients of determination
are
0.23, 0.28, and 0.87 which further stresses the steep
reduction in fuel consumption due to platooning.
4 CONCLUSIONS
In this paper, an input minimal platooning controller
is presented. This logic takes into account various
dynamic and kinematic constraints that vehicles
experience. These include acceleration, velocity, and
collision avoidance constraints. This controller was
later applied on the highways in downtown Los
Angeles in the INTEGRATION software. The results
suggest a clear trend towards a reduction in system-
wide travel time, delay and notably fuel consumption.
The average reduction in travel time for all the MPRs
is up to 5%. The average reduction in delay as well as
fuel consumption (and ultimately CO
2
emissions) are
up to 9% and 8%, respectively. These results are for
the fleet of all vehicles, platooned and non-platooned
traveling through the downtown area. This leads us to
deduce that controlling the trips of a subset of
vehicles inside a large network does have the
potential to benefit other road users in a positive
manner. In the future work, we will be conducting a
detailed investigation on the performance of this
controller on a mixed platoon comprised of
conventional, hybrid and electrical vehicles at various
MPRs.
ACKNOWLEDGMENTS
This effort was funded through the Office of Energy
Efficiency and Renewable Energy (EERE), Vehicle
Technologies Office, Energy Efficient Mobility
Systems Program under award number DE-EE0
008209.
REFERENCES
Ahn, K., & Rakha, H. (2019). A Simple Hybrid Electric
Vehicle Fuel Consumption Model for Transportation
Applications. Retrieved from.
Alam, A. A., Gattami, A., & Johansson, K. H. (2010). An
Experimental Study on the Fuel Reduction Potential of
Heavy Duty Vehicle Platooning. Paper presented at the
13th International IEEE Conf. on Intelligent
Transportation Systems.
Bergenhem, C., Shladover, S., Coelingh, E., Englund, C.,
& Tsugawa, S. (2012, October 22-26). Overview of
platooning systems. Paper presented at the 19th ITS
World Congress, Vienna, Austria.
Bevly, D., Murray, C., Lim, A., Turochy, R., Sesek, R.,
Smith, S., Kahn, B. (2017). Heavy Truck Cooperative
Adaptive Cruise Control: Evaluation, Testing, and
Stakeholder Engagement for Near Term Deployment:
Phase Two Final Report. Retrieved from.
Bichiou, Y., & Rakha, H. A. (2019). Developing an
Optimal Intersection Control System for Automated
Connected Vehicles. IEEE Transactions on Intelligent
Transportation Systems, 20(5), 1908-1916.
Brown, I. D. (2005). Review of the 'looked But Failed to
See' Accident Causation Factor. Retrieved from.
Davila, A., & Nombela, M. (2012). Platooning - Safe and
Eco-Friendly Mobility. SAE International.
doi:10.4271/2012-01-0488.
Deng, Q., & Ma, X. (2014). A Fast Algorithm for Planning
Optimal Platoon Speeds on Highway. Paper presented
at the IFAC Proceedings.
Dion, F., Rakha, H., & Kang, Y.-S. (2004). Comparison of
delay estimates at under-saturated and over-saturated
pre-timed signalized intersections. Transportation
Research Part B-Methodological, 38(2), 99-122.
Du, J., Rakha, H. A., Elbery, A., & Klenk, M. (2018).
Microscopic Simulation and Calibration of a Large-
Scale Metropolitan Network: Issues and Proposed
Solutions. Paper presented at the Transportation
Research Board 97th Annual Meeting, Washington,
DC.
Ellis, M., & Gargoloff, J. I. (2015). Aerodynamic Drag and
Engine Cooling Effects on Class 8 Trucks in Platooning
Configurations. Paper presented at the SAE 2015
Commercial Vehicle Engineering Congress.
Hussein, A. A., & Rakha, H. A. (2020). Vehicle Platooning
Impact on Drag Coefficients and Energy/Fuel Saving
Implications. arXiv:2001.00560.
Lammert, M. P., Duran, A., Diez, J., Burton, K., &
Nicholson, A. (2014). Effect of Platooning on Fuel
Consumption of Class 8 Vehicles Over a Range of
Speeds, Following Distances, and Mass. Paper
presented at the SAE 2014 Commercial Vehicle
Engineering Congress.
Loulizi, A., Bichiou, Y., & Rakha, H. (2019). Steady-State
Car-Following Time Gaps: An Empirical Study Using
Naturalistic Driving Data. Journal of Advanced
Transportation, 2019. doi:10.1155/2019/7659496.
Rakha, H., & Ahn, K. (2004). Integration modeling
framework for estimating mobile source emissions.
Journal of transportation engineering, 130(2), 183-
193.
Rakha, H., Lucic, I., Demarchi, S., Setti, J., & Aerde, M.
(2001). Vehicle Dynamics Model for Predicting
Maximum Truck Acceleration Levels. Journal of
Transportation Engineering, 127(5), 418-425.
doi:10.1061/(ASCE)0733-947X(2001)127:5(418).
VEHITS 2021 - 7th International Conference on Vehicle Technology and Intelligent Transport Systems
384