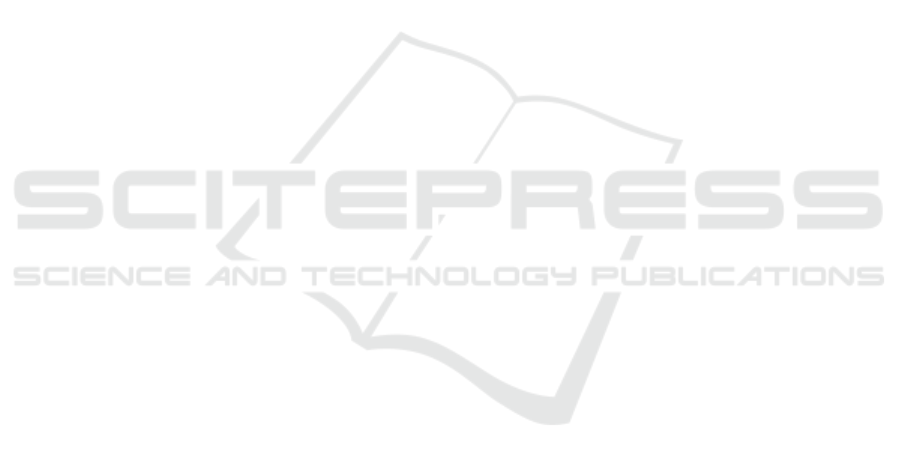
common centralized scheduling solutions is still out-
standing and will be done in the near future. Next, we
want to extend the solution to handle more than the
two task types setup and processing steps, like load-
ing and unloading materials for a job, and evaluate
how the developed solution is performing with these
new constraints.
ACKNOWLEDGEMENTS
The authors acknowledge the financial support by
the German Federal Ministry of Education and Re-
search within the funding program "Forschung an
Fachhochschulen" (contract number: 13FH133PX8).
REFERENCES
Adhau, S. and Mittal, M. L. (2012). A multiagent based
system for resource allocation and scheduling of dis-
tributed projects. International Journal of Modeling
and Optimization, pages 524–528.
Akkiraju, R., Keskinocak, P., Murthy, S., and Wu, F. (2001).
An agent-based approach for scheduling multiple ma-
chines. Applied Intelligence, 14(2):135–144.
Chan, F. T. S., Wong, T. C., and Chan, L. Y. (2006).
Flexible job-shop scheduling problem under resource
constraints. International Journal of Production Re-
search, 44(11):2071–2089.
Dhiflaoui, M., Nouri, H. E., and Driss, O. B. (2018). Dual-
resource constraints in classical and flexible job shop
problems: A state-of-the-art review. Procedia Com-
puter Science, 126:1507–1515.
FIPA TC C (03.12.2002). Fipa contract net interaction pro-
tocol specification.
Frazier, G. V. (1996). An evaluation of group scheduling
heuristics in a flow-line manufacturing cell. Inter-
national Journal of Production Research, 34(4):959–
976.
Gehlhoff, F. and Fay, A. (2020). On agent-based decentral-
ized and integrated scheduling for small-scale manu-
facturing. at - Automatisierungstechnik, 68(1):15–31.
Grabot, B. and Geneste, L. (1994). Dispatching rules in
scheduling: a fuzzy approach. International Journal
of Production Research, 32(4):903–915.
Gu, M., Gu, J., and Lu, X. (2018). An algorithm for multi-
agent scheduling to minimize the makespan on m par-
allel machines. Journal of Scheduling, 21(5):483–492.
Guizzi, G., Revetria, R., Vanacore, G., and Vespoli, S.
(2019). On the open job-shop scheduling problem:
A decentralized multi-agent approach for the manu-
facturing system performance optimization. Procedia
CIRP, 79:192–197.
He, J., Li, Q., and Xu, D. (2016). Scheduling two par-
allel machines with machine-dependent availabilities.
Computers & Operations Research, 72:31–42.
Jeschke, S., Brecher, C., Song, H., and Rawat, D. B., ed-
itors (2017). Industrial Internet of Things. Springer
Series in Wireless Technology. Springer International
Publishing, Cham.
Jodlbauer, H. (2007). Produktionsoptimierung: Wertschaf-
fende sowie kundenorientierte Planung und
Steuerung. Springer Vienna.
Kim, Y.-D. (1990). A comparison of dispatching rules for
job shops with multiple identical jobs and alternative
routeings. International Journal of Production Re-
search, 28(5):953–962.
Lenstra, J. K. and A. H. G. Rinnooy Kan (1978). Complex-
ity of scheduling under precedence constraints. Oper-
ations Research, 26(1):22–35.
Liu, J. and Sycara, K. (1996). Multiagent coordination in
tightly coupled task schedulingmultiagent coordina-
tion in tightly coupled task scheduling. Proceedings
of the Second International Conference on Multiagent
Systems, pages 181–188.
Miao, C. and Zou, J. (2015). Parallel-machine schedul-
ing with time-dependent and machine availability con-
straints. Mathematical Problems in Engineering,
2015:1–6.
Montazeri, M. and van Wassenhove, L. N. (1990). Analy-
sis of scheduling rules for an fms (flexible manufac-
turing system). International Journal of Production
Research, 28(4):785–802.
Mourtzis, D., Doukas, M., and Psarommatis, F. (2012).
Design and planning of decentralised production net-
works under high product variety demand. Procedia
CIRP, 3:293–298.
Munkelt, T. and Krockert, M. (2018). An approach to a self-
organizing production in comparison to a centrally
planned production. In Tagungsband ASIM 2018 – 24.
Symposium Simulationstechnik, pages 299–306. AR-
GESIM.
Nouri, H. E., Driss, O. B., and Ghédira, K. (2016). A clas-
sification schema for the job shop scheduling problem
with transportation resources: State-of-the-art review.
In Silhavy, R., Senkerik, R., Oplatkova, Z. K., Silhavy,
P., and Prokopova, Z., editors, Artificial Intelligence
Perspectives in Intelligent Systems, volume 464 of Ad-
vances in Intelligent Systems and Computing, pages
1–11. Springer International Publishing, Cham.
Rohloff, M. (1993). Decentralized production planning and
design of a production management system based on
an object-oriented architecture. International Journal
of Production Economics, 30-31:365–383.
Sarkar, A. and Šormaz, D. (2019). Ontology model for
process level capabilities of manufacturing resources.
Procedia Manufacturing, 39:1889–1898.
Shen, W., Wang, L., and Hao, Q. (2006). Agent-based dis-
tributed manufacturing process planning and schedul-
ing: a state-of-the-art survey. IEEE Transactions on
Systems, Man and Cybernetics, Part C (Applications
and Reviews), 36(4):563–577.
Toivonen, V., Järvenpää, E., and Lanz, M. (01.11.2017 -
03.11.2017). Managing production complexity with
intelligent work orders. In Proceedings of the 9th In-
ternational Joint Conference on Knowledge Discov-
ery, Knowledge Engineering and Knowledge Manage-
ment, pages 189–196. SCITEPRESS - Science and
Technology Publications.
Agent-based Decentral Production Planning and Control: A New Approach for Multi-resource Scheduling
451