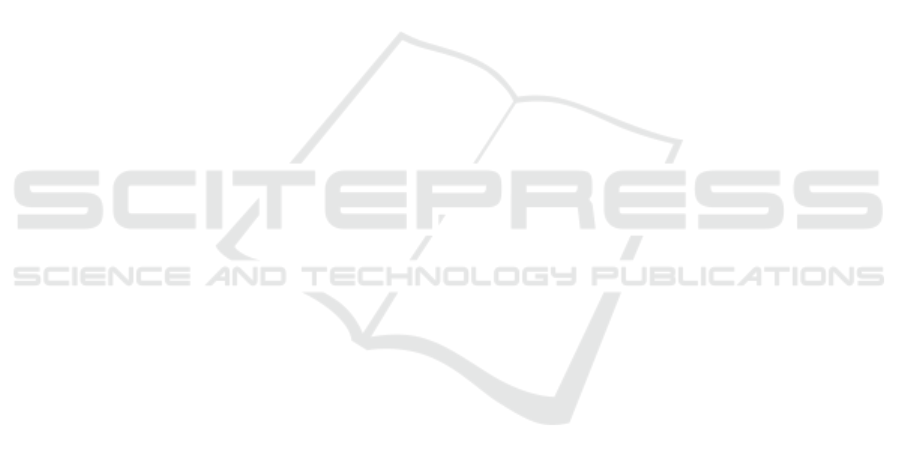
industrial demonstrators for showcasing Industry 4.0
concepts and technologies. We argue that the Smart
Lab misses a digital backbone that would allow us to
easily collect data and track the production. This
digital backbone would help us as researchers to
explore new concepts and create industrial
demonstrators faster. The digital backbone entails a
full enterprise automation stack (as explained in ISA
– 95 standard) developed from open-source tools. The
architecture includes an ERP system (Odoo ERP), a
MES (MES – based on Odoo Manufacturing), and an
IoT Platform (Home Assistant), which was the result
of a DSR approach with 4 design cycles. Our artifact
is not the final state and will continue to be refined as
it will be used in the upcoming industrial
demonstrators.
The presented platform fulfills almost all the
requirements presented earlier. It is composed of
open-source tools (1), has little hard coding involved,
only in the FESTO Agent (2) , includes ERP, MES,
and IoT (3), has a modular architecture through the
containers that hold the programs (4), the response is
close to real-time (5), the virtualization and
information transparency is in place (6). Further
development also seeks to fully complete the
requirements (2) and (5).
The contribution of this paper includes proposed
architecture of the enterprise software stack, a
concrete instantiation of the platform, and the generic
order workflow model.
It is also planned that the OP4SP will be used
further in the context of helping small and medium
sized enterprises (SMEs) by providing minimum
necessary enterprise functionalities and observe their
digitization journey. Moreover, the stack will
facilitate research into implementation of industry 4.0
technologies, with respect to SMEs as well.
REFERENCES
Awouda, A. et al. (2019) ‘Practical Implementation of
Industry 4.0 Based on Open Access Tools and
Technologies’, in IFIP Advances in Information and
Communication Technology. Springer, pp. 94–103.
Franzosa, R. (2019) Magic Quadrant for Manufacturing
Execution Systems. Available at: https://www.gartner
.com/en/documents/3970825/magic-quadrant-for-man
ufacturing-execution-systems (Accessed: 18 December
2020).
De Jong, E., Lalla-Sewgoolam, B. and Vainberg, G. (2019)
Unlocking the full power of automation in industrials.
Kagermann, H. (2015) ‘Change through digitization—
value creation in the age of industry 4.0’, in
Management of Permanent Change. Springer
Science+Business Media, pp. 23–45.
Kim, M., Lee, J. and Jeong, J. (2019) ‘Open Source Based
Industrial IoT Platforms for Smart Factory: Concept,
Comparison and Challenges’, in Lecture Notes in
Computer Science (including subseries Lecture Notes
in Artificial Intelligence and Lecture Notes in
Bioinformatics). Springer Verlag, pp. 105–120.
Li, C., Mantravadi, S. and Møller, C. (2020) ‘AAU Open
Source MES Architecture for Smart Factories -
Exploiting ISA 95’, Ieee International Conference on
Industrial Informatics.
Madsen, O. and Møller, C. (2017) ‘The AAU Smart
Production Laboratory for Teaching and Research in
Emerging Digital Manufacturing Technologies’,
Procedia Manufacturing. Elsevier B.V., 9, pp. 106–
112. doi: 10.1016/j.promfg.2017.04.036.
Mantravadi, S. et al. (2020) ‘Securing IT/OT Links for Low
Power IIoT Devices: Design Considerations for
Industry 4.0’, IEEE Access, 8, pp. 200305–200321. doi:
10.1109/ACCESS.2020.3035963.
Mantravadi, S., Jansson, A. D. and Møller, C. (2020) ‘User-
Friendly MES Interfaces: Recommendations for an AI-
Based Chatbot Assistance in Industry 4.0 Shop Floors’,
in Nguyen, N. T. et al. (eds) Intelligent Information and
Database Systems. Cham: Springer International
Publishing, pp. 189–201.
Martin, J. L. et al. (2010) ‘Preface: Technologies for a
Smarter Planet’, IBM Journal of Research and
Development. doi: 10.1147/JRD.2010.2051498.
Møller, C. (2005) ‘ERP II: a conceptual framework for
next-generation enterprise systems?’, Journal of
Enterprise Information Management. JAI Press, 18(4),
pp. 483–497. Available at: https://vbn.aau.dk/da/
publications/erp-ii-a-conceptual-framework-for-next-g
eneration-enterprise-syst (Accessed: 18 December
2020).
Nardello, M. ; Madsen, O. ; and Møller, C. (2017) The
smart production laboratory A learning factory for
industry 4.0 concepts, CEUR Workshop Proceedings.
CEUR Workshop Proceedings. Available at:
http://ceur-ws.org/Vol-1898/paper13.pdf (Accessed:
27 November 2020).
Queiroz, M. M. et al. (2020) ‘Smart production systems
drivers for business process management improvement:
An integrative framework’, Business Process
Management Journal. Emerald Group Holdings Ltd.,
26(5), pp. 1075–1092. doi: 10.1108/BPMJ-03-2019-
0134.
Ross, J. W. and Weill, D. P. (2006) Enterprise Architecture
as Strategy-Creating a Foundation for Business
Execution. Available at: https://www.researchgate.net/
publication/236972734 (Accessed: 14 December
2020).
Williams, T. J. (1994) ‘The Purdue enterprise reference
architecture’, Computers in Industry, 24(2–3), pp. 141–
158.
ICEIS 2021 - 23rd International Conference on Enterprise Information Systems
714