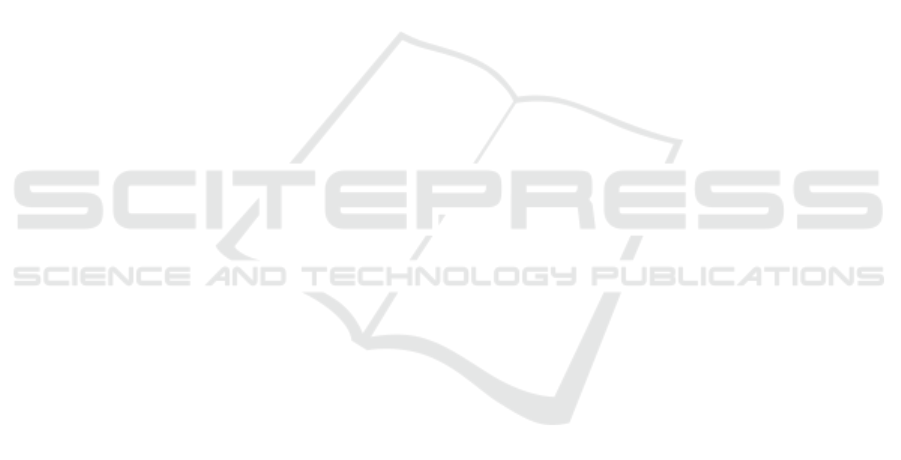
Automation and Robotics, volume 2, pages 231–238,
Reykjav
´
ık.
Gnatzig, S., Schuller, F., and Lienkamp, M. (2012). Human-
machine interaction as key technology for driverless
driving - A trajectory-based shared autonomy control
approach. In 2012 IEEE RO-MAN: The 21st IEEE
International Symposium on Robot and Human Inter-
active Communication, pages 913–918. IEEE.
Hosseini, A. and Lienkamp, M. (2016). Enhancing telep-
resence during the teleoperation of road vehicles using
HMD-based mixed reality. In 2016 IEEE Intelligent
Vehicles Symposium (IV), volume 2016-Augus, pages
1366–1373, Gothenburg. IEEE.
Hosseini, A., Richthammer, F., and Lienkamp, M. (2016).
Predictive Haptic Feedback for Safe Lateral Control
of Teleoperated Road Vehicles in Urban Areas. In
2016 IEEE 83rd Vehicular Technology Conference
(VTC Spring), volume 2016-July, pages 1–7. IEEE.
Hosseini, A., Wiedemann, T., and Lienkamp, M. (2014).
Interactive path planning for teleoperated road vehi-
cles in urban environments. 2014 17th IEEE Interna-
tional Conference on Intelligent Transportation Sys-
tems, ITSC 2014, pages 400–405.
ISO (2018). ISO 26262:2018: Road vehicles - Functional
safety. International Organization for Standardization.
ISO (2019). ISO/PAS 21448:2019: Road vehicles - Safety of
the intended functionality. International Organization
for Standardization.
Leveson, N. G. (2011). Engineering a Safer World: Systems
Thinking Applied to Safety.
Leveson, N. G. and Thomas, J. P. (2018). STPA Handbook.
Lichiardopol S. (2007). A Survey on Teleoperation. Techni-
cal report, Technische Universiteit Eindhoven, Eind-
hoven.
Liu, R., Kwak, D., Devarakonda, S., Bekris, K., and Iftode,
L. (2017). Investigating remote driving over the LTE
network. AutomotiveUI 2017 - 9th International ACM
Conference on Automotive User Interfaces and In-
teractive Vehicular Applications, Proceedings, pages
264–269.
Mallya, A., Pantelic, V., Adedjouma, M., Lawford, M., and
Wassyng, A. (2016). Using STPA in an ISO 26262
Compliant Process. In Safecomp 2016, Lncs 9922,,
volume 1, pages 117–129.
Oscarsson, J., Stolz-Sundnes, M., Mohan, N., and Izosi-
mov, V. (2016). Applying systems-theoretic process
analysis in the context of cooperative driving. In 2016
11th IEEE Symposium on Industrial Embedded Sys-
tems (SIES), pages 1–5. IEEE.
Placke, S., Thomas, J., and Suo, D. (2015). Integration of
Multiple Active Safety Systems using STPA. In SAE
Technical Paper 2015-01-0277.
Rasmussen, J. (1983). Skills, Rules, and Knowledge; Sig-
nals, Signs and Symbols , and Other Distinctions in
Human Performance Models. In IEEE Transactions
on Systems, Man, and Cybernetics, volume 13, pages
257–266. IEEE.
Raste, T., B
¨
ohmert, H., and Houry, A. (2015). Fallback
Strategy for Automated Driving using STPA. In 3rd
European STAMP Workshop, Amsterdam.
SAE International (2018). Surface Vehicle Recommended
Practice - J3016: Taxonomy and Definitions for Terms
Related to Driving Automation Systems for On-Road
Motor Vehicles.
Schimpe, A. and Diermeyer, F. (2020). Steer with Me:
A Predictive, Potential Field-Based Control Approach
for Semi-Autonomous, Teleoperated Road Vehicles.
In The 23rd IEEE International Conference on Intel-
ligent Transportation Systems.
Sheridan, T. and Ferrell, W. (1963). Remote Manipulative
Control with Transmission Delay. IEEE Transactions
on Human Factors in Electronics, HFE-4(1):25–29.
Stolte, T., Hosse, R. S., Becker, U., and Maurer, M.
(2016). On Functional Safety of Vehicle Actuation
Systems in the Context of Automated Driving. IFAC-
PapersOnLine, 49(11):576–581.
Sulaman, S. M., Abbas, T., Wnuk, K., and H
¨
ost, M. (2014).
Hazard analysis of collision avoidance system us-
ing STPA. In ISCRAM 2014 Conference Proceed-
ings - 11th International Conference on Information
Systems for Crisis Response and Management, pages
424–428, Pennsylvania,.
Suo, D., Yako, S., Boesch, M., and Post, K. (2017). In-
tegrating STPA into ISO 26262 Process for Require-
ment Development. In SAE Technical Paper 2017-01-
0058.
Tang, T., Vetter, P., Finkl, S., Figel, K., and Lienkamp, M.
(2014). Teleoperated road vehicles - The ”Free Corri-
dor” as a safety strategy approach. Applied Mechanics
and Materials, 490-491:1399–1409.
Thomas, J. (2013). Extending and automating a systems-
theoretic hazard analysis for requirements generation
and analysis. Phd-thesis, Massachusetts Institute of
Technology.
Thomas, J., Sgueglia, J., Suo, D., Leveson, N., Vernacchia,
M., and Sundaram, P. (2015). An Integrated Approach
to Requirements Development and Hazard Analysis.
In SAE Technical Paper 2015-01-0274.
VEHITS 2021 - 7th International Conference on Vehicle Technology and Intelligent Transport Systems
456