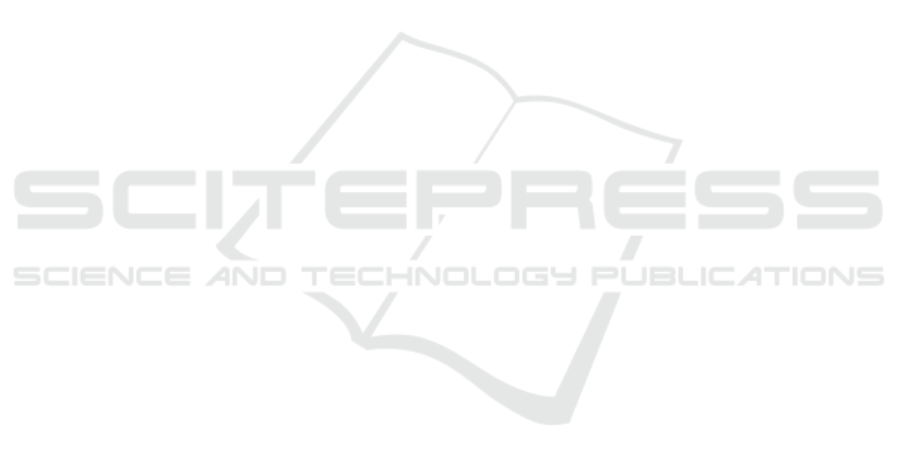
N
´
ıvel Superior - Brasil (CAPES) - Finance Code 001,
Fundac¸
˜
ao De Amparo a Pesquisa Do Estado De Mi-
nas Gerais - FAPEMIG grant code APQ-01331-18,
and the Instituto Tecnol
´
ogico Vale (ITV).
REFERENCES
Almassalkhi, M., Frolik, J., and Hines, P. (2017). Packe-
tized energy management: asynchronous and anony-
mous coordination of thermostatically controlled
loads. In 2017 American Control Conference (ACC),
pages 1431–1437. IEEE.
Amorim, V. J., Silva, M. C., and Oliveira, R. A. (2019).
Software and hardware requirements and trade-offs in
operating systems for wearables: A tool to improve
devices’ performance. Sensors (Basel, Switzerland),
19(8).
Atzori, L., Iera, A., and Morabito, G. (2010). The internet of
things: A survey. Computer networks, 54(15):2787–
2805.
Bilberg, A. and Hadar, R. (2012). Adaptable and reconfig-
urable lean automation-a competitive solution in the
western industry.
Boschert, S., Heinrich, C., and Rosen, R. (2018). Next gen-
eration digital twin. In Proc. TMCE, pages 209–218.
Las Palmas de Gran Canaria, Spain.
Byg, J., Jørgensen, K. Y., and Srba, J. (2009). Tapaal:
Editor, simulator and verifier of timed-arc petri nets.
In International Symposium on Automated Technology
for Verification and Analysis, pages 84–89. Springer.
Da Xu, L., He, W., and Li, S. (2014). Internet of things in
industries: A survey. IEEE Transactions on industrial
informatics, 10(4):2233–2243.
Doltsinis, S., Ferreira, P., and Lohse, N. (2017). A sym-
biotic human–machine learning approach for produc-
tion ramp-up. IEEE Transactions on Human-Machine
Systems, 48(3):229–240.
Fortino, G., Savaglio, C., and Zhou, M. (2017). Toward
opportunistic services for the industrial internet of
things. In 2017 13th IEEE Conference on Automa-
tion Science and Engineering (CASE), pages 825–
830. IEEE.
Gabor, T., Belzner, L., Kiermeier, M., Beck, M. T., and
Neitz, A. (2016). A simulation-based architecture for
smart cyber-physical systems. In 2016 IEEE Interna-
tional Conference on Autonomic Computing (ICAC),
pages 374–379. IEEE.
Garrocho, C., Ferreira, C. M. S., Junior, A., Cavalcanti,
C. F., and Oliveira, R. R. (2019). Industry 4.0: Smart
contract-based industrial internet of things process
management. In Anais do IX Simp
´
osio Brasileiro de
Engenharia de Sistemas Computacionais, pages 137–
142. SBC.
Holdowsky, J., Mahto, M., Raynor, M. E., and Cotteleer, M.
(2015). Inside the internet of things (iot): A primer on
the technologies building the iot. Deloitte University
Press.
Jezequel, L., Fabre, E., and Khomenko, V. (2015). Factored
planning: From automata to petri nets. ACM Trans-
actions on Embedded Computing Systems (TECS),
14(2):1–25.
Kolberg, D. and Z
¨
uhlke, D. (2015). Lean automa-
tion enabled by industry 4.0 technologies. IFAC-
PapersOnLine, 48(3):1870–1875.
Lasi, H., Fettke, P., Kemper, H.-G., Feld, T., and Hoffmann,
M. (2014). Industry 4.0. Business & information sys-
tems engineering, 6(4):239–242.
Latorre-Biel, J.-I., Faul
´
ın, J., Juan, A. A., and Jim
´
enez-
Mac
´
ıas, E. (2018). Petri net model of a smart fac-
tory in the frame of industry 4.0. IFAC-PapersOnLine,
51(2):266–271.
Lomotey, R. K., Pry, J., and Sriramoju, S. (2017). Wearable
iot data stream traceability in a distributed health in-
formation system. Pervasive and Mobile Computing,
40:692–707.
Masri, A., Bourdeaud’Huy, T., and Toguyeni, A. (2009).
Performance analysis of ieee 802.11 b wireless net-
works with object oriented petri nets. Electronic Notes
in Theoretical Computer Science, 242(2):73–85.
Qi, Q. and Tao, F. (2018). Digital twin and big data to-
wards smart manufacturing and industry 4.0: 360 de-
gree comparison. Ieee Access, 6:3585–3593.
Romero, D., Stahre, J., Wuest, T., Noran, O., Bernus, P.,
Fast-Berglund,
˚
A., and Gorecky, D. (2016). Towards
an operator 4.0 typology: a human-centric perspec-
tive on the fourth industrial revolution technologies. In
Proceedings of the International Conference on Com-
puters and Industrial Engineering (CIE46), Tianjin,
China, pages 29–31.
Rosen, R., Von Wichert, G., Lo, G., and Bettenhausen,
K. D. (2015). About the importance of autonomy and
digital twins for the future of manufacturing. IFAC-
PapersOnLine, 48(3):567–572.
Saldivar, A. A. F., Li, Y., Chen, W.-n., Zhan, Z.-h., Zhang,
J., and Chen, L. Y. (2015). Industry 4.0 with cyber-
physical integration: A design and manufacture per-
spective. In 2015 21st international conference on
automation and computing (ICAC), pages 1–6. IEEE.
Samie, F., Tsoutsouras, V., Xydis, S., Bauer, L., Soudris,
D., and Henkel, J. (2016). Distributed qos manage-
ment for internet of things under resource constraints.
In Proceedings of the Eleventh IEEE/ACM/IFIP Inter-
national Conference on Hardware/Software Codesign
and System Synthesis, pages 1–10.
Samsung Research (2020). 6G the next hyper-connected
experience for all.
Schluse, M., Priggemeyer, M., Atorf, L., and Rossmann, J.
(2018). Experimentable digital twins—streamlining
simulation-based systems engineering for industry
4.0. IEEE Transactions on Industrial Informatics,
14(4):1722–1731.
Silva, M. and Oliveira, R. (2019). Analyzing the effect
of increased distribution on a wearable appliance. In
2019 IEEE 43rd Annual Computer Software and Ap-
plications Conference (COMPSAC), volume 2, pages
13–18. IEEE.
Sisinni, E., Saifullah, A., Han, S., Jennehag, U., and Gid-
lund, M. (2018). Industrial internet of things: Chal-
lenges, opportunities, and directions. IEEE Transac-
tions on Industrial Informatics, 14(11):4724–4734.
ICEIS 2021 - 23rd International Conference on Enterprise Information Systems
646