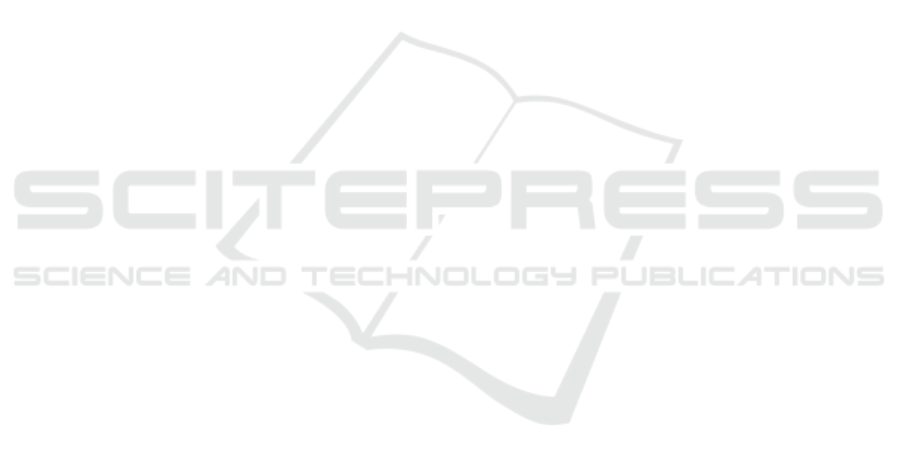
thereby improving product quality and minimising
downtime. This paper focuses on the problems that
are caused by the latency issues in large databases due
to the application of MQTT and suggests potential so-
lutions. This paper is organized as follows. Section 2
discusses related work and concepts in this area of re-
search. Section 3 presents a case study on storage of
data in the industry and the problems associated with
it. Section 4 analyzes the MQTT experimental obser-
vations. Section 5 proposes a new system architecture
for real-time data analysis that works well in simula-
tion. Finally, Section 6 concludes the paper and sug-
gests a roadmap for installation of the architecture on
the actual commercial process.
2 PRELIMINARIES AND
RELATED WORK
The work in this paper considers data engineering
challenges for Cyber Physical System (CPS) applica-
tions in Industry 4.0. Such applications require op-
timized manufacturing processes for smart allocation
of intelligent manufacturing subsystems for the pur-
pose of production. The objective is to support cus-
tomer optimized individual (so called ‘Batch size 0’)
product manufacturing. This intelligent control of
subsystem utilization enables cycle time, reliability,
security, logistics and circular economy/sustainability
considerations to be actively managed. Therefore, the
first objective of the the work is to select an informa-
tion transfer protocol that directly Industry 4.0 aims of
resource efficient production through the use of state-
of-the-art CPS infrastructure (M
¨
oller, 2016).
2.1 Industry 4.0
Industry 4.0 denotes the arrival of Internet of
Things(IoT), smart devices, sensor networks, and the
entire cyber-physical systems (CPS) which power the
cloud based manufacturing systems (Vaidya et al.,
2018). First industrial revolution was powered by the
invention of water and steam powered engines and
machines. Second industrial revolution or which can
be termed as “Industry 2.0” was made possible due
to the arrival of the mass production of goods using
electrical engines and machines. Third industrial rev-
olution or “Industry 3.0” marks the beginning of au-
tomation using PLCs and IT infrastructure. Industry
4.0 is an era of digital manufacturing. Digital manu-
facturing is a process of smart manufacturing, which
fuses the virtual world with the real world through the
cyber-physical infrastructure (M
¨
oller, 2016). This is
aimed to improve the quality and quantity of goods
being manufactured. Industry 4.0 dwells on the prin-
ciples of interoperability, virtualization, decentral-
ization, real-time capability, service orientation and
modularity (Khan et al., 2017).
2.2 MOM Protocols for Industry 4.0
Message-oriented middleware (MOM) is software
and/or hardware infrastructure that dynamically as-
sists the transmission and receipt of messages in
an IoT network. MQTT is a particular instance of
the MOM model based protocol (Banks and Gupta,
2014). MQTT was developed by Andy Stanford-
Clark of IBM in 1999 (Banks and Gupta, 2014)
(Luzuriaga et al., 2015). Other commercial exam-
ples of the MOM protocol include the Advanced Mes-
sage Queuing Protocol (AMQP), and the Data Distri-
bution Service (DDS) protocols. AMQP, created by
John O’Hara at JPMorgan Chase in London in 2003
(Kramer, 2009) (Luzuriaga et al., 2015), provides en-
cryption for the purpose of security(Luzuriaga et al.,
2015) (Novelli et al., 2018). This makes AMQP more
secure but at the same time more resource heavy and
not optimized in terms of power consumption. For
this reason AMQP is not seen as being appropriate
for industry 4.0 applications. DDS is an MOM based
protocol that does not employ a brokerage system
for event driven data flow. (Pardo-Castellote, 2003)
(Yang et al., 2012). DDS systems generally con-
sist of a “databus” which connects the publisher to
the relevant subscriber. A vector of parameters are
used to control the flow of information from the pub-
lisher to the subscriber thereby making it extremely
suitable for secure real-time access. It is necessar-
ily resource-heavy in its implementation and not suit-
able at present for deterministic low-power consum-
ing systems. DDS was initially developed for critical
military applications. DDS does not include a broker
but a set of parameters which control the quality-of-
service (QoS) through management of the informa-
tion flow from the publishers to the subscribers. This
fast and direct control of flow of information in DDS
protocol makes it an excellent choice for real-time
data analysis if it can be deployed in energy limited
low power devices and sensor networks. The use of
DDS is an on going research theme outside the scope
of this paper and will be considered in future work.
2.3 MQTT Fundamentals
MQTT has 3 types of QoS (Silva et al., 2018). QoS 0
denotes that the messages are delivered at most once,
and either the publisher or the subscriber stores the
message. QoS 1 means the publisher stores the mes-
IoTBDS 2021 - 6th International Conference on Internet of Things, Big Data and Security
216