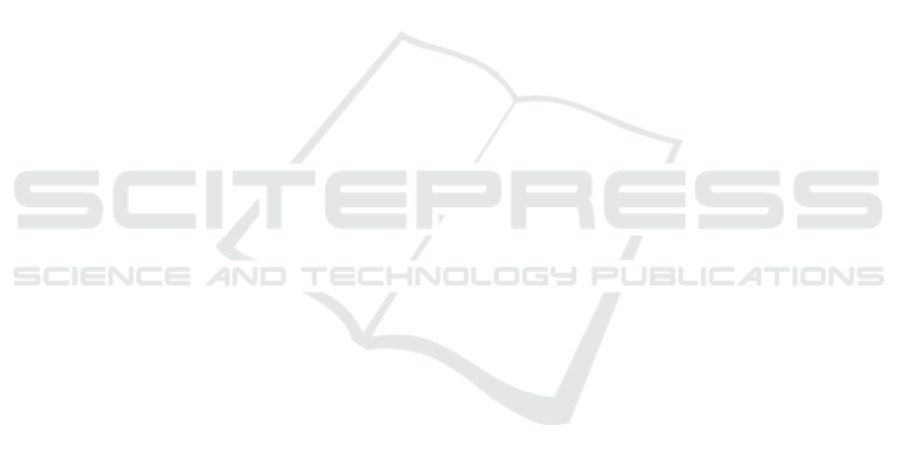
Blender Online Community (2018). Blender - a 3D mod-
elling and rendering package. Blender Foundation.
Cohen, J., Crispim-Junior, C., Grange-Faivre, C., and
Tougne, L. (2020). CAD-based learning for ego-
centric object detection in industrial context. In
15th International Conference on Computer Vision
Theory and Applications, volume 5, pages 644–651.
SCITEPRESS.
Drost, B., Ulrich, M., Bergmann, P., Hartinger, P., and Ste-
ger, C. (2017). Introducing MVTec ITODD-a dataset
for 3d object recognition in industry. In Proceedings
of the IEEE International Conference on Computer
Vision Workshops, pages 2200–2208.
Everingham, M., Van Gool, L., Williams, C. K., Winn,
J., and Zisserman, A. (2010). The pascal visual ob-
ject classes (VOC) challenge. International journal of
computer vision, 88(2):303–338.
Ge, C., Wang, J., Wang, J., Qi, Q., Sun, H., and Liao,
J. (2020). Towards automatic visual inspection: A
weakly supervised learning method for industrial ap-
plicable object detection. Computers in Industry,
121:103232.
Gu
´
erin, J., Gibaru, O., Nyiri, E., Thiery, S., and Palos,
J. (2018a). Automatic construction of real-world
datasets for 3D object localization using two cam-
eras. In IECON 2018-44th Annual Conference of
the IEEE Industrial Electronics Society, pages 3655–
3658. IEEE.
Gu
´
erin, J., Gibaru, O., Nyiri, E., Thieryl, S., and Boots,
B. (2018b). Semantically meaningful view selection.
In 2018 IEEE/RSJ International Conference on Intel-
ligent Robots and Systems (IROS), pages 1061–1066.
IEEE.
He, K., Zhang, X., Ren, S., and Sun, J. (2015). Spatial pyra-
mid pooling in deep convolutional networks for visual
recognition. IEEE transactions on pattern analysis
and machine intelligence, 37(9):1904–1916.
Hinterstoisser, S., Lepetit, V., Wohlhart, P., and Konolige,
K. (2018). On pre-trained image features and syn-
thetic images for deep learning. In Proceedings of the
European Conference on Computer Vision (ECCV).
Hirz, M., Rossbacher, P., and Gulanov
´
a, J. (2017). Future
trends in CAD–from the perspective of automotive
industry. Computer-aided design and applications,
14(6):734–741.
Huang, J., Rathod, V., Sun, C., Zhu, M., Korattikara, A.,
Fathi, A., Fischer, I., Wojna, Z., Song, Y., Guadar-
rama, S., et al. (2017). Speed/accuracy trade-offs for
modern convolutional object detectors. In Proceed-
ings of the IEEE conference on computer vision and
pattern recognition, pages 7310–7311.
Jabbar, A., Farrawell, L., Fountain, J., and Chalup, S. K.
(2017). Training deep neural networks for detecting
drinking glasses using synthetic images. In Interna-
tional Conference on Neural Information Processing,
pages 354–363. Springer.
Jana, A. P., Biswas, A., et al. (2018). YOLO based de-
tection and classification of objects in video records.
In 2018 3rd IEEE International Conference on Recent
Trends in Electronics, Information & Communication
Technology (RTEICT), pages 2448–2452. IEEE.
Kuznetsova, A., Rom, H., Alldrin, N., Uijlings, J., Krasin,
I., Pont-Tuset, J., Kamali, S., Popov, S., Malloci, M.,
Duerig, T., et al. (2018). The open images dataset
v4: Unified image classification, object detection, and
visual relationship detection at scale. arXiv preprint
arXiv:1811.00982.
Lin, T.-Y., Maire, M., Belongie, S., Hays, J., Perona, P., Ra-
manan, D., Doll
´
ar, P., and Zitnick, C. L. (2014). Mi-
crosoft COCO: Common objects in context. In Euro-
pean conference on computer vision, pages 740–755.
Springer.
Lindsay, A., Paterson, A., and Graham, I. (2018). Identi-
fying and quantifying inefficiencies within industrial
parametric CAD models. In Advances in Manufac-
turing Technology XXXII: Proceedings of the 16th In-
ternational Conference on Manufacturing Research,
volume 8, page 227. IOS Press.
Liu, L., Ouyang, W., Wang, X., Fieguth, P., Chen, J., Liu,
X., and Pietik
¨
ainen, M. (2020). Deep learning for
generic object detection: A survey. International jour-
nal of computer vision, 128(2):261–318.
Mazzetto, M., Southier, L. F., Teixeira, M., and Casanova,
D. (2019). Automatic classification of multiple ob-
jects in automotive assembly line. In 2019 24th
IEEE International Conference on Emerging Tech-
nologies and Factory Automation (ETFA), pages 363–
369. IEEE.
Peng, X., Sun, B., Ali, K., and Saenko, K. (2015). Learning
deep object detectors from 3D models. In Proceed-
ings of the IEEE International Conference on Com-
puter Vision, pages 1278–1286.
Prasad, D. K. (2012). Survey of the problem of object de-
tection in real images. International Journal of Image
Processing (IJIP), 6(6):441.
Rajpura, P. S., Bojinov, H., and Hegde, R. S. (2017). Ob-
ject detection using deep CNNs trained on synthetic
images. arXiv preprint arXiv:1706.06782.
Ren, S., He, K., Girshick, R., and Sun, J. (2015). Faster R-
CNN: Towards real-time object detection with region
proposal networks. In Advances in neural information
processing systems, pages 91–99.
Shirley, P. and Morley, R. K. (2003). Realistic ray tracing.
AK Peters/CRC Press.
Xiao, Y., Tian, Z., Yu, J., Zhang, Y., Liu, S., Du, S., and
Lan, X. (2020). A review of object detection based
on deep learning. Multimedia Tools and Applications,
pages 1–63.
Yang, J., Li, S., Wang, Z., and Yang, G. (2019). Real-time
tiny part defect detection system in manufacturing us-
ing deep learning. IEEE Access, 7:89278–89291.
Zhang, X., Yang, Y.-H., Han, Z., Wang, H., and Gao, C.
(2013). Object class detection: A survey. ACM Com-
puting Surveys (CSUR), 46(1):1–53.
Zhou, B., Lapedriza, A., Khosla, A., Oliva, A., and Tor-
ralba, A. (2017). Places: A 10 million image database
for scene recognition. IEEE transactions on pattern
analysis and machine intelligence, 40(6):1452–1464.
ICEIS 2021 - 23rd International Conference on Enterprise Information Systems
82