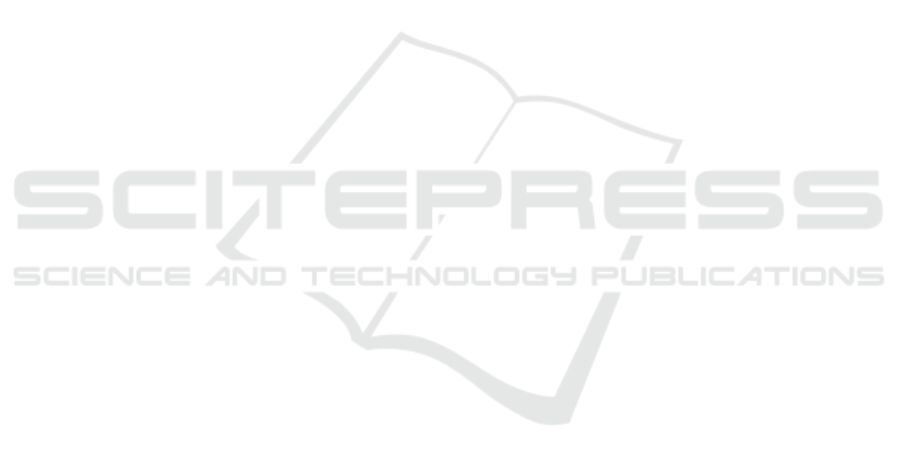
ness, inconsistency and conflict), in order to satisfy
the configuration(s) with a feature model. The ap-
plicability of the proposed approach is demonstrated
through AOCS family/product line. It is noteworthy
that the proposed approach is generally applicable to
the broad range of scenarios and domains.
In the future, we plan to perform automatic extrac-
tion of feature and configuration models from docu-
ment files. We also plan to consider additional scenar-
ios and application, such as electric quarry site (Javed
et al., 2020). Another direction for future work is
to attach the evidence obtained from runtime model
checking with the assurance cases that are constructed
to provide comprehensive, logical and defensible jus-
tification of the safety and security of a reconfigurable
production system (Muram et al., 2020).
ACKNOWLEDGEMENTS
This work is partially supported by FiC (Future fac-
tories in the Cloud) project funded by SSF (Swedish
Foundation for Strategic Research). The third author
has also participated during the tenure of an ERCIM
“Alain Bensoussan” Fellowship Programme.
REFERENCES
Cimatti, A., Clarke, E. M., Giunchiglia, F., and Roveri,
M. (1999). NuSMV: A new symbolic model veri-
fier. In 11th Int’l Conf. on Computer Aided Verifica-
tion (CAV), pages 495–499.
Classen, A., Heymans, P., Schobbens, P., and Legay, A.
(2011). Symbolic model checking of software product
lines. In 33rd International Conference on Software
Engineering, ICSE ’11, Waikiki, Honolulu, HI, USA,
pages 321–330.
Gan, X., Dubrovin, J., and Heljanko, K. (2014). A sym-
bolic model checking approach to verifying satellite
onboard software. Sci. Comput. Program., 82:44–55.
Gruler, A., Leucker, M., and Scheidemann, K. D. (2008).
Modeling and model checking software product lines.
In 10th IFIP WG 6.1 International Conference on For-
mal Methods for Open Object-Based Distributed Sys-
tems, FMOODS ’08, Oslo, Norway, volume 5051,
pages 113–131.
Javed, M. A. and Gallina, B. (2018). Safety-oriented pro-
cess line engineering via seamless integration between
EPF composer and BVR tool. In 22nd International
Systems and Software Product Line Conference - Vol-
ume 2, SPLC ’18, Gothenburg, Sweden, pages 23–28.
Javed, M. A., Gallina, B., and Carlsson, A. (2019). To-
wards variant management and change impact anal-
ysis in safety-oriented process-product lines. In
34th ACM/SIGAPP Symposium on Applied Comput-
ing, SAC ’19, Limassol, Cyprus, pages 2372–2375.
Javed, M. A., Muram, F. U., Fattouh, A., and Punnekkat, S.
(2020). Enforcing geofences for managing automated
transportation risks in production sites. In Depend-
able Computing - EDCC Workshops, DREAMS ’20,
Munich, Germany, volume 1279, pages 113–126.
Lauenroth, K., Pohl, K., and Toehning, S. (2009). Model
checking of domain artifacts in product line engineer-
ing. In 24th IEEE/ACM International Conference on
Automated Software Engineering, ASE ’09, Auckland,
New Zealand, pages 269–280.
Lochau, M., Mennicke, S., Baller, H., and Ribbeck, L.
(2016). Incremental model checking of delta-oriented
software product lines. J. Log. Algebraic Methods
Program., 85(1):245–267.
Muram, F. U., Javed, M. A., Hansson, H., and Punnekkat,
S. (2020). Dynamic reconfiguration of safety-critical
production systems. In 25th IEEE Pacific Rim Interna-
tional Symposium on Dependable Computing, PRDC
’20, Perth, Australia, pages 120–129.
Muram, F. U., Javed, M. A., Tran, H., and Zdun, U. (2017).
Towards a framework for detecting containment viola-
tions in service choreography. In 2017 IEEE Interna-
tional Conference on Services Computing, SCC’ 17,
Honolulu, HI, USA, pages 172–179.
Muram, F. U., Tran, H., and Zdun, U. (2015). Counterex-
ample analysis for supporting containment checking
of business process models. In 13th International
Business Process Management Workshops, BPM ’15,
Innsbruck, Austria, volume 256, pages 515–528.
Muram, F. U., Tran, H., and Zdun, U. (2016). A model
checking based approach for containment checking of
UML sequence diagrams. In 23rd Asia-Pacific Soft-
ware Engineering Conference, APSEC ’16, Hamilton,
New Zealand, pages 73–80.
Muram, F. U., Tran, H., and Zdun, U. (2019). Support-
ing automated containment checking of software be-
havioural models using model transformations and
model checking. Sci. Comput. Program., 174:38–71.
Pnueli, A. (1977). The temporal logic of programs. In
18th Annual Symposium on Foundations of Computer
Science, Providence, Rhode Island, USA, SFCS ’77,
pages 46–57.
Shi, Y., Wei, O., and Zhou, Y. (2014). Model check-
ing partial software product line designs. In Interna-
tional Workshop on Innovative Software Development
Methodologies and Practices, InnoSWDev ’14, Hong
Kong, China, pages 21–29.
ter Beek, M. H., Legay, A., Lluch-Lafuente, A., and Vandin,
A. (2016). Statistical model checking for product
lines. In 7th International Symposium on Leveraging
Applications of Formal Methods, Verification and Val-
idation, ISoLA ’16, Imperial, Corfu, Greece, volume
9952, pages 114–133.
Supporting Automated Verification of Reconfigurable Systems with Product Lines and Model Checking
305