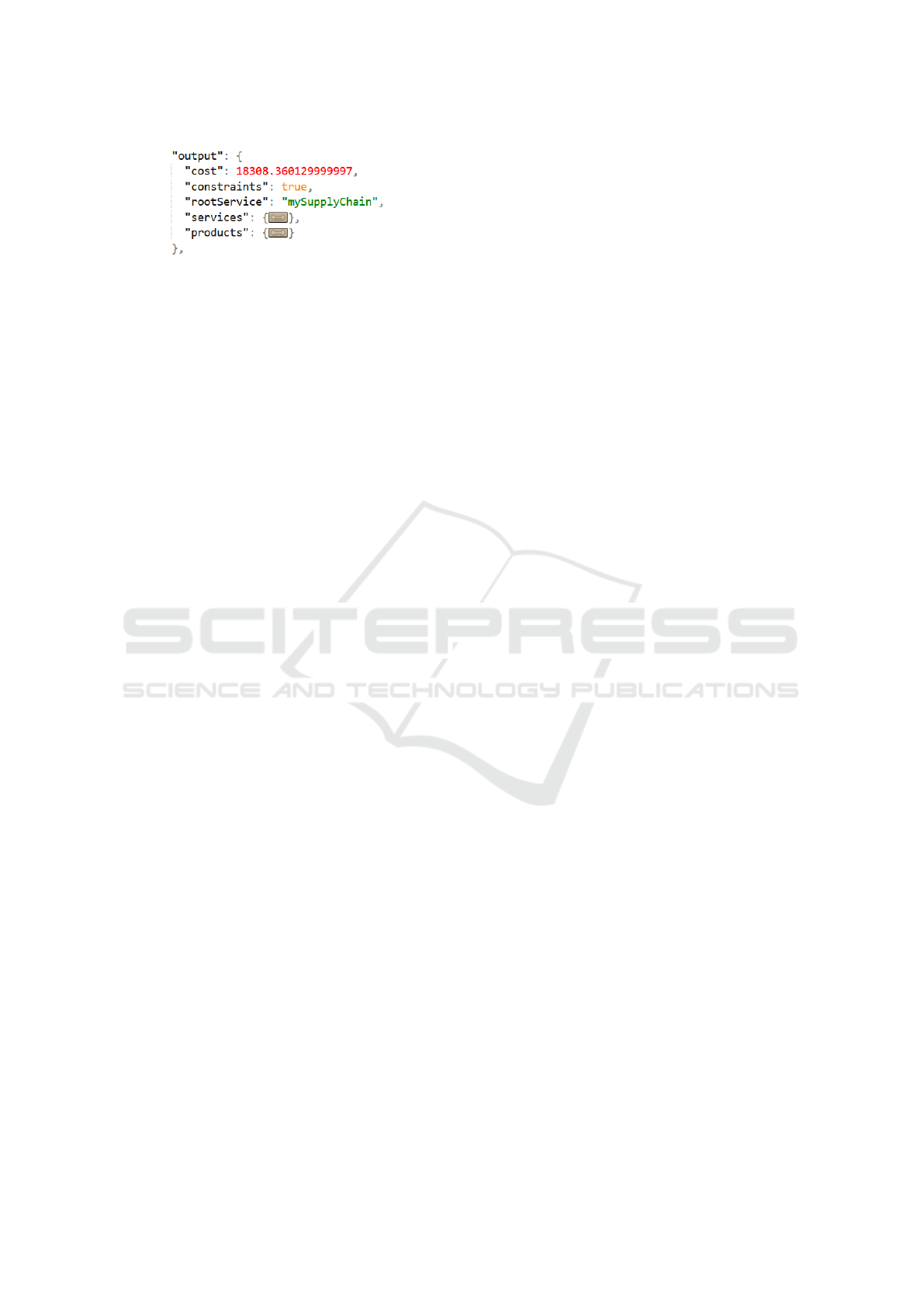
Figure 5: Valid Output Data Structure.
of the metrics for the Sub-Service which comprise of
the bikeSupplyChain.
6 CONCLUSION AND FUTURE
RESEARCH
This research is the first step toward developing a
decision guidance system for combined optimization
over product design, process design, and supply chain
management all while keeping the lower level math-
ematical programming code hidden from the domain
users. The prototype, SPOT, was successfully tested
on a virtual bicycle product and service network.
The methodology in creating hierarchical data input,
which describes the assembly of product and services
using the described input data structure, successfully
generated a valid output data structure with the cor-
rect optimal solution. This modular composite of the
life cycle of product design is unique in the fact that
it joins the optimization of traditionally silo’d project
spaces and adds to the agility of realizing product
and services using distributed manufacturing capac-
ity. Many research questions remain open. Future
research directions include expanding the functional-
ity of SPOT, integrating the application with existing
design tools such as CAD and CAM, creating a graph-
ical user interface to design the hierarchical relation-
ships.
REFERENCES
Towards agile engineering of mechatronic systems in ma-
chinery and plant construction.
Brodsky, A., Gingold, Y., LaToza, T. D., Yu, L.-F., and Han,
X. (2021). Catalyzing the agility, accessibility, and
predictability of the manufacturing-entrepreneurship
ecosystem through design environments and markets
for virtual things. In 10th Intern. Conf. on Oper-
ations Research and Enterprise Systems (ICORES-
2021), pages 264–272.
Brodsky, A., Krishnamoorthy, M., Bernstein, W. Z., and
Nachawati, M. O. (2016). A system and architecture
for reusable abstractions of manufacturing processes.
In 2016 IEEE International Conference on Big Data
(Big Data), pages 2004–2013.
Brodsky, A., Krishnamoorthy, M., Nachawati, M. O., Bern-
stein, W. Z., and Menasc
´
e, D. A. (2017). Manufactur-
ing and contract service networks: Composition, op-
timization and tradeoff analysis based on a reusable
repository of performance models. In 2017 IEEE In-
ternational Conference on Big Data (Big Data), pages
1716–1725.
Brodsky, A., Nachawati, M. O., Krishnamoorthy, M., Bern-
stein, W. Z., and Menasc
´
e, D. A. (2019). Factory op-
tima: a web-based system for composition and anal-
ysis of manufacturing service networks based on a
reusable model repository. International Journal of
Computer Integrated Manufacturing, 32(3):206–224.
Denkena, B., Shpitalni, M., Kowalski, P., Molcho, G., and
Zipori, Y. (2007). Knowledge management in process
planning. CIRP Annals, 56(1):175 – 180.
Eddy, D. C., Krishnamurty, S., Grosse, I. R., Wileden, J. C.,
and Lewis, K. E. (2015). A predictive modelling-
based material selection method for sustainable prod-
uct design. Journal of Engineering Design, 26(10-
12):365–390.
Garcia, D. J. and You, F. (2015). Supply chain design and
optimization: Challenges and opportunities. Comput-
ers & Chemical Engineering, 81:153 – 170. Special
Issue: Selected papers from the 8th International Sym-
posium on the Foundations of Computer-Aided Pro-
cess Design (FOCAPD 2014), July 13-17, 2014, Cle
Elum, Washington, USA.
Helu, M. and Hedberg, T. (2015). Enabling smart manufac-
turing research and development using a product life-
cycle test bed. Procedia Manufacturing, 1:86 – 97.
43rd North American Manufacturing Research Con-
ference, NAMRC 43, 8-12 June 2015, UNC Charlotte,
North Carolina, United States.
Herrmann, J., Cooper, J., Gupta, S., Hayes, C., Ishii, K.,
Kazmer, D., Sandborn, P., and Wood, W. (2004). New
directions in design for manufacturing. volume 3.
Klingstam, P. and Gullander, P. (1999). Overview of simula-
tion tools for computer-aided production engineering.
Computers in Industry, 38(2):173 – 186.
McLean, C. and Shao, G. (2003). Manufacturing case stud-
ies: Generic case studies for manufacturing simula-
tion applications. In Proceedings of the 35th Confer-
ence on Winter Simulation: Driving Innovation, WSC
’03, page 1217–1224. Winter Simulation Conference.
Molcho, G., Zipori, Y., Schneor, R., Rosen, O., Goldstein,
D., and Shpitalni, M. (2008). Computer aided manu-
facturability analysis: Closing the knowledge gap be-
tween the designer and the manufacturer. CIRP An-
nals, 57(1):153 – 158.
Salvendy, G. (2001). Handbook of Industrial Engineering:
Technology and Operations Management.
Shehadi, A. I.-H. S. (2019). On the move: manufacturing’s
return to the developed world. FDiIntelligence.
Stoll, H. W. (1986). Design for Manufacture: An Overview.
Applied Mechanics Reviews, 39(9):1356–1364.
Wu, D., Greer, M. J., Rosen, D. W., and Schaefer, D. (2013).
Cloud manufacturing: Strategic vision and state-of-
the-art. Journal of Manufacturing Systems, 32(4):564
– 579.
ICEIS 2021 - 23rd International Conference on Enterprise Information Systems
728