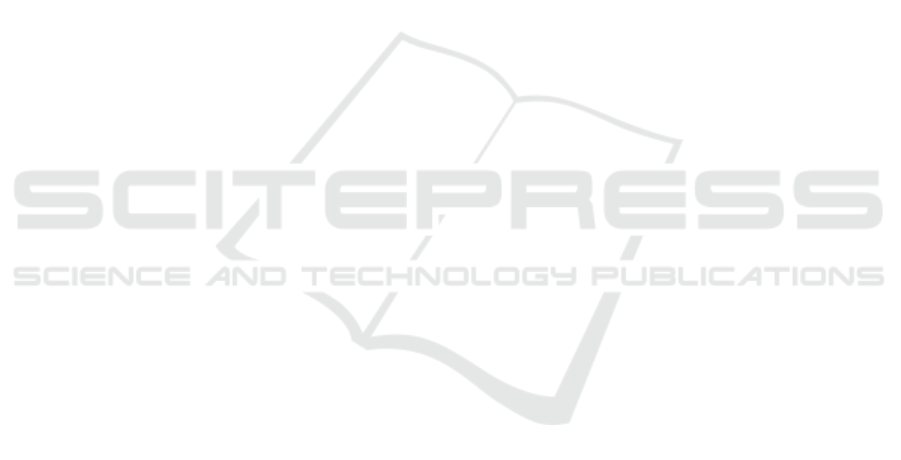
ment between the technical team, the business repre-
sentatives of the customer side, and the IT department
on the customer side. This communication network is
crucial for Lean R&D projects to work. For solutions
to be delivered in an agile way, there must be an align-
ment among all stakeholders.
5 CONCLUSIONS
Through our experiences, interviews with develop-
ers, and usability data from questionnaires with end
users, we have learned interesting lessons from ap-
plying Lean R&D in an industry-academia collabora-
tion in the oil and gas field, specifically in the IAGO
project.
We found that not only communication with all
stakeholders is crucial for this type of agile collabo-
ration, but also, in particular, end-user involvement is
key to avoid misunderstandings and rework. Because
of the short cycles with frequent deliveries and the
experimentation nature of the process, it is important
to continually evaluate the evolving solution with the
end users and customers and keep all parties informed
about changes in the project.
When following the Lean R&D approach in the
future, we plan to schedule early knowledge-sharing
meetings about the domain, so that all participants in
the LI workshop will be able to make well-informed
decisions and elicit features and requirements that are
valuable to both the business and the end users.
REFERENCES
Abras, C., Maloney-krichmar, D., and Preece, J. (2004).
User-Centered Design. In In Bainbridge, W. Ency-
clopedia of Human-Computer Interaction, Thousand
Oaks. Sage Publications.
Aguiar, F. and Caroli, P. (2020). Product Backlog Building:
Concepção de um Product Backlog Efetivo. Editora
Caroli.
Bashir Shaban, K., Kadri, A., and Rezk, E. (2016). Ur-
ban Air Pollution Monitoring System With Forecast-
ing Models. IEEE Sensors Journal, 16(8):2598–2606.
Cadei, L., Camarda, G., Montini, M., Rossi, G., Fier, P.,
Bianco, A., Lancia, L., Loffreno, D., Corneo, A., Mi-
lana, D., Carrettoni, M., and Silvestri, G. (2019). Pre-
diction and prescription of operation upset in H2S gas
sweetening unit: Implementation of an innovative big
data analytics procedure. In Offshore Mediterranean
Conference, pages 1–9, Ravenna.
Caroli, P. (2018). Lean Inception: Como Alinhar Pessoas e
Construir o Produto Certo. Editora Caroli, 1st edition.
Cohn, M. (2004). User Stories Applied: For Agile Software
Development. Addison-Wesley Professional, USA.
Corbin, J. and Strauss, A. (2007). Basics of Qualitative
Research: Techniques and Procedures for Developing
Grounded Theory. SAGE Publications, Inc, Los An-
geles, Calif, 3rd edition edition.
Davis, F. D. (1989). Perceived Usefulness, Perceived Ease
of Use, and User Acceptance of Information Technol-
ogy. MIS Quarterly, 13(3):319–340.
Du, D., Jiang, X., Sun, H., and Nie, Z. (2019). An
APSO-BP Prediction Modeling of Malodorous Gas
in Landfill Based on Historical Data. In Proceedings
of the 2019 International Conference on Artificial In-
telligence and Computer Science, AICS 2019, page
390–393, New York, NY, USA. ACM.
Groysman, A. (2017). Corrosion problems and solutions
in oil, gas, refining and petrochemical industry. Ko-
roze a ochrana materialu, 61(3):100–117. Publisher:
Sciendo Section: Koroze a ochrana materialu.
Harper, B. D., Slaughter, L. A., and Norman, K. L. (1997).
Questionnaire Administration Via the WWW: A val-
idation & Reliability Study for a User Satisfaction
Questionnaire. In Proceedings of World Conference
on the WWW, Internet and Intranet, WebNet 97.
Kalinowski, M., Lopes, H., Teixeira, A. F., da Silva Car-
doso, G., Kuramoto, A., Itagyba, B., Batista, S. T.,
Pereira, J. A., Silva, T., Warrak, J. A., da Costa, M. S.,
Fischer, M., Salgado, C., Teixeira, B. R., Chueke, J.,
Ferreira, B., Lima, R., Villamizar, H., Brandão, A.,
Barbosa, S. D. J., Poggi, M., Pelizaro, C., Lemes, D.,
Waltemberg, M., Lopes, O., and Goulart, W. (2020).
Lean r&d: An agile research and development ap-
proach for digital transformation. In Morisio, M.,
Torchiano, M., and Jedlitschka, A., editors, Product-
Focused Software Process Improvement - 21st In-
ternational Conference, PROFES 2020, Turin, Italy,
November 25-27, 2020, Proceedings, volume 12562
of Lecture Notes in Computer Science, pages 106–
124. Springer.
Kuusinen, K. (2014). Improving UX Work in Scrum De-
velopment: A Three-Year Follow-Up Study in a Com-
pany. In Sauer, S., Bogdan, C., Forbrig, P., Bernhaupt,
R., and Winckler, M., editors, Human-Centered Soft-
ware Engineering, Lecture Notes in Computer Sci-
ence, pages 259–266, Berlin, Heidelberg. Springer.
Lárusdóttir, M. K., Cajander, Å., and Simader, M. (2014).
Continuous Improvement in Agile Development Prac-
tice. In Sauer, S., Bogdan, C., Forbrig, P., Bernhaupt,
R., and Winckler, M., editors, Human-Centered Soft-
ware Engineering, Lecture Notes in Computer Sci-
ence, pages 57–72, Berlin, Heidelberg. Springer.
Rettig, M. (1994). Prototyping for tiny fingers. Communi-
cations of the ACM, 37(4):21–27.
Sandberg, A., Pareto, L., and Arts, T. (2011). Agile Col-
laborative Research: Action Principles for Industry-
Academia Collaboration. IEEE Software, 28(4):74–
83. Conference Name: IEEE Software.
Yousif, J. H. (2016). Forecasting Hydrogen sulfide Level
Based Neural Computation. International Journal of
Computation and Applied Sciences, 1(1):21–26.
ICEIS 2021 - 23rd International Conference on Enterprise Information Systems
352