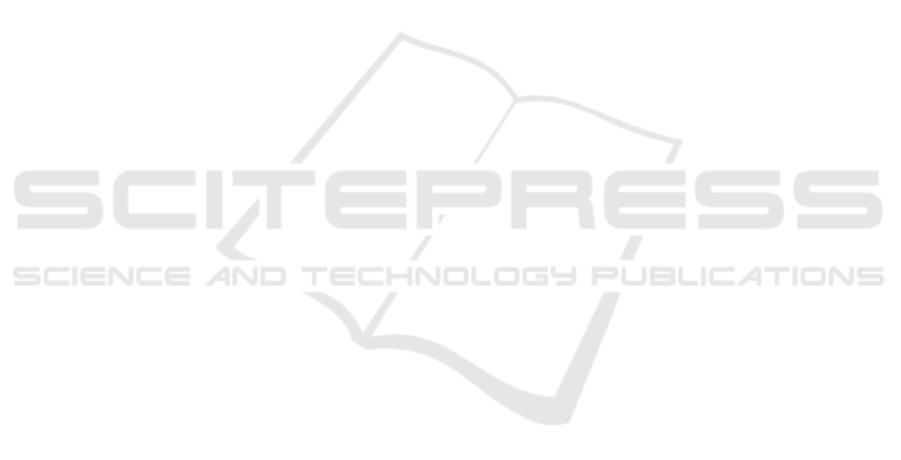
demand transmission for edge-assisted remote control
in industrial network systems. IEEE Transactions on
Industrial Informatics, 16(7):4842–4854.
Dongbing Gu and Huosheng Hu (2006). Receding
horizon tracking control of wheeled mobile robots.
IEEE Transactions on Control Systems Technology,
14(4):743–749.
Esen, H., Adachi, M., Bernardini, D., Bemporad, A., Rost,
D., and Knodel, J. (2015). Control as a service
(caas): Cloud-based software architecture for automo-
tive control applications. In Proceedings of the Second
International Workshop on the Swarm at the Edge of
the Cloud, page 13–18, New York, NY, USA.
Findeisen, R. and Varutti, P. (2009). Stabilizing Nonlinear
Predictive Control over Nondeterministic Communi-
cation Networks, pages 167–179. Springer Berlin Hei-
delberg, Berlin, Heidelberg.
Gr
¨
une, L., Allg
¨
ower, F., Findeisen, R., Fischer, J., Groß, D.,
Hanebeck, U. D., Kern, B., M
¨
uller, M. A., Pannek, J.,
Reble, M., Stursberg, O., Varutti, P., and Worthmann,
K. (2014). Distributed and Networked Model Predic-
tive Control, pages 111–167. Springer International
Publishing, Heidelberg.
Gubbi, J., Buyya, R., Marusic, S., and Palaniswami, M.
(2013). Internet of things (iot): A vision, architectural
elements, and future directions. Future Generation
Computer Systems, 29(7):1645 – 1660.
Hegazy, T. and Hefeeda, M. (2015). Industrial automation
as a cloud service. IEEE Transactions on Parallel and
Distributed Systems, 26(10):2750–2763.
Hespanha, J. P., Naghshtabrizi, P., and Xu, Y. (2007). A
survey of recent results in networked control systems.
Proceedings of the IEEE, 95(1):138–162.
Hojjat A. Izadi, B. W. G. and Zhang, Y. (2011). Decentral-
ized model predictive control for cooperative multiple
vehicles subject to communication loss. International
Journal of Aerospace Engineering, 2011:1–13.
Kaur, K., Garg, S., Aujla, G. S., Kumar, N., Rodrigues, J. J.
P. C., and Guizani, M. (2018). Edge computing in the
industrial internet of things environment: Software-
defined-networks-based edge-cloud interplay. IEEE
Communications Magazine, 56(2):44–51.
Kiani, A. and Ansari, N. (2018). Edge computing aware
noma for 5g networks. IEEE Internet of Things Jour-
nal, 5(2):1299–1306.
Liu, G., Xia, Y., Chen, J., Rees, D., and Hu, W. (2007).
Networked predictive control of systems with random
network delays in both forward and feedback chan-
nels. IEEE Transactions on Industrial Electronics,
54(3):1282–1297.
Mayne, D., Rawlings, J., Rao, C., and Scokaert, P. (2000).
Constrained model predictive control: Stability and
optimality. Automatica, 36(6):789 – 814.
Mehrez, M. W., Mann, G. K. I., and Gosine, R. G. (2013).
Stabilizing nmpc of wheeled mobile robots using
open-source real-time software. In 2013 16th Inter-
national Conference on Advanced Robotics (ICAR),
pages 1–6.
Pallasch, C., Wein, S., Hoffmann, N., Obdenbusch, M.,
Buchner, T., Waltl, J., and Brecher, C. (2018). Edge
powered industrial control: Concept for combining
cloud and automation technologies. In 2018 IEEE In-
ternational Conference on Edge Computing (EDGE),
pages 130–134.
Pin, G. and Parisini, T. (2011). Networked predictive con-
trol of uncertain constrained nonlinear systems: Re-
cursive feasibility and input-to-state stability analysis.
IEEE Transactions on Automatic Control, 56(1):72–
87.
Qiu, T., Chi, J., Zhou, X., Ning, Z., Atiquzzaman, M.,
and Wu, D. O. (2020). Edge computing in indus-
trial internet of things: Architecture, advances and
challenges. IEEE Communications Surveys Tutorials,
22(4):2462–2488.
Rimal, B. P., Van, D. P., and Maier, M. (2017). Mobile
edge computing empowered fiber-wireless access net-
works in the 5g era. IEEE Communications Magazine,
55(2):192–200.
Rohmer, E., Singh, S. P. N., and Freese, M. (2013). V-rep:
A versatile and scalable robot simulation framework.
In 2013 IEEE/RSJ International Conference on Intel-
ligent Robots and Systems, pages 1321–1326.
Sisinni, E., Saifullah, A., Han, S., Jennehag, U., and Gid-
lund, M. (2018). Industrial internet of things: Chal-
lenges, opportunities, and directions. IEEE Transac-
tions on Industrial Informatics, 14(11):4724–4734.
Skarin, P., Eker, J., Kihl, M., and
˚
Arz
´
en, K.-E. (2019).
Cloud-assisted model predictive control. In 2019
IEEE International Conference on Edge Computing
(EDGE), pages 110–112.
Skarin, P., T
¨
arneberg, W.,
˚
Arzen, K., and Kihl, M. (2018).
Towards mission-critical control at the edge and over
5g. In 2018 IEEE International Conference on Edge
Computing (EDGE), pages 50–57.
Trevisan, M., Safari Khatouni, A., and Giordano, D. (2020).
ERRANT: Realistic emulation of radio access net-
works. Computer Networks, 176:107289.
Ulusoy, A., Gurbuz, O., and Onat, A. (2011). Wire-
less model-based predictive networked control system
over cooperative wireless network. IEEE Transactions
on Industrial Informatics, 7(1):41–51.
Vick, A., Guhl, J., and Kr
¨
uger, J. (2016). Model predic-
tive control as a service — concept and architecture
for use in cloud-based robot control. In 2016 21st
International Conference on Methods and Models in
Automation and Robotics (MMAR), pages 607–612.
Wan, J., Tang, S., Shu, Z., Li, D., Wang, S., Imran, M., and
Vasilakos, A. V. (2016). Software-defined industrial
internet of things in the context of industry 4.0. IEEE
Sensors Journal, 16(20):7373–7380.
Xu, H., Yu, W., Griffith, D., and Golmie, N. (2018). A sur-
vey on industrial internet of things: A cyber-physical
systems perspective. IEEE Access, 6:78238–78259.
Yaqoob, I., Ahmed, E., Hashem, I. A. T., Ahmed, A. I. A.,
Gani, A., Imran, M., and Guizani, M. (2017). Internet
of things architecture: Recent advances, taxonomy,
requirements, and open challenges. IEEE Wireless
Communications, 24(3):10–16.
Zhao, P. and D
´
an, G. (2018). A benders decomposi-
tion approach for resilient placement of virtual pro-
cess control functions in mobile edge clouds. IEEE
Transactions on Network and Service Management,
15(4):1460–1472.
An Approach to Reduce Network Effects in an Industrial Control and Edge Computing Scenario
303