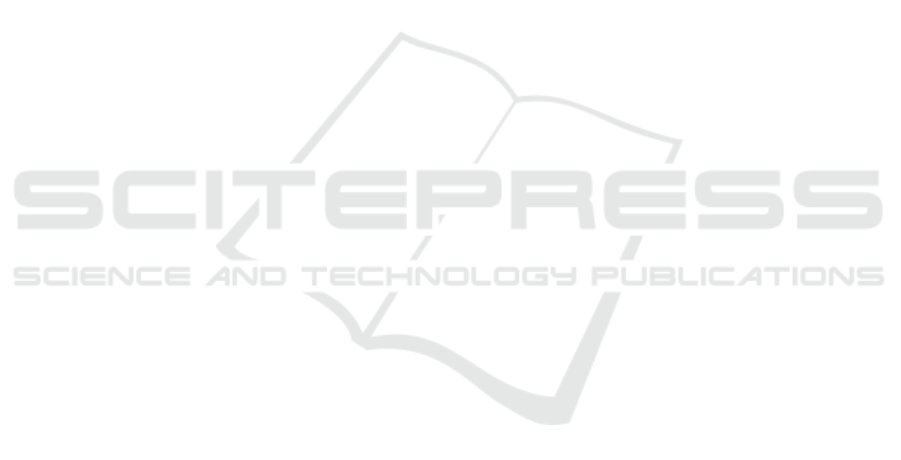
health and safety and are expected to continue to do
so in the future (International Labour Office, 2019).
Thus, the need for new engineering solutions applied
to OHS is evident.
Some solutions in this regard foresee the use of
wearable computing, virtual reality and augmented
reality for human assistance in dangerous and diverse
activities. Wearable smart devices are already being
used to monitor worker fatigue and fall detection, for
example (International Labour Office, 2019).
In this perspective, this paper’s main objective
is to review and investigate the technologies already
used in confined spaces and also to describe some
promising solutions to support human activities in
these environments, since working in these places is
still classified as high risk and harmful to employees’
health. Thus, this study is a preliminary investiga-
tion for the improvement of these technologies and
serves as a theoretical foundation for the development
of wearable devices in confined spaces. The work, in
current progress by the authors and still in its infancy,
proposes to display monitoring data on augmented re-
ality glasses in a more practical and intuitive way for
confined workers. An example application under de-
velopment is the computational coloring of naturally
colorless gas concentrations for users of these glasses.
2 CONFINED SPACES
The concept of confined spaces is understood as any
area not designed for continuous human occupation
that has limited means of entry and exit. According to
the US Occupational Safety and Health Administra-
tion (OSHA), three characteristics define a confined
space: (i) it is large enough and configured so that an
employee is able to enter and perform the work, (ii)
it has limited entry or exit opening, (iii) and it is not
designed for human occupation (OSHA, 1993). Ex-
amples of confined spaces include, but are not limited
to, silos, ducts, boilers, storage tanks, sewage ditches,
chimneys and underground galleries.
When developing a regulatory procedure on work
in confined spaces, OSHA estimated, in 1993, that 4.8
million entrances into confined spaces were made an-
nually in the United States and they involved an av-
erage of 1.6 million workers and 63 deaths (Burlet-
Vienney et al., 2015).
The most common causes of accidents in these
places are fires, explosions, spontaneous combustion
and contact with extremely high temperatures (Botti
et al., 2017). Tasks in confined spaces involve physi-
cal, chemical, biological and ergonomic risks to the
health of employees, the risk of asphyxiation and
intoxication being among the most common (Botti
et al., 2018).
These risks are present in several industrial seg-
ments. In mining, in non-ferrous metal mining ac-
tivities, the accumulation of methane gas in coal
mines and toxic concentrations of hydrochloric acid
are some of the sources of risks and dangers to
which workers are exposed in these locations (Dr
¨
ager,
2015). In the chemical industry, a case study in 2005
reported a fatal accident in the US where two workers
at a refinery were asphyxiated inside a confined space
filled with nitrogen (CSB, 2005).
Simply put, the most effective risk control mea-
sure for working in a confined space is not to enter
the confined area (Botti et al., 2018). In this trend,
robotic systems and stand-alone operations for work
in confined environments have gained prominence. In
a systematic review of automated solutions for enter-
ing these places, 60 scientific articles that document
the use of these tools, produced between 1999 and
2015, were cataloged (Botti et al., 2017).
At first, one can imagine that the future of con-
fined spaces will be dominated by these innovative
non-human entry technologies. However, they are
still limited to certain industrial operations such as
cleaning, inspection and maintenance. Moreover, be-
cause they are places with rigid and divergent oper-
ational parameters, autonomous solutions for work
in confined environments are limited to the activities
to which the solutions were initially designed (Botti
et al., 2017).
From this perspective, it is certain that research
in this area will considerably evolve the flexibility
of robots for access in distinct operations, but even
so, certain activities will still require human pres-
ence in these locations. To remove automatic cleaning
residues in naval tanks, for example, human interven-
tion is still required (Botti et al., 2017).
Perhaps the greatest gain obtained from the inser-
tion of robots in confined environments is the reduc-
tion in the time that workers remain in these places.
Thus, the work done in these environments tends to
be guided by hybrid systems of human-computer in-
teraction.
This paradigm shift is observed not only in con-
fined spaces, but also in the industry as a whole. This
is what enthusiasts consider the philosophy of the re-
cent Industry 5.0, where humans work together with
robots or computer instruments integrated into their
bodies to improve their physical, sensory and cogni-
tive capabilities (Longo et al., 2020).
If in Industry 4.0 technology has advanced to-
wards interconnecting machines and cyber-physical
systems to the processes, in Industry 5.0 the focus
ICEIS 2021 - 23rd International Conference on Enterprise Information Systems
574