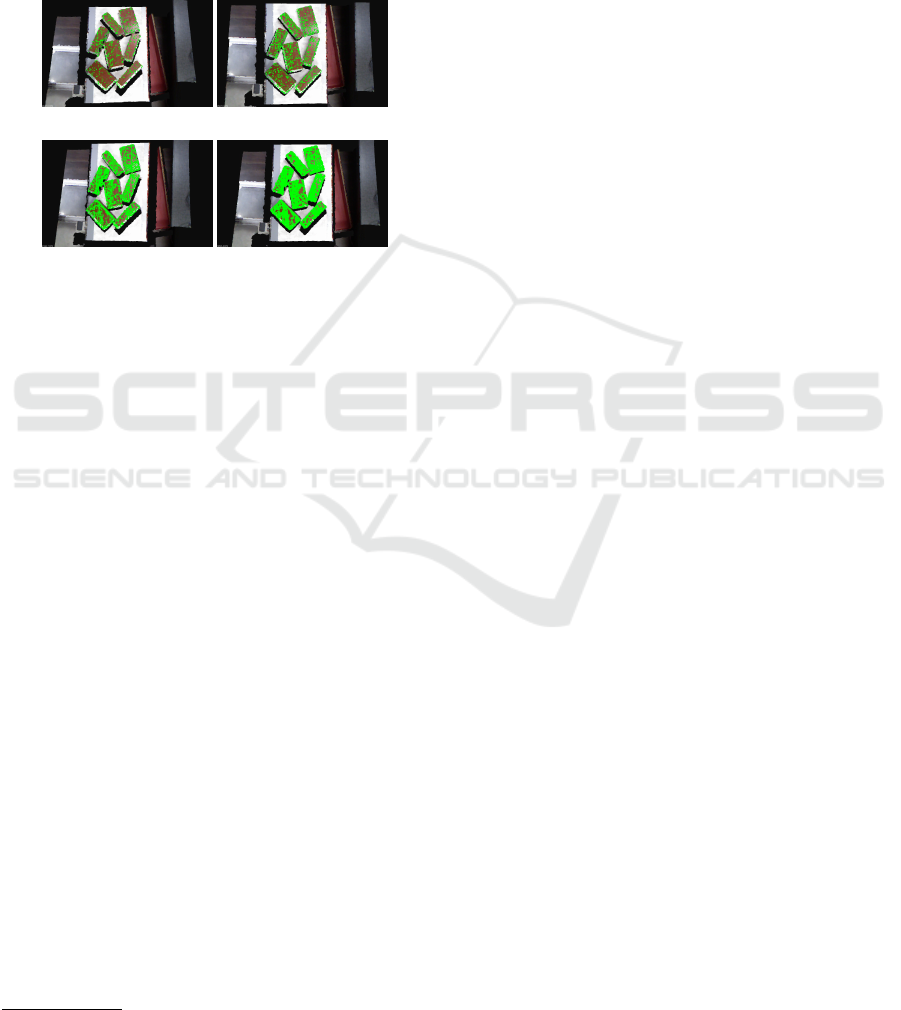
nearest neighbors. We apply their method
2
on raw
point cloud data with k vary from 4 to 30 as shown in
Fig. 10. The results of the method (Bazazian et al.,
2015) is unsatisfactory on the same data set where our
method perform very well. It is because of the inher-
ent noise in the sensor, points on a flat surface has
large variations. Thus all eigenvalues of the covari-
ance matrix will be large, hence predicts the sharp
edges even at the flat surface.
(a) k = 4 (b) k = 5
(c) k = 10 (d) k = 30
Figure 10: Edges from covariance matrix based method.
6 CONCLUSION
Novel edge and corner detection algorithm for un-
organized point clouds was proposed and tested on
generic objects like a coffee mug, dragon, bunny, and
clutter of random objects. The algorithm is used for
6D pose estimation of known objects in clutter for
robotic pick and place applications. The proposed
technique is tested on two warehouse scenarios, when
objects are placed distinctly and when objects are
placed in a dense clutter. Results of each scenario
is reported in the paper along with the computation
time at each step. To demonstrate the efficacy of the
edge extraction technique, we compared it with the
covariance matrix based solution for 3D edge extrac-
tions from unorganized point cloud in a real scenario
and report better performance. The overall approach
is tested in a warehouse application where a real UR5
robot manipulator is used for robotic pick and place
operations.
REFERENCES
Asadi, K. and Han, K. (2018). Real-time image-to-bim reg-
istration using perspective alignment for automated
construction monitoring. In Construction Research
Congress, volume 2018, pages 388–397.
2
https://github.com/denabazazian/
Bazazian, D., Casas, J. R., and Ruiz-Hidalgo, J. (2015).
Fast and robust edge extraction in unorganized point
clouds. In 2015 International Conference on Digi-
tal Image Computing: Techniques and Applications
(DICTA), pages 1–8. IEEE.
Changali, S., Mohammad, A., and van Nieuwland, M.
(2015). The construction productivity imperative.
How to build megaprojects better.„McKinsey Quar-
terly.
Collet, A., Martinez, M., and Srinivasa, S. S. (2011). The
moped framework: Object recognition and pose esti-
mation for manipulation. The International Journal of
Robotics Research, 30(10):1284–1306.
Demarsin, K., Vanderstraeten, D., Volodine, T., and Roose,
D. (2007). Detection of closed sharp edges in point
clouds using normal estimation and graph theory.
Computer-Aided Design, 39(4):276–283.
Doliotis, P., McMurrough, C. D., Criswell, A., Middleton,
M. B., and Rajan, S. T. (2016). A 3d perception-based
robotic manipulation system for automated truck un-
loading. In 2016 IEEE International Conference on
Automation Science and Engineering (CASE), pages
262–267. IEEE.
Drost, B., Ulrich, M., Navab, N., and Ilic, S. (2010). Model
globally, match locally: Efficient and robust 3d ob-
ject recognition. In 2010 IEEE computer society con-
ference on computer vision and pattern recognition,
pages 998–1005. Ieee.
Hackel, T., Wegner, J. D., and Schindler, K. (2016). Con-
tour detection in unstructured 3d point clouds. In Pro-
ceedings of the IEEE Conference on Computer Vision
and Pattern Recognition, pages 1610–1618.
Hinterstoisser, S., Lepetit, V., Rajkumar, N., and Konolige,
K. (2016). Going further with point pair features. In
European conference on computer vision, pages 834–
848. Springer.
Kazhdan, M. and Hoppe, H. (2013). Screened poisson sur-
face reconstruction. ACM Transactions on Graphics
(ToG), 32(3):29.
Lai, K., Bo, L., and Fox, D. (2014). Unsupervised fea-
ture learning for 3d scene labeling. In 2014 IEEE In-
ternational Conference on Robotics and Automation
(ICRA), pages 3050–3057. IEEE.
Lowe, D. G. (2004). Distinctive image features from scale-
invariant keypoints. International journal of computer
vision, 60(2):91–110.
Ni, H., Lin, X., Ning, X., and Zhang, J. (2016). Edge de-
tection and feature line tracing in 3d-point clouds by
analyzing geometric properties of neighborhoods. Re-
mote Sensing, 8(9):710.
Parkes, S. (2019). Automated brick laying system and
method of use thereof. US Patent App. 16/047,143.
Pharswan, S. V., Vohra, M., Kumar, A., and Behera, L.
(2019). Domain-independent unsupervised detec-
tion of grasp regions to grasp novel objects. In
2019 IEEE/RSJ International Conference on Intel-
ligent Robots and Systems (IROS), pages 640–645.
IEEE.
Qi, C. R., Su, H., Mo, K., and Guibas, L. J. (2017). Pointnet:
Deep learning on point sets for 3d classification and
ICINCO 2021 - 18th International Conference on Informatics in Control, Automation and Robotics
252