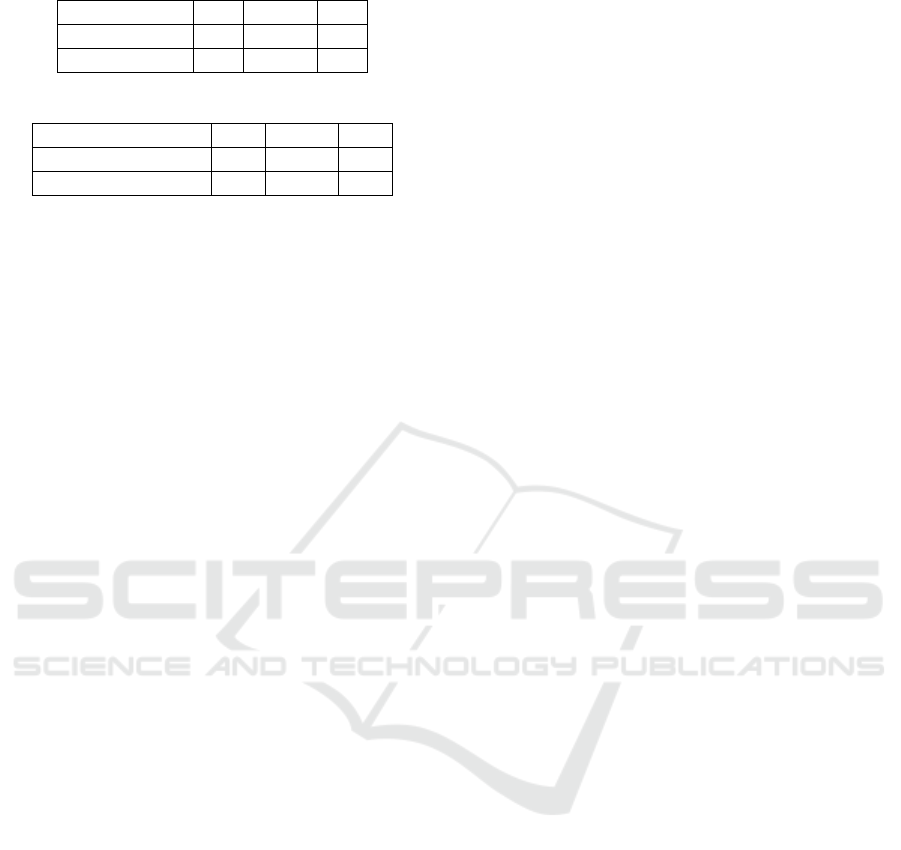
Table 4: CPU time of runs using each strategy.
CP MILP TP
CPU Pb. 1 [s] 5.6 49429 47
CPU Pb. 2 [s] 4.5 3540 3.2
Table 5: Makespan of plans generated with each strategy.
CP MILP TP
Makespan Pb. 1 [s] 128 128 255
Makespan Pb. 2 [s] 189 189 306
The second factor is the CPU time, which is de-
picted for all problems and all planning approaches in
Table 4. All computations were done on a computer
with Intel
R
Core
TM
i5-6200U CPU at 2.30 GHz and 8
GB of RAM. For both problems, CP shows great and
stable performance regarding the CPU time, whereas
MILP is almost impractical. The computational time
with TP is even lower than that with CP for prob-
lem 2, but is also relatively high for problem 1. This
means that when the number of objects in the model
increases, the CPU time with TP also grows rapidly.
Hence, CP is the best choice among these three strate-
gies with respect to the CPU time. Considering the
makespans of the generated plans, as depicted in Ta-
ble 5, CP and MILP are both highly efficient, while
TP shows bad performance.
Moreover, for each strategy multiple ways to de-
velop a model are possible and different models may
lead to different results. This is the case for the TP ap-
proach, where the quality of the plan highly depends
on the matching between the used heuristic and the
model of the planning problem. However, if different
CP or MILP based models are applied for the same
problem, the CPU time may be different, but the gen-
erated plan is always the global optimal solution re-
garding makespan.
5 CONCLUSIONS
In this work the modelling and solving of a complex
task planning problem with three planning strategies
is presented. CP shows the greatest performance in
terms of CPU time and plan quality (makespan of
plans), while temporal planning is the best when con-
sidering the flexibility of the models. In the next steps,
we aim to solve the model with further MILP, CP and
TP planners. A further direction for our future work is
to combine the CP and TP approaches to complement
each other and thus being able to improve the overall
performance on all three factors.
REFERENCES
Behrens, J. K., Lange, R., and Mansouri, M. (2019). A con-
straint programming approach to simultaneous task
allocation and motion scheduling for industrial dual-
arm manipulation tasks. In 2019 International Con-
ference on Robotics and Automation (ICRA). IEEE.
Bezrucav, S.-O. and Corves, B. (2020). Improved ai plan-
ning for cooperating teams of humans and robots. In
Cashmore, M., Orlandini, A., and Finzi, A., editors,
Workshop on Planning and Robotics (PlanRob) at In-
ternational Conference on Automated Planning.
Booth, K. E. C., Tran, T. T., Nejat, G., and Beck, J. C.
(Jan. 2016). Mixed-integer and constraint program-
ming techniques for mobile robot task planning. IEEE
Robotics and Automation Letters, 1(1):500–507.
Coles, A., Coles, A., Fox, M., and Long, D. (2010).
Forward-chaining partial-order planning. In Proceed-
ings of the Twentieth International Conference on
Automated Planning and Scheduling, pages 42–49.
AAAI Press.
Da Col, G. and Teppan, E. (2019). Google vs ibm: A con-
straint solving challenge on the job-shop scheduling
problem. Electronic Proceedings in Theoretical Com-
puter Science, 306:259–265.
Fox, M. and Long, D. (2003). pddl2.1 : An extension to
pddl for expressing temporal planning domains. Jour-
nal Of Artificial Intelligence Research, 20:61–124.
Gervet, C. (2006). Constraints over structured domains. In
Francesca Rossi Peter van Beek Toby Walsh, editor,
Handbook of Constraint Programming, Foundations
of Artificial Intelligence, pages 605–638. Elsevier.
Ku, W.-Y., Beck, J. C. (2016). Mixed integer program-
ming models for job shop scheduling: A computa-
tional analysis. Computers & Operations Research,
73:165–173.
Land, A. H. and Doig, A. G. (1960). An automatic method
of solving discrete programming problems. Econo-
metrica, 28:497–520.
Mokhtarzadeh, M., Tavakkoli-Moghaddam, R., Vahedi-
Nouri, B., and Farsi, A. (2020). Scheduling of
human-robot collaboration in assembly of printed cir-
cuit boards: a constraint programming approach. In-
ternational Journal of Computer Integrated Manufac-
turing, 33(5):460–473.
Murty, K. G. (1985). Linear and Combinatorial Program-
ming. R.E. Krieger.
Rossi, F., Peter van Beek, and Walsh, T., editors (2006).
Handbook of Constraint Programming: Introduction.
Elsevier Science.
Simonis, H. (2001). Building industrial applications with
constraint programming. In Comon, H., Treinen,
R., and March
´
e, C., editors, Constraints in compu-
tational logics: theory and applications, pages 271–
309. Springer-Verlag Berlin Heidelberg, France.
Yi, J.-s., Ahn, M. S., Chae, H., Nam, H., Noh, D., Hong,
D., and Moon, H. (2020). Task planning with mixed-
integer programming for multiple cooking task using
dual-arm robot. In 17th International Conference on
Ubiquitous Robots (UR), pages 29–35. IEEE.
ICINCO 2021 - 18th International Conference on Informatics in Control, Automation and Robotics
122