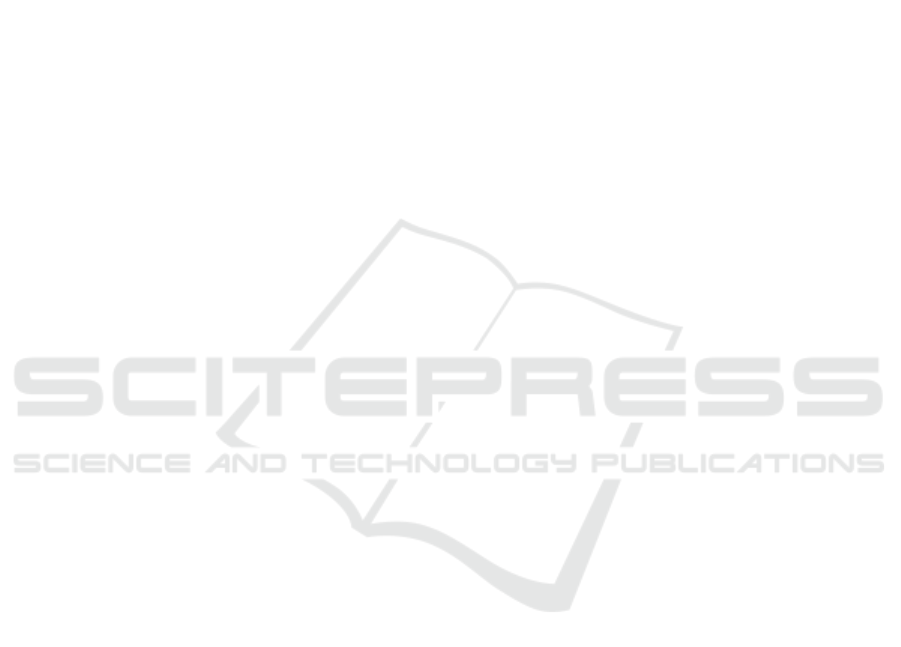
AdvWarp: A Transformation Algorithm for Advanced Modeling of Gas
Compressors and Drives
Anton Baldin
1
, Kl
¨
are Cassirer
1
, Tanja Clees
1,2
, Bernhard Klaassen
1
, Igor Nikitin
1
,
Lialia Nikitina
1
and Sabine Pott
1
1
Fraunhofer Institute for Algorithms and Scientific Computing, Schloss Birlinghoven, 53754 Sankt Augustin, Germany
2
Bonn-Rhine-Sieg University of Applied Sciences, Grantham-Allee 20, 53754 Sankt Augustin, Germany
Anton.Baldin, Klaere.Cassirer, Tanja.Clees, Bernhard.Klaassen, Igor.Nikitin, Lialia.Nikitina, Sabine.Pott
Keywords:
Complex Systems Modeling and Simulation, Non-linear Systems, Applications in Energy Transport.
Abstract:
Solving transport network problems can be complicated by non-linear effects. In the particular case of gas
transport networks, the most complex non-linear elements are compressors and their drives. They are described
by a system of equations, composed of a piecewise linear ‘free’ model for the control logic and a non-linear
‘advanced’ model for calibrated characteristics of the compressor. For all element equations, certain stability
criteria must be fulfilled, providing the absence of folds in associated system mapping. In this paper, we
consider a transformation (warping) of a system from the space of calibration parameters to the space of
transport variables, satisfying these criteria. The algorithm drastically improves stability of the network solver.
Numerous tests on realistic networks show that nearly 100% convergence rate of the solver is achieved with
this approach.
1 INTRODUCTION
In this paper, we continue the construction of globally
converging solver algorithm for stationary transport
network problems. The approach is based on condi-
tions of generalized resistivity formulated in our pre-
vious work (Clees et al., 2018a). Specifically for the
natural gas transport, the modeling of key elements,
the compressors, combines two parts, identified in gas
simulation community as ‘free’ and ‘advanced’ mod-
els. The ‘free’ model represents the control logic of
compressors, related to the fulfillment of goals, such
as the input/output pressure or flow. The ‘advanced’
model describes the individual physical characteris-
tics of compressors determined by calibration proce-
dure. The construction of the algorithm for advanced
modeling of compressors was started in (Clees et al.,
2018b), continued in (Baldin et al., 2020), and further
improved in the present paper.
The advanced model of compressors and drives
considers the space of calibration parameters such as
volumetric flow, revolution number, as well as vari-
ous energy characteristics. Although the representa-
tion of compressors and drives in this space is more
convenient for calibration, for solving transport net-
work problems it is more suitable to represent them
in the space, describing the main transport character-
istics, such as inlet and outlet pressures and mass flow.
It is important to fulfill the conditions of generalized
resistivity (Clees et al., 2018a), which means that the
flow must be an increasing function of the inlet pres-
sure and a decreasing function of the outlet pressure.
For the global convergence of the solver, this condi-
tion must be satisfied everywhere, including the exte-
rior of the working region, since the solver can wan-
der around there during the iterations.
In this work, to construct the element equation, an
improved pixel algorithm from (Clees et al., 2018b)
is used. A triangular grid (Baldin et al., 2020) is im-
plemented, which can be adaptively compressed in
places where higher resolution is required. Warping
of the grid will be performed in the solution loop
whenever the temperature or/and the gas composi-
tion change. This approach provides a simple con-
trol over the system resistivity by calculating the nor-
mals to the triangles. We tested the method on a vari-
ety of realistic examples and obtained nearly 100%
convergence of the solver. The approach enhances
our multi-physics network simulator MYNTS (Clees
et al., 2016).
Modeling of gas transport networks has been de-
scribed in detail in works (Mischner et al., 2011;
Baldin, A., Cassirer, K., Clees, T., Klaassen, B., Nikitin, I., Nikitina, L. and Pott, S.
AdvWarp: A Transformation Algorithm for Advanced Modeling of Gas Compressors and Drives.
DOI: 10.5220/0010512602310238
In Proceedings of the 11th International Conference on Simulation and Modeling Methodologies, Technologies and Applications (SIMULTECH 2021), pages 231-238
ISBN: 978-989-758-528-9
Copyright
c
2021 by SCITEPRESS – Science and Technology Publications, Lda. All rights reserved
231