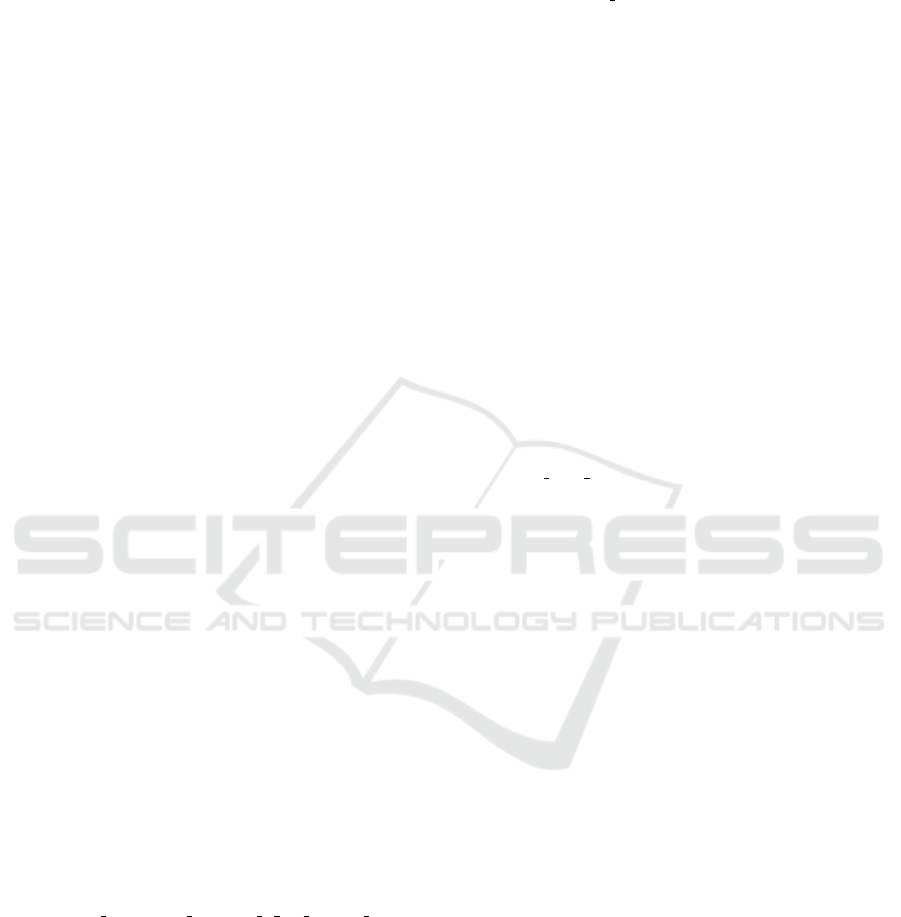
cision basis for a set of trained parameters.
From an engineering point of view we want to fur-
ther improve the solution’s degree of automatization
by employing continuous integration (CI) techniques
(Smart, 2011). CI focuses merging code of individ-
ual programmers frequently. We intend to use the
methodology to automatically test and perhaps recali-
brate the TI whenever new source code is introduced.
8 CONCLUSION
Modern touch screens are both electrical sensors and
digital signal processing units. Often the signal
processing part consists out of multiple components
which must be calibrated precisely in order to as-
sure proper functionality. Additional legal obligations
such as electromagnetic compatibility must be met by
a calibration. We provided automated solution to de-
termine robust parameterizations for the signal pro-
cessing approach. We could not only erase the pain
of calibrating the device by hand, we could also show
that our method leads to a superior calibration.
ACKNOWLEDGEMENT
We would like to thank Mircea Barbu and Carsten
Fischer for supporting and sponsoring this research
project. Furthermore we would like to express our
gratitude towards our BSH colleagues that helped us
understanding the use case and setting up the test bed.
REFERENCES
Arakawa, M., Yamashita, Y., and Funatsu, K. (2011). Ge-
netic Algorithm-based Wavelength Selection Method
for Spectral Calibration. Journal of Chemometrics,
25(1):10–19.
Atmel (2020). Atmel Max Touch Overview.
http://ww1.microchip.com/downloads/en/DeviceDoc/
45071A maXTouch Portfolio E US 060514 Web.
pdf. [Online; accessed 3-December-2020].
B
¨
ack, T., Fogel, D. B., and Michalewicz, Z. (1997). Hand-
book of Evolutionary Computation. IOP Publishing
Ltd., GBR, 1st edition.
Cressie, N. and Wikle, C. (2015). Statistics for Spatio-
Temporal Data. Wiley.
Doerr, A., Nguyen-Tuong, D., Marco, A., Schaal, S., and
Trimpe, S. (2017). Model-based policy search for au-
tomatic tuning of multivariate pid controllers. In 2017
IEEE International Conference on Robotics and Au-
tomation (ICRA), pages 5295–5301.
EU (2014). Directive 2014/30/EU. https:
//ec.europa.eu/growth/single-market/european-
standards/harmonised-standards/electromagnetic-
compatibility en. [Online; accessed 7-December-
2020].
Haga, H. and Suehiro, A. (2012). Automatic test case gen-
eration based on genetic algorithm and mutation anal-
ysis. In 2012 IEEE International Conference on Con-
trol System, Computing and Engineering, pages 119–
123.
Harding, S., Leitner, J., and Schmidhuber, J. (2013). Carte-
sian Genetic Programming for Image Processing,
pages 31–44. Springer New York, New York, NY.
Heider, M., P
¨
atzel, D., and H
¨
ahner, J. (2020). Towards
a Pittsburgh-Style LCS for Learning Manufacturing
Machinery Parametrizations. In Proceedings of the
2020 Genetic and Evolutionary Computation Confer-
ence Companion, GECCO ’20, page 127–128, New
York, NY, USA. Association for Computing Machin-
ery.
Holland, J. H. (1992). Genetic Algorithms. Scientific Amer-
ican, 267(1):66–73.
IEC (2009). 61000-4-6: Testing and Measurement
Techniques – Immunity to conducted Distur-
bances, induced by radio-frequency Fields.
https://www.iecee.org/dyn/www/f?p=106:49:0::::
FSP STD ID:18793. [Online; accessed 3-December-
2020].
Man, K. F. and Tang, K. S. (1997). Genetic Algorithms for
Control and Signal Processing. In Proceedings of the
IECON’97 23rd International Conference on Indus-
trial Electronics, Control, and Instrumentation (Cat.
No.97CH36066), volume 4, pages 1541–1555 vol.4.
Margraf, A., Stein, A., Engstler, L., Geinitz, S., and Hah-
ner, J. (2017). An Evolutionary Learning Approach
to Self-configuring Image Pipelines in the Context of
Carbon Fiber Fault Detection. In 2017 16th IEEE In-
ternational Conference on Machine Learning and Ap-
plications (ICMLA), pages 147–154.
MATT (2020). MATT ROBOT - The ultimate Touchscreen
Testing Tool. https://www.mattrobot.ai/. [Online; ac-
cessed 4-December-2020].
Millo, F., Arya, P., and Mallamo, F. (2018). Optimization of
Automotive Diesel Engine Calibration using Genetic
Algorithm Techniques. Energy, 158:807 – 819.
Neumann, F. and Witt, C. (2010). Bioinspired Computa-
tion in Combinatorial Optimization: Algorithms and
their Computational Complexity. Natural Comput-
ing Series, ISBN 978-3-642-16543-6. Springer-Verlag
Berlin Heidelberg, 2010.
OptoFidelity (2020). Touch Testing. https://www.
optofidelity.com/touch-testing/. [Online; accessed 4-
December-2020].
Rao, K. D. and Swamy, M. N. S. (2018). Digital Signal
Processing: Theory and Practice. Springer Publish-
ing Company, Incorporated, 1st edition.
Ryan, C., Tetteh, M. K., and Mota Dias, D. (2020). Be-
havioural Modelling of Digital Circuits in System Ver-
ilog using Grammatical Evolution. In Proceedings of
An Evolutionary Calibration Approach for Touch Interface Filter Chains
37