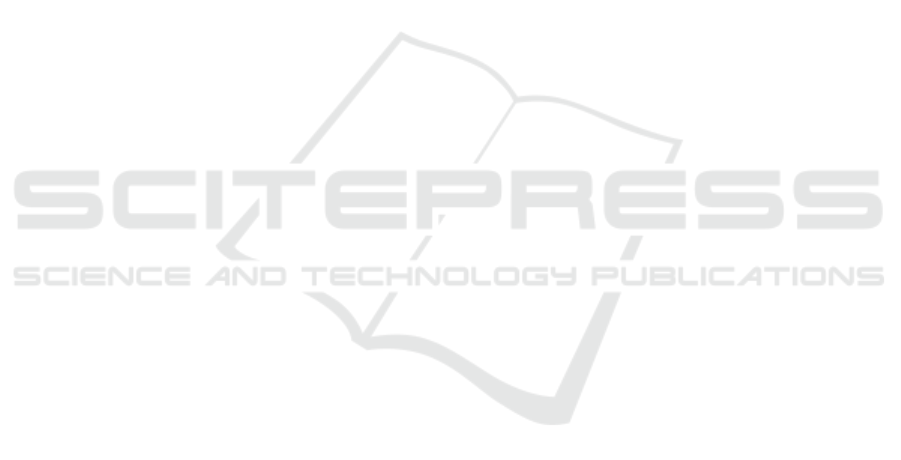
Kale, M. and Chipperfield, A. (2005). Stabilized mpc
formulations for robust reconfigurable flight control.
Control Engineering Practice, 13(6):771–788.
Lee, J. H. (2009). A Lecture on Model Predictive Control.
Pan American Advanced Studies Institute Program on
Process Systems Engineering.
Ma, J., Qin, S. J., Li, B., and Salsbury, T. (2011). Economic
model predictive control for building energy systems.
IEEE, Anaheim, USA.
Maciejowski, J. M. (2002). Predictive control: with con-
straints. Pearson education, London, UK.
Mayne, D. Q., Rawlings, J. B., Rao, C. V., and Scokaert,
P. O. (2000). Constrained model predictive control:
Stability and optimality. Automatica, 36(6):789–814.
Mbungu, N. T., Bansal, R. C., and Naidoo, R. (2019a).
Smart energy coordination of autonomous residential
home. IET Smart Grid, 2(3):336–346.
Mbungu, N. T., Bansal, R. C., Naidoo, R., Miranda, V., and
Bipath, M. (2018). An optimal energy management
system for a commercial building with renewable en-
ergy generation under real-time electricity prices. Sus-
tainable Cities and Society, 41:392–404.
Mbungu, N. T., Bansal, R. C., Naidoo, R. M., Bettayeb, M.,
Siti, M. W., and Bipath, M. (2020). A dynamic energy
management system using smart metering. Applied
Energy, 280:115990.
Mbungu, N. T., Naidoo, R., Bansal, R. C., and Bipath,
M. (2017a). Optimisation of grid connected hybrid
photovoltaic–wind–battery system using model pre-
dictive control design. IET Renewable Power Gen-
eration, 11(14):1760–1768.
Mbungu, N. T., Naidoo, R. M., and Bansal, R. C. (2017b).
Real-time electricity pricing: TOU-MPC based en-
ergy management for commercial buildings. Energy
Procedia, 105:3419–3424.
Mbungu, N. T., Naidoo, R. M., Bansal, R. C., and Vahid-
inasab, V. (2019b). Overview of the optimal smart
energy coordination for microgrid applications. IEEE
Access, 7:163063–163084.
Mbungu, T., Naidoo, R., Bansal, R., and Bipath, M. (2016).
Smart SISO-MPC based energy management system
for commercial buildings: Technology trends. In Fu-
ture Technologies Conference (FTC), pages 750–753,
San Francisco, USA.
Mesbah, A. (2016). Stochastic model predictive control: An
overview and perspectives for future research. IEEE
Control Systems Magazine, 36(6):30–44.
Rawlings, J. B. and Mayne, D. Q. (2009). Model predictive
control: Theory and design. Nob Hill Pub, New York,
USA.
Rossiter, J. A. (2003). Model-based predictive control: a
practical approach. CRC press, New York, USA.
Seborg, D. E., Mellichamp, D. A., Edgar, T. F., and
Doyle III, F. J. (2010). Process dynamics and control.
John Wiley & Sons, USA, 3rd ed edition.
Siti, M. W., Tungadio, D. H., Sun, Y., Mbungu, N. T., and
Tiako, R. (2019). Optimal frequency deviations con-
trol in microgrid interconnected systems. IET Renew-
able Power Generation, 13(13):2376–2382.
Tungadio, D. H., Bansal, R. C., Siti, M. W., and Mbungu,
N. T. (2018). Predictive active power control of
two interconnected microgrids. Technology and
Economics of Smart Grids and Sustainable Energy,
3(3):1–15.
Wang, L. (2009). Model predictive control system design
and implementation using MATLAB
R
. Springer Sci-
ence & Business Media, Girona, Spain.
Xie, L., Li, P., and Wozny, G. (2007). Chance constrained
nonlinear model predictive control. Assessment and
Future Directions of Nonlinear Model Predictive Con-
trol, pages 295–304.
Zhang, Y., Liu, B., Zhang, T., and Guo, B. (2014). An intel-
ligent control strategy of battery energy storage sys-
tem for microgrid energy management under forecast
uncertainties. International Journal of Electrochemi-
cal Science, 9(8):4190–4204.
Model Predictive Control: A Survey of Dynamic Energy Management
129