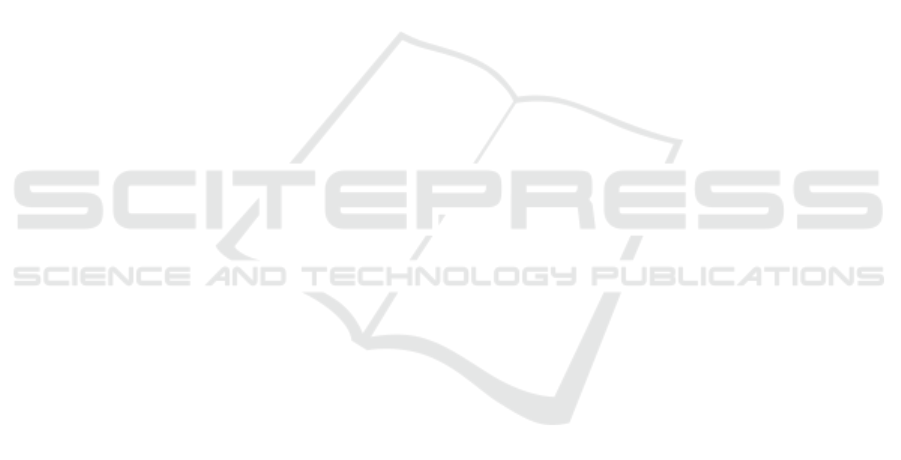
ACKNOWLEDGEMENTS
This work has been supported by FCT - Fundac¸
˜
ao
para a Ci
ˆ
encia e Tecnologia within the Project Scope:
UIDB/05757/2020.
REFERENCES
Adiprawita, W., Ahmad, A., and Sembiring, J. (2008).
Hardware in the loop simulator in uav rapid develop-
ment life cycle. arXiv.
Berndt, J. (2020). Flightgear: an open-source flight simula-
tor.
Boril, J., Leuchter, J., Smrz, V., and Blasch, E. (2015). Avi-
ation simulation training in the czech air force. In
2015 IEEE/AIAA 34th Digital Avionics Systems Con-
ference (DASC), pages 9A2–1. IEEE.
Bruyninckx, H. (2008). V model from structured systems
design theory.
Casner SM, Geven RW, W. K. (2013). The Effectiveness of
Airline Pilot Training for Abnormal Events. Human
Factors.
Cen, F., Li, Q., Fan, L., Liu, Z., and Sun, H. (2015). De-
velopment of a pilot-in-loop real-time simulation plat-
form for wind tunnel free-flight test. In 2015 IEEE In-
ternational Conference on Information and Automa-
tion, pages 2433–2438. IEEE.
Chaudron, J.-B., Saussi
´
e, D., Siron, P., and Adelantado, M.
(2014). Real-time distributed simulations in an hla
framework: Application to aircraft simulation. Simu-
lation, 90(6):627–643.
Chudy, P. and Rzucidlo, P. (2012). Hil simulation of a light
aircraft flight control system. In 31th IEEE Digital
Avionics Systems Conference, pages 6D111–6D112.
IEEE.
Demers, S., Gopalakrishnan, P., and Kant, L. (2007). A
generic solution to software-in-the-loop. Military
Communications Conference 2007. MILCOM 2007.
Ellis, G. (2012). Chapter 13 - model development and
verification. In Ellis, G., editor, Control System
Design Guide (Fourth Edition), pages 261 – 282.
Butterworth-Heinemann, Boston, fourth edition edi-
tion.
Fodor, A., J
´
an
´
o, R., and Fizes
,
an, R. T. (2019). Charac-
terization of the v-model approach in thermal design
process. In 2019 IEEE 25th International Symposium
for Design and Technology in Electronic Packaging
(SIITME), pages 367–370.
Garcia, R. and Barnes, L. (2009). Multi-uav simulator uti-
lizing x-plane. In Selected papers from the 2nd In-
ternational Symposium on UAVs, Reno, Nevada, USA
June 8–10, 2009, pages 393–406. Springer.
Gervais, C., Chaudron, J.-B., Siron, P., Leconte, R., and
Saussi
´
e, D. (2012). Real-time distributed aircraft sim-
ulation through hla. In 2012 IEEE/ACM 16th Interna-
tional Symposium on Distributed Simulation and Real
Time Applications, pages 251–254. IEEE.
Gholkar, A., Isaacs, A., and Arya, H. (2004). Hardware-in-
loop simulator for mini aerial vehicle. Department of
Aerospace Engineering on IIT at Bombay, 2(2).
Gomez, M. (2001). Hardware-in-the-loop simulation. Em-
bedded System Design.
Hays, R. T., Jacobs, J. W., Prince, C., and Salas, E.
(1992). Flight simulator training effectiveness: A
meta-analysis. Military psychology, 4(2):63–74.
Kaden, A., Boche, B., and Luckner, R. (2013). Hardware-
in-the-loop flight simulator – an essential part in the
development process for the automatic flight control
system of a utility aircraft. In AIAA Modeling and
Simulation Technologies Conference and Exhibit.
Khan, A. H., Khan, Z. H., and Khan, S. H. (2014).
Optimized reconfigurable autopilot design for an
aerospace cps. In Computational intelligence for de-
cision support in cyber-physical systems, pages 381–
420. Springer.
Lofaro, R. J. and Smith, K. M. (2012). The aviation op-
erational environment: Integrating a decision-making
paradigm, flight simulator training and an automated
cockpit display for aviation safety. In Technology
Engineering and Management in Aviation: Advance-
ments and Discoveries, pages 241–282. IGI Global.
Lorains, M., MacMahon, C., Ball, K., and Mahoney, J.
(2011). Above real time training for team invasion
sport skills. International Journal of Sports Science
& Coaching, 6(4):537–544.
Louali, R., Belloula, A., Djouadi, M. S., and Bouaziz, S.
(2011). Real-time characterization of ms flight sim-
ulator 2004 for integration into hardware in the loop
architecture. In 19th Mediterranean Conf. on Control
& Automation (MED), pages 1241–1246. IEEE.
Merk, R. and Roessingh, J. (2016). Assessing behaviour of
cognitive agents in a flight simulator with fighter pi-
lots. In 2016 IEEE International Conference on Sys-
tems, Man, and Cybernetics (SMC), pages 004842–
004847. IEEE.
Meyer, A. (2011). X-plane operation manual.
Rajkumar, R., Lee, I., Sha, L., and Stankovic, J. (2010).
Cyber-physical systems: the next computing revolu-
tion. In Design automation conference, pages 731–
736. IEEE.
Sampaio, R. C. B., Becker, M., Freschi, L. W., and Mon-
tanher, M. P. (2013). Novel sil evaluation of an op-
timal h1 controller on the stability of a mav in flight
simulator. In Aerospace Conference, pages 186D11–
186D12. IEEE.
Scamps, A. and Gibbens, P. (2005). Development of a flight
simulator evaluation course at qantas. In AIAA Model-
ing and Simulation Technologies Conference and Ex-
hibit, page 6114.
Shuping, L. and Ling, P. (2008). The research of v model
in testing embedded software. In 2008 International
Conference on Computer Science and Information
Technology, pages 463–466.
Zhang, X. and Mi, C. (2011). Hardware-in-the-loop and
software-in-the-loop testing for vehicle power man-
agement. In In proceedings of Vehicle Power Man-
agement, Power Systems. Springer.
Real Cockpit Proposal for Flight Simulation with Airbus A32x Models: An Overview Description
263