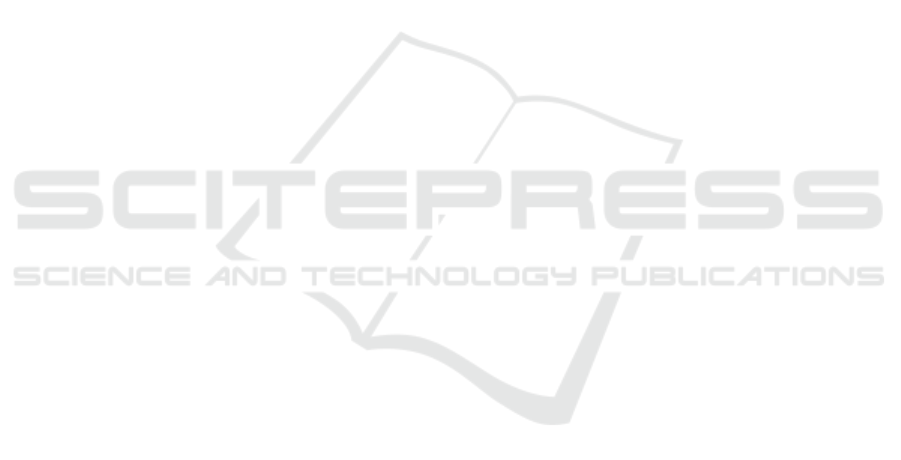
be smaller, lighter, more user-friendly and focus on its
implementation on the real hardware with the devel-
opment alongside of a digital twin. The experiments
with a real robot will address an RGB camera as well
as a thermal camera in order to optimize the cleaning
process with a sensor fusion algorithm. A docking
station for the robot is also equated to charge the bat-
teries of the robot and increase its autonomy.
ACKNOWLEDGEMENTS
This work is financed by National Funds through
the Portuguese funding agency, FCT - Fundac¸
˜
ao
para a Ci
ˆ
encia e a Tecnologia within project
UIDB/50014/2020.
REFERENCES
Akyazi,
¨
O., S¸ahin, E.,
¨
Ozsoy, T., and Alg
¨
ul, M. (2019).
A solar panel cleaning robot design and application.
Avrupa Bilim ve Teknoloji Dergisi, pages 343–348.
Anderson, M., Grandy, A., Hastie, J., Sweezey, A., Ranky,
R., Mavroidis, C., and MARKOPOULOS, Y. P.
(2010). Robotic device for cleaning photovoltaic
panel arrays. In Mobile Robotics: Solutions and Chal-
lenges, pages 367–377. World Scientific.
Aravind, G., Vasan, G., Kumar, T. G., Balaji, R. N., and
Ilango, G. S. (2014). A control strategy for an au-
tonomous robotic vacuum cleaner for solar panels. In
2014 Texas Instruments India Educators’ Conference
(TIIEC), pages 53–61. IEEE.
Campana, P. E., Li, H., and Yan, J. (2013). Dynamic mod-
elling of a pv pumping system with special considera-
tion on water demand. Applied energy, 112:635–645.
Christian, S., Stefan, B., and Michael, K. (2015). Impact
of soiling on iv-curves and efficiency of pv-modules.
Solar Energy, 112:259–262.
Costa, P., Gonc¸alves, J., Lima, J., and Malheiros, P. (2011).
Simtwo realistic simulator: A tool for the develop-
ment and validation of robot software. Theory and
Applications of Mathematics & Computer Science,
1(1):17–33.
Gonc¸alves, J., Lima, J., Costa, P. J., and Moreira, A. P.
(2013). Modeling and simulation of the emg30 geared
motor with encoder resorting to simtwo: the official
robot@ factory simulator. In Advances in Sustainable
and Competitive Manufacturing Systems, pages 307–
314. Springer.
Grando, M. T., Maletz, E. R., Martins, D., Simas, H., and
Simoni, R. (2019). Robots for cleaning photovoltaic
panels: State of the art and future prospects. Revista
Tecnolog
´
ıa Y Ciencia, (35):137–150.
Hashim, N., Mohammed, M., Selvarajan, R. A., Al-
Zubaidi, S., and Mohammed, S. (2019). Study on so-
lar panel cleaning robot. In 2019 IEEE International
Conference on Automatic Control and Intelligent Sys-
tems (I2CACIS), pages 56–61. IEEE.
JKB Energy, . (2018). Get your system cleaned & running
properlys. https://www.jkbenergy.com/blog/2018/4/
30/get-your-system-cleaned-running-properly.
Li, M., Zhang, M., Fu, Y., Guo, W., Zhong, X., Wang,
X., and Chen, F. (2016). Fast and robust mapping
with low-cost kinect v2 for photovoltaic panel clean-
ing robot. In 2016 International Conference on Ad-
vanced Robotics and Mechatronics (ICARM), pages
95–100. IEEE.
Mostefaoui, M., Ziane, A., Bouraiou, A., and Khelifi1, S.
(2019). Effect of sand dust accumulation on pho-
tovoltaic performance in the saharan environment:
southern algeria (adrar). Environmental Science and
Pollution Research, 26(1):259–268.
Ronnaronglit, N. and Maneerat, N. (2019). A cleaning robot
for solar panels. In 2019 5th International Confer-
ence on Engineering, Applied Sciences and Technol-
ogy (ICEAST), pages 1–4. IEEE.
Stridh, B. (2012). Evaluation of economical benefit of
cleaning of soiling and snow in pv plants at three eu-
ropean locations. In 2012 38th ieee photovoltaic spe-
cialists conference, pages 001448–001451. IEEE.
Sundaram, M., Prabhakaran, S., Jishnu, T., and Sharma, S.
(2019). Design and analysis of an autonomous clean-
ing robot for large scale solar pv farms. In Proc. Int.
Conf. Autom. Control, Mechtron. Ind. Eng., page 265.
Zorrilla-Casanova, J., Piliougine, M., Carretero, J.,
Bernaola, P., Carpena, P., Mora-L
´
opez, L., and de Car-
dona, M. S. (2011). Analysis of dust losses in
photovoltaic modules. In World Renewable Energy
Congress-Sweden; 8-13 May; 2011; Sweden, number
057, pages 2985–2992.
SIMULTECH 2021 - 11th International Conference on Simulation and Modeling Methodologies, Technologies and Applications
270