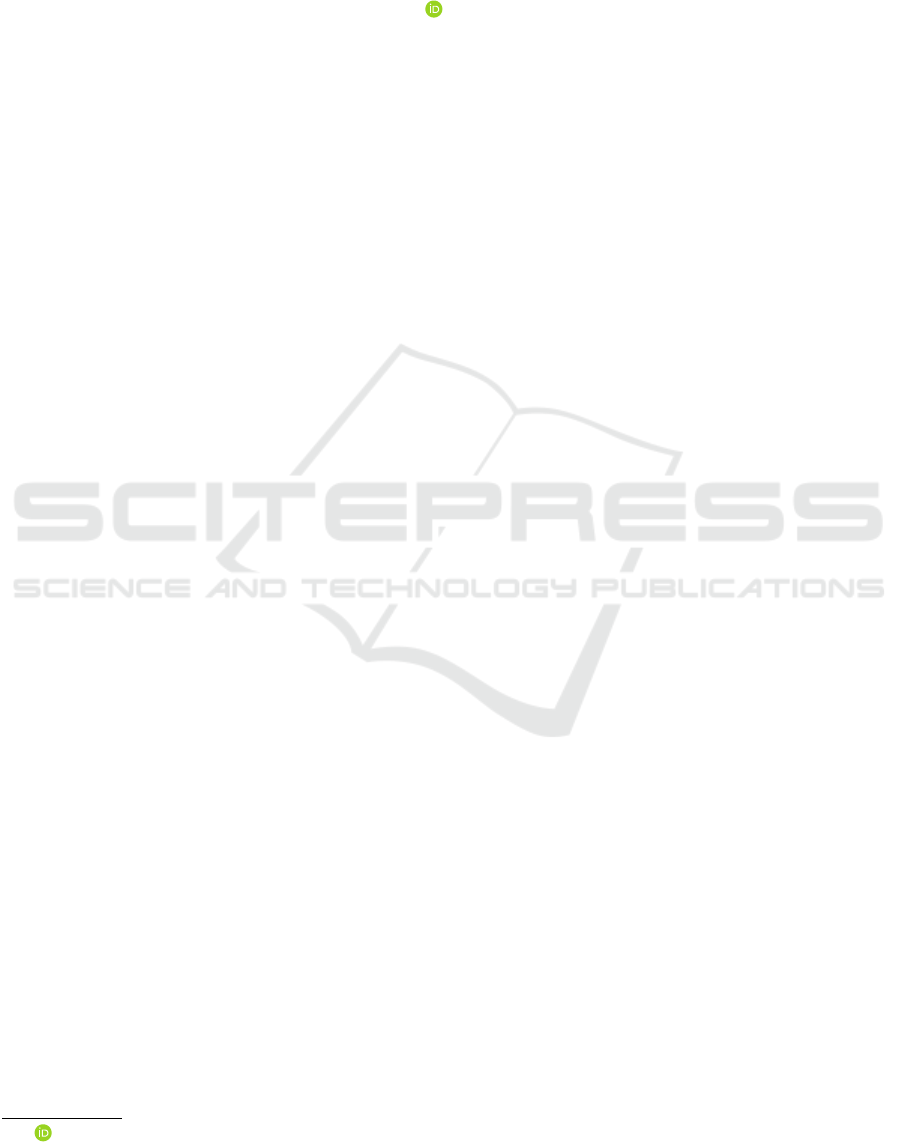
An Effective Method for Data Processing of Inertial Measurement Units
Applied to Embedded Systems
Christoph Kolhoff
a
and Markus Kemper
ZME-Institute, UAS Diepholz (PHWT), Th
¨
uringer Str. 3a, Diepholz, Germany
Keywords:
Bias Error, Gauss-Markov Process, MEMS Error Model.
Abstract:
Autonomous functions for navigation and localization have piqued the attention and interest in many fields of
science and engineering as automotive, aviation and robotics. Desiring high quantity of autonomous products,
the used components are requested to be cheap. This often lead engineers or developers to apply micro-
electromechanical systems that exhibit large errors. To use these sensors anyway, the acquired data must be
processed online for error reduction. Hence there is a need for an algorithm that is easy to compute. The
aim of this research is to develop a generic algorithm based on a Gauss-Markov process representing the
drifting bias that can be parametrized easily and performs well on real-time systems. Therefore, the error
model imitates the sensor’s output and removing the errors afterwards. Finally, a validation of the suggested
algorithm is performed by comparing processed data of the micro-controller to data processed a posteriori on
a high-performance computer.
1 INTRODUCTION
Autonomous functions are designed to make deci-
sions based on data acquired from sensors without any
human assistance. In foreseeable future autonomous
devices are purposed to take tasks in various sections
of daily life which requires a large large amount of
several accurate sensor data. The commonly used
sensors deliver those precise data but they lead to high
costs of the final product. For for low-cost robotic
systems on customer markets the used sensors are re-
quested to be cheap on the one hand and have to pro-
vide data with small errors on the other hand. Hence,
micro-electromechanical systems (MEMS) are the
point of interest in many cases. These kind of sen-
sors exhibit large tolerances and wide ranges of er-
rors as shown in (Kolhoff et al., 2021). In (Titterton
and Weston, 2004) an error model for triaxial IMUs is
given to describe the connectedness between the real
and the measured values. This model contains both,
repeatable (e.g. misalignment, scaling errors, static
bias) and non repeatable (e.g. noise) effects. Looking
at (Titterton and Weston, 2004), it is recommended
to compensate only repeatable errors by applying the
chosen error model. Processing stochastic effects is
not considered by this approach. Acquired data have
to be processed in ”real time” to improve their quality
a
https://orcid.org/0000-0002-7880-8152
and to reduce errors which leads to the need for suffi-
cient algorithms. Concerning automotive application,
inertial measurement units (IMUs) consisting of ac-
celerometers and gyroscopes are focused to determine
the relevant properties of the vehicle’s actual motion.
To take account of these requirements, the mathemat-
ical structure of the sensor’s behavior has to be known
to be able to develop an algorithm for data processing.
Therefore, an easy model containing misalignment,
constant and drifting bias, noise and nonlinear effects
in triads of sensors is given by (Kuncar et al., 2018).
Additionally, in (Gebre-Egziabher, 2004) some meth-
ods are presented to identify the needed parameters
easily. As a further important requirement, the model
is not just purposed to be parametrized for only one
specific sensor, but for an entire class of sensors. In
this paper the bias is the focused kind of error because
of its long-time drift characteristics.
In known applications the static component of the
bias is considered only and therefore the entire bias
cannot be compensated completely. Especially when
an integration over time is performed (e.g. by deter-
mining the orientation from the angular velocity), the
resulting errors rise very quickly with time as shown
in (Ramalingam et al., 2009). To design an algorithm
meeting these requirements, the drift of the sensor’s
bias is approximated by a first order Gauss-Markov
process (GM) for a single axis, referring to (Gebre-
558
Kolhoff, C. and Kemper, M.
An Effective Method for Data Processing of Inertial Measurement Units Applied to Embedded Systems.
DOI: 10.5220/0010540705580565
In Proceedings of the 18th International Conference on Informatics in Control, Automation and Robotics (ICINCO 2021), pages 558-565
ISBN: 978-989-758-522-7
Copyright
c
2021 by SCITEPRESS – Science and Technology Publications, Lda. All rights reserved