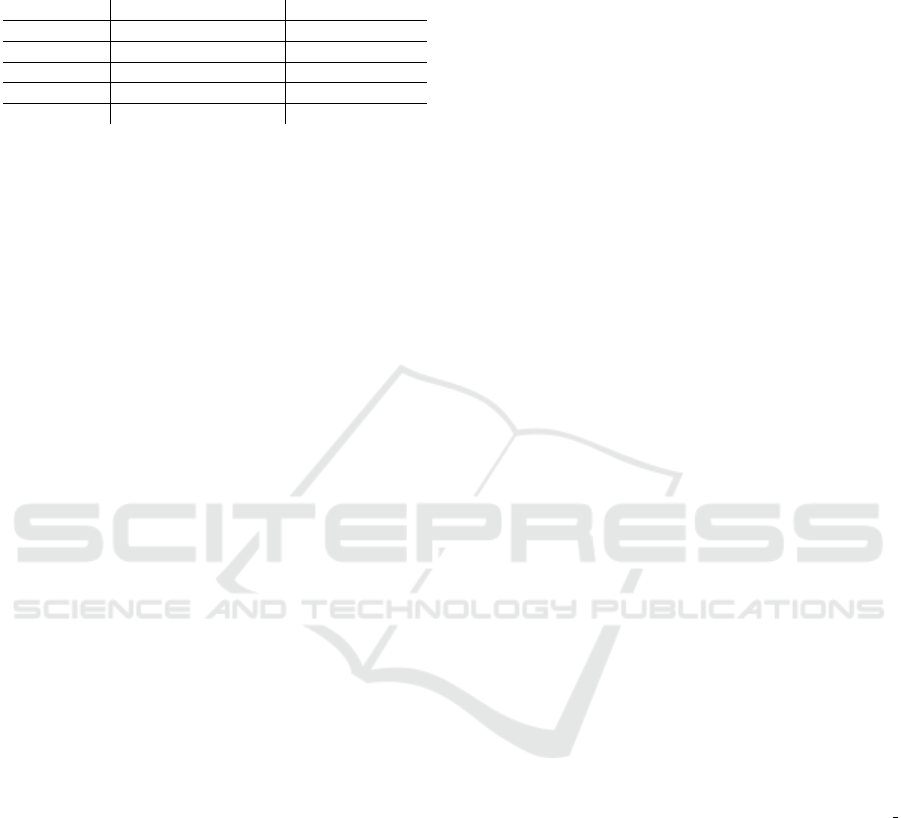
Table 1: Maximum, minimum, and median volumes and
aspect ratios (higher is better) of the meshes shown on the
left hand sides (before) and right hand sides (after) of Fig. 3
(hole fill) and Fig. 4 (erosion).
Volume Aspect Ratio
Edit Op. Max. Min. Med. Max. Min. Med.
Before Hole Fill 3.3e-10 1.4e-11 1.1e-10 .3333 .0803 .2737
After Hole Fill 2.4e-9 1.4e-11 1.1e-10 .3333 .0456 .2736
Before Erosion 1.6e-10 5.4e-12 4.9e-11 .3333 .0872 .2688
After Erosion 1.6e-10 1.0e-12 4.9e-11 .3333 .0004 .2689
tion with six iterations of subsequent quality preserv-
ing surface smoothing did not introduce inverted ele-
ments or infinitesimally small volume tetrahedra. The
resulting tetrahedra exhibit sufficient aspect ratios. As
a result, both mesh editing operations succeed at pro-
ducing meshes suitable for the FEM, as we have also
validated in our experiments.
5 CONCLUSIONS
In summary, we have introduced a novel tetrahedral
mesh editor with immediate simulation feedback. By
directly operating on CAE meshes, modifications can
be performed and simulated, while avoiding switch-
ing to a CAD tool and remeshing the entire domain.
As 3D printing can support and often only supports
discrete triangular surfaces, this approach avoids hav-
ing to feed back the results into a CAD tool com-
pletely. While the current set of editing operations
is somewhat limited, our prototype demonstrates how
the iterative product design loop can be shortened for
individualized versions of mass-produced parts.
The use of a GPU-accelerated FEA solver ensures
short iteration times, while the distributed architec-
ture minimizes user hardware requirements. Due to
the use of Unity (Unity, 2020) and WebSockets, the
front end can be deployed directly as a web applica-
tion. Bandwidth requirements are low due to the use
of surface meshes only between the front end and the
modeling service (the modeling and simulation ser-
vice should reside in the same data center, as they ex-
change volumetric meshes).
As the implemented editing operations preserve
the correspondence between individual boundary tri-
angles and their originating CAD surface IDs (or a
newly created contiguous surface ID), the user can in-
teract at a significantly higher level of abstraction than
individual surface triangles. Furthermore, this allows
automatic remapping of surface-based boundary con-
ditions for simulation. Additionally, mesh optimiza-
tion ensures mesh quality is preserved.
5.1 Future Work
Besides the extension to further editing operations, it-
eration times could be further reduced in the future by
performing geometry processing on the GPU, as done
by Mueller-Roemer et al. (Mueller-Roemer et al.,
2017). While our local, topological erosion works
well for the removal of fin- or plate-like structures,
the addition of geometric morphological operations,
such as the opening and closing operations on trian-
gle meshes recently shown by Sell
´
an et al. (Sell
´
an
et al., 2020), could greatly improve the flexibility of
the editor. Furthermore, hole filling could be extended
to non-planar holes by reparametrization of the loop
into 2D space and subsequent determination of inte-
rior point positions in 3D by solving a Laplacian.
REFERENCES
Alexa, M. (2019). Harmonic triangulations. ACM Transac-
tions on Graphics, 38(4):1–14.
Baraff, D. and Witkin, A. (1998). Large steps in cloth
simulation. In Proceedings of the 25th annual con-
ference on Computer graphics and interactive tech-
niques, SIGGRAPH ’98, pages 43–54.
Cheng, S.-W., Dey, T. K., and Shewchuk, J. (2012). Delau-
nay mesh generation. CRC Press.
D., J. (2018). Mini offers 3D printing person-
alization services for its cars. [Online; ac-
cessed Dec-2020]. https://www.3dnatives.com/en/
3d-printing-mini-100120184/.
Geuzaine, C. and Remacle, J.-F. (2009). Gmsh: A 3-d finite
element mesh generator with built-in pre- and post-
processing facilities. International Journal for Nu-
merical Methods in Engineering, 79(11):1309–1331.
Google (2020). Protocol buffers. [Online; ac-
cessed Dec-2020]. https://developers.google.com/
protocol-buffers/.
Inria (2019). Graphite. [Online; accessed Dec-
2020]. http://alice.loria.fr/index.php?option=com
content&view=article&id=22.
Klingner, B. M. and Shewchuk, J. R. (2008). Aggressive
tetrahedral mesh improvement. In Proceedings of the
16th International Meshing Roundtable, pages 3–23.
Koch, S., Matveev, A., Jiang, Z., Williams, F., Artemov, A.,
Burnaev, E., Alexa, M., Zorin, D., and Panozzo, D.
(2019). ABC: A big CAD model dataset for geomet-
ric deep learning. In 2019 IEEE/CVF Conference on
Computer Vision and Pattern Recognition.
Krispel, U., Settgast, V., and Fellner, D. W. (2018). Dy-
namo - dynamic 3d models for the web: A declara-
tive approach to dynamic and interactive 3d models
on the web using x3dom. In Proceedings of the 23rd
International ACM Conference on 3D Web Technol-
ogy, Web3D ’18, New York, NY, USA. Association
for Computing Machinery.
SIMULTECH 2021 - 11th International Conference on Simulation and Modeling Methodologies, Technologies and Applications
276