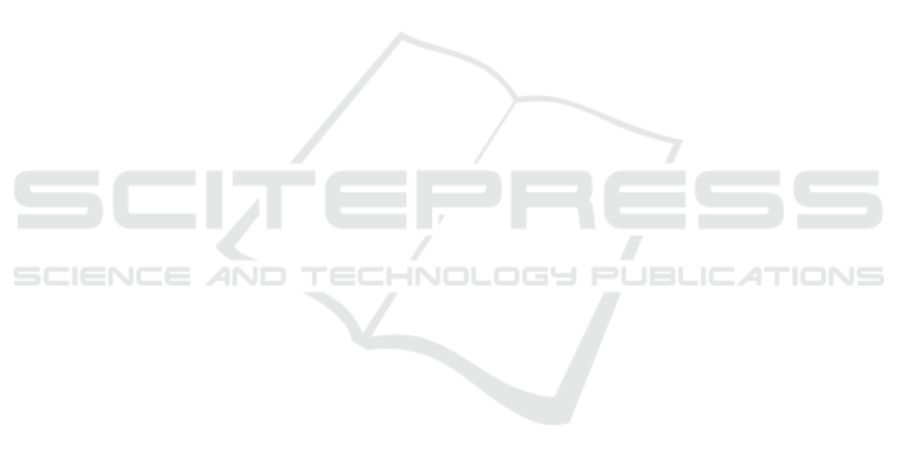
BB/R003971/1 for the University of Birmingham.
This work was partially supported by the Deutsche
Forschungsgemeinschaft (DFG, German Research
Foundation) under Germany’s Excellence Strategy –
EXC 2120/1 – 390831618.
REFERENCES
Adjigble, M., Marturi, N., Ortenzi, V., Rajasekaran, V.,
Corke, P., and Stolkin, R. (2018). Model-free
and learning-free grasping by local contact moment
matching. In Proceedings of the 2018 IEEE/RSJ In-
ternational Conference on Intelligent Robots and Sys-
tems (IROS), pages 2933–2940, Madrid, Spain.
Ajoudani, A., Zanchettin, A. M., Ivaldi, S., Albu-Sch
¨
affer,
A., Kosuge, K., and Khatib, O. (2017). Progress
and prospects of the human-robot collaboration. Au-
tonomous Robots.
Bekiroglu, Y., Marturi, N., Roa, M. A., Adjigble, K. J. M.,
Pardi, T., Grimm, C., Balasubramanian, R., Hang, K.,
and Stolkin, R. (2020). Benchmarking protocol for
grasp planning algorithms. IEEE Robotics and Au-
tomation Letters, 5(2):315–322.
Berceanu, C. and Tarnita, D. (2012). Mechanical design and
control issues of a dexterous robotic hand. Advanced
Materials Research, 463-464:1268–1271.
Bicchi, A. and Kumar, V. (2000). Robotic grasping and
contact: a review. In Proceedings of the IEEE In-
ternational Conference on Robotics and Automation
(ICRA), volume 1, pages 348–353.
Borst, C. and Indugula, A. (2005). Realistic virtual grasp-
ing. In Proceedings of the IEEE Conference on Virtual
Reality (VR), pages 91–320, Bonn, Germany.
Calli, B., Singh, A., Bruce, J., Walsman, A., Konolige, K.,
Srinivasa, S., Abbeel, P., and Dollar, A. M. (2017).
Yale-CMU-Berkeley dataset for robotic manipulation
research. The International Journal of Robotics Re-
search, 36(3):261–268.
Ding, D., Lee, Y.-H., and Wang, S. (2001). Computation
of 3-D form-closure grasps. IEEE Transactions on
Robotics and Automation, 17(4):515–522.
Dworkin, P. and Zeltzer, D. (1993). A new model for ef-
ficient dynamic simulation. In Proceedings of the
Fourth Eurographics Workshop on Animation and
Simulation, pages 135–147.
Ferrari, C. and Canny, J. (1992). Planning optimal grasps.
In Proceedings of the IEEE International Conference
on Robotics and Automation, volume 3, pages 2290–
2295.
Gualtieri, M., ten Pas, A., Saenko, K., and Platt, R. (2016).
High precision grasp pose detection in dense clutter.
In Proceedings of the IEEE/RSJ International Confer-
ence on Intelligent Robots and Systems (IROS), pages
598–605.
H
¨
oll, M., Oberweger, M., Arth, C., and Lepetit, V. (2018).
Efficient physics-based implementation for realistic
hand-object interaction in virtual reality. In Proceed-
ings of the IEEE Conference on Virtual Reality and
3D User Interfaces (VR), pages 175–182.
Honarpardaz, M., Tarkian, M.,
¨
Olvander, J., and Feng, X.
(2017). Finger design automation for industrial robot
grippers: A review. Robotics and Autonomous Sys-
tems, 87:104 – 119.
Levine, S., Pastor, P., Krizhevsky, A., Ibarz, J., and Quillen,
D. (2018). Learning hand-eye coordination for robotic
grasping with deep learning and large-scale data col-
lection. The International Journal of Robotics Re-
search, 37(4-5):421–436.
Miller, A. T. and Allen, P. K. (2004). GraspIt! a versa-
tile simulator for robotic grasping. IEEE Robotics Au-
tomation Magazine, 11(4):110–122.
Nguyen, V.-D. (1988). Constructing force- closure grasps.
The International Journal of Robotics Research,
7(3):3–16.
Nguyenle, T., Verdoja, F., Abu-Dakka, F., and Kyrki, V.
(2021). Probabilistic surface friction estimation based
on visual and haptic measurements. IEEE Robotics
and Automation Letters, pages 1–8.
Ortenzi, V., Cini, F., Pardi, T., Marturi, N., Stolkin, R.,
Corke, P., and Controzzi, M. (2020a). The grasp strat-
egy of a robot passer influences performance and qual-
ity of the robot-human object handover. Frontiers in
Robotics and AI, 7:138.
Ortenzi, V., Controzzi, M., Cini, F., Leitner, J., Bianchi, M.,
Roa, M. A., and Corke, P. (2019). Robotic manipula-
tion and the role of the task in the metric of success.
Nature Machine Intelligence, 1(8):340–346.
Ortenzi, V., Cosgun, A., Pardi, T., Chan, W., Croft, E., and
Kulic, D. (2020b). Object handovers: a review for
robotics. arXiv.
Osiurak, F., Rossetti, Y., and Badets, A. (2017). What is an
affordance? 40 years later. Neuroscience & Biobehav-
ioral Reviews, 77:403–417.
Talvas, A., Marchal, M., and L
´
ecuyer, A. (2013). The god-
finger method for improving 3d interaction with vir-
tual objects through simulation of contact area. In
Proceedings of the IEEE Symposium on 3D User In-
terfaces (3DUI), pages 111–114.
Vahrenkamp, N., Kr
¨
ohnert, M., Ulbrich, S., Asfour, T.,
Metta, G., Dillmann, R., and Sandini, G. (2012).
Simox: A robotics toolbox for simulation, motion and
grasp planning. In International Conference on Intel-
ligent Autonomous Systems (IAS), pages 585–594.
Zilles, C. B. and Salisbury, J. K. (1995). A constraint-based
god-object method for haptic display. In Proceedings
of the IEEE/RSJ International Conference on Intel-
ligent Robots and Systems (IROS), volume 3, pages
146–151.
ICINCO 2021 - 18th International Conference on Informatics in Control, Automation and Robotics
68