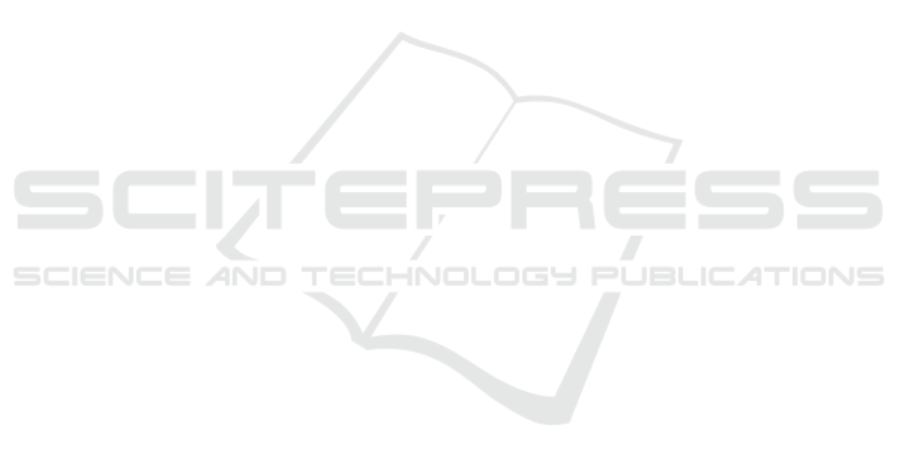
Dorigo, M. and St
¨
utzle, T. (2004). Ant Colony Optimiza-
tion. A Bradford Book, The MIT Press.
Elmenreich, W. and de Meer, H. (2008). Self-organizing
networked systems for technical applications: A dis-
cussion on open issues. In Proceedings of the 3rd
International Workshop on Self-Organizing Systems,
pages 1–9. Springer.
Elmenreich, W., D’Souza, R., Bettstetter, C., and de Meer,
H. (2009). A survey of models and design meth-
ods for self-organizing networked systems. In Self-
Organizing Systems, volume 5918 of LNCS, pages
37–49. Springer.
Elmenreich, W., Schnabl, A., and Schranz, M. (2021).
An artificial hormone-based algorithm for production
scheduling from the bottom-up. In Proceedings of the
13th International Conference on Agents and Artifi-
cial Intelligence. SciTePress.
Gao, K., Cao, Z., Zhang, L., Chen, Z., Han, Y., and
Pan, Q. (2019). A review on swarm intelligence and
evolutionary algorithms for solving flexible job shop
scheduling problems. IEEE/CAA Journal of Automat-
ica Sinica, 6(4):904–916.
Garey, M. R., Johnson, D. S., and Sethi, R. (1976).
The complexity of flowshop and jobshop scheduling.
Mathematics of Operations Research, 1(2):117–129.
Geng, H., editor (2018). Semiconductor Manufacturing
Handbook. McGraw-Hill Education.
Ghumare, M., Bewoor, L., and Sapkal, S. (2015). Appli-
cation of particle swarm optimization for production
scheduling. In Proc. of the International Conference
on Computing Communication Control and Automa-
tion, pages 485–489. IEEE.
Hamann, H., Stradner, J., Schmickl, T., and Crailsheim,
K. (2010). Artificial hormone reaction networks:
Towards higher evolvability in evolutionary multi-
modular robotics. In Proceedings of the Artificial Life
XII, pages 773–780.
Hassanien, A. E. and Emary, E. (2018). Swarm Intelligence:
Principles, Advances, and Applications. CRC Press.
Heylighen, F. (2001). The science of self-organization and
adaptivity. The Encyclopedia of Life Support Systems,
5(3):253–280.
Lawler, E. L., Lenstra, J. K., Kan, A. H. R., and Shmoys,
D. B. (1993). Sequencing and scheduling: Algorithms
and complexity. Handbooks in Operations Research
and Management Science, 4:445–522.
Lawler, E. L., Lenstra, J. K., Rinnooy-Kan, A. H. G., and
Shmoys, D. B., editors (1985). The Traveling Sales-
man Problem: A Guided Tour of Combinatorial Opti-
mization. JohnWiley & Sons.
Li, X. and Gao, L. (2016). An effective hybrid genetic algo-
rithm and tabu search for flexible job shop scheduling
problem. International Journal of Production Eco-
nomics, 174:93–110.
Pacino, D. and Van Hentenryck, P. (2011). Large neigh-
borhood search and adaptive randomized decomposi-
tions for flexible jobshop scheduling. In Proc. of the
22nd International Joint Conference on Artificial In-
telligence, pages 1997–2002.
Renteln, A. V., Brinkschulte, U., and Weiss, M. (2008). Ex-
aminating task distribution by an artificial hormone
system based middleware. In Proc. of the 11th IEEE
International Symposium on Object and Component-
Oriented Real-Time Distributed Computing, pages
119–123.
Schranz, M., Bagnato, A., Brosse, E., and Elmenreich, W.
(2018). Modelling a CPS swarm system: A simple
case study. In Proc. of the 6th International Confer-
ence on Model-Driven Engineering and Software De-
velopment, pages 615–624.
Schranz, M., Umlauft, M., Sende, M., and Elmenreich, W.
(2020). Swarm robotic behaviors and current applica-
tions. Frontiers in Robotics and AI, 7:36.
Sharma, T. K. and Pant, M. (2017). Shuffled artificial
bee colony algorithm. Soft Computing, 21(20):6085–
6104.
Shen, W. M., Chuong, C. M., and Will, P. (2002). Digital
hormone models for self-organization. In Proceedings
of the 8th International Conference on Artificial Life,
pages 116–120.
Sinha, S. and Chaczko, Z. (2017). Concepts and observa-
tions in artificial endocrine systems for iot infrastruc-
ture. In Proceedings of the 25th International Confer-
ence on Systems Engineering, pages 427–430.
Sobe, A., Elmenreich, W., Szkaliczki, T., and B
¨
osz
¨
ormenyi,
L. (2015). SEAHORSE: Generalizing an artificial hor-
mone system algorithm to a middleware for search and
delivery of information units. Computer Networks,
80:124–142.
Sobe, A., Feh
´
erv
´
ari, I., and Elmenreich, W. (2012).
FREVO: A tool for evolving and evaluating self-
organizing systems. In Proceedings of the 1st Interna-
tional Workshop on Evaluation for Self-Adaptive and
Self-Organizing Systems.
Stidham Jr, S. (2002). Analysis, design, and control of
queueing systems. Operations Research, 50(1):197–
216.
van Ast, J., Babuska, R., and De Schutter, B. (2008). A gen-
eral modeling framework for swarms. In Proceedings
of the IEEE Congress on Evolutionary Computation,
pages 3795–3800.
Wilensky, U. and Rand, W. (2015). An Introduction to
Agent-Based Modeling: Modeling Natural, Social,
and Engineered Complex Systems with NetLogo. MIT
Press.
Wilson, J., Timmis, J., and Tyrrell, A. (2019). An amal-
gamation of hormone inspired arbitration systems for
application in robot swarms. Applied Sciences, 9(17).
Yuan, Y. and Xu, H. (2013). Flexible job shop scheduling
using hybrid differential evolution algorithms. Com-
puters & Industrial Engineering, 65(2):246–260.
Zhang, G., Shao, X., Li, P., and Gao, L. (2009). An effec-
tive hybrid particle swarm optimization algorithm for
multi-objective flexible job-shop scheduling problem.
Computers & Industrial Engineering, 56(4):1309–
1318.
SIMULTECH 2021 - 11th International Conference on Simulation and Modeling Methodologies, Technologies and Applications
334