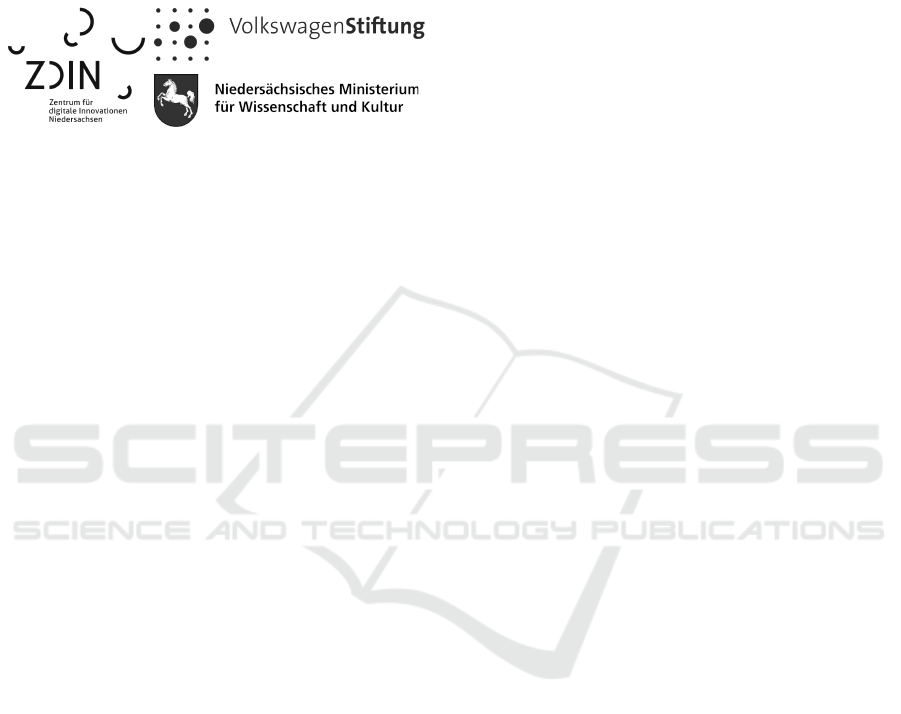
ACKNOWLEDGEMENTS
Funded by the Lower Saxony Ministry of Science
and Culture under grant number ZN3495 within the
Lower Saxony ”Vorab” of the Volkswagen Founda-
tion and supported by the Center for Digital Innova-
tions (ZDIN).
REFERENCES
Aeberhard, M., Rauch, S., Bahram, M., Tanzmeister, G.,
Thomas, J., Pilat, Y., Homm, F., Huber, W., and
Kaempchen, N. (2015). Experience, Results and
Lessons Learned from Automated Driving on Ger-
many’s Highways. IEEE Intelligent Transportation
Systems Magazine, 7(1):42–57.
Alshareef, A. and Sarjoughian, H. S. (2018). Model-driven
time-accurate DEVS-based approaches for CPS de-
sign. In Model-driven Approaches for Simulation En-
gineering. Society for Modeling and Simulation Inter-
national.
Conrad, M., Sadeghipour, S., and Wiesbrock, H.-W. (2005).
Automatic Evaluation of ECU Software Tests. In SAE
Technical Paper Series, volume 2005-01-1659, War-
rendale, PA, United States. SAE International.
Garousi, V. and Elberzhager, F. (2017). Test Automation:
Not Just for Test Execution. IEEE Software, 34(2):90–
96.
G
¨
ollner, M. and Tao, H. (2018). Simulator develop-
ment. Automotive Testing Technology International,
September 2018:102–106.
Hanselmann, H. (1996). Automotive control: from con-
cept to experiment to product. In Proceedings of the
Joint Conference on Control Applications Intelligent
Control and Computer Aided Control System Design,
pages 129–134.
Inkermann, D., Huth, T., Vietor, T., Grewe, A., Knieke,
C., and Rausch, A. (2019). Model-Based Require-
ment Engineering to Support Development of Com-
plex Systems. Procedia CIRP, 84:239–244.
ISO (2018). Road vehicles - Functional safety. Number ISO
26262:2018. Beuth Verlag GmbH, Berlin, Germany.
ISO (2019). Road vehicles: Safety of the intended func-
tionality. Number ISO/PAS 21448:2019. Beuth Ver-
lag GmbH, Berlin, Germany.
Jacobitz, S. and Liu-Henke, X. (2019). A Real-Time
Interface for Xcos – Demonstrated on a Battery-
management System. In Proceedings of the 2nd Scilab
Conference.
Jacobitz, S. and Liu-Henke, X. (2020). The Seamless
Low-cost Development Platform LoRra for Model
based Systems Engineering. In Proceedings of the
8th International Conference on Model-Driven En-
gineering and Software Development, pages 57–64.
SCITEPRESS.
Kumar, A., Boehm, M., and Yang, J. (2017). Data Man-
agement in Machine Learning. In Proceedings of
the 2017 ACM International Conference on Manage-
ment of Data, pages 1717–1722, New York, NY, USA.
ACM.
Lemon, K. (2003). Introduction to the Universal Measure-
ment and Calibration Protocol XCP. In SAE Technical
Paper Series, Warrendale, PA, United States. SAE In-
ternational.
Liu-Henke, X., Feind, R., Roch, M., and Quantmeyer,
F. (2014). Investigation of low-cost open-source
platforms for developing of mechatronic functions
with rapid control prototyping. In 10th International
Conference on Mechatronic Systems and Materials,
Opole, Polen.
Liu-Henke, X., Gollner, M., Jacobitz, S., Scherler, S.,
Zhang, J., and Yarom, O. A. (2020a). Driving-
Simulator-in-the-Loop — Virtual Function Design
with Consideration of Human Behaviour. In IEEE In-
ternational Symposium on Systems Engineering.
Liu-Henke, X., Jacobitz, S., Gollner, M., Zhang, J., Scher-
ler, S., and Yarom, O. A. (2020b). Cyber-physical
Industry 4.0 laboratory test field to simulate self-
optimizing intralogistics. In 19th International Con-
ference on Mechatronics.
Liu-Henke, X., L
¨
uckel, J., and J
¨
aker, K.-P. (2002). An ac-
tive suspension/tilt system for a mechatronic railway
carriage. Journal of IFAC - Control Engineering Prac-
tice, 10(9):991–998.
Liu-Henke, X., Scherler, S., Fritsch, M., and Quantmeyer,
F. (2016). Holistic development of a full-active elec-
tric vehicle by means of a model-based systems engi-
neering. In IEEE International Symposium on Systems
Engineering.
L
¨
uckel, J., Hestermeyer, T., and Liu-Henke, X. (2001).
Generalization of the cascade principle in view of
a structured form of mechatronic systems. In
IEEE/ASME International Conference on Advanced
Intelligent Mechatronics, pages 123–128.
Maldonado, L., Chang, W., Roy, D., Annaswamy, A.,
Goswami, D., and Chakraborty, S. (2019). Exploiting
System Dynamics for Resource-Efficient Automotive
CPS Design. In Design, Automation & Test in Europe
Conference & Exhibition, pages 234–239.
Matt, D., Modrak, V., and Zsifkovits, H. E. (2020). Industry
4.0 for SMEs: Challenges, opportunities and require-
ments. Springer International Publishing, Cham.
Montavon, G., Samek, W., and M
¨
uller, K.-R. (2018). Meth-
ods for interpreting and understanding deep neural
networks. Digital Signal Processing, 73:1–15.
Scherler, S., Liu-Henke, X., and Henke, M. (2020). Pre-
dictive Energy Management for an Electric Vehicle
with Fuel Cell Range Extender in Connected Traffic
Systems. In 19th International Conference on Mecha-
tronics - Mechatronika. IEEE.
ICSOFT 2021 - 16th International Conference on Software Technologies
222