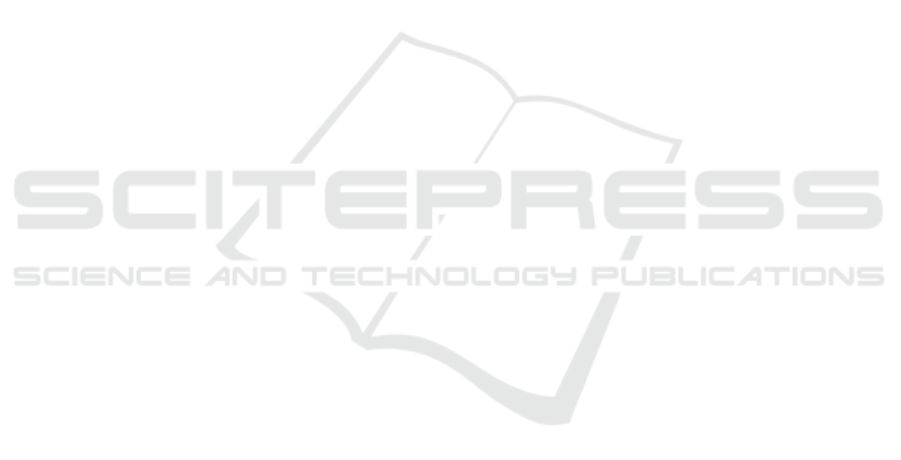
computing infrastructure has to be manually deployed
in advance. The automation of these tasks would give
to Evoker the robustness for being widely adopted in
many fields.
Finally, since Evoker relies on OpenFOAM and
their communications are already ready, the next step
would be to make Evoker provide CFD simulation
capabilities.
ACKNOWLEDGEMENTS
Researcher S. Iserte was supported by the
postdoctoral fellowship APOSTD/2020/026 from the
Valencian Government Region and European Social
Funds.
REFERENCES
Ayachit, U. (2015). The ParaView Guide: A Parallel
Visualization Application. Kitware, Inc., Clifton Park,
NY, USA.
Azure (2021a). Eds v4 Series. https://azure.microsoft.
com/en-us/pricing/details/virtual-machines/linux/
#edv4-series. [Online; accessed 22-March-2021].
Azure (2021b). Storage Files. https://azure.microsoft.com/
en-us/pricing/details/storage/files/. [Online; accessed
22-March-2021].
Climent, J., Basiero, L., Mart
´
ınez-Cuenca, R., Berlanga,
J. G., Juli
´
an-L
´
opez, B., and Chiva, S. (2018).
Biological reactor retrofitting using CFD-ASM
modelling. Chemical Engineering Journal, 348.
Climent, J., Mart
´
ınez-Cuenca, R., Berlanga, J. G., and
Chiva, S. (2019). Hydrosludge 3D: herramienta
para el dise
˜
no de nuevas EDAR mediante simulaci
´
on
computacional de fluidos (CFD). In XXXV
Jornadas T
´
ecnicas de AEAS. Asociaci
´
on Espa
˜
nola de
Abastecimientos de Agua y Saneamiento.
Geuzaine, C. and Remacle, J. F. (2009). Gmsh: A
3-D finite element mesh generator with built-in
pre- and post-processing facilities. International
Journal for Numerical Methods in Engineering,
79(11):1309–1331.
Glover, G. C., Printemps, C., Essemiani, K., and Meinhold,
J. (2006). Modelling of wastewater treatment plants
- How far shall we go with sophisticated modelling
tools? Water Science and Technology, 53(3):79–89.
Jayakumar, J., Mahajani, S., Mandal, J., Vijayan, P.,
and Bhoi, R. (2008). Experimental and cfd
estimation of heat transfer in helically coiled heat
exchangers. Chemical Engineering Research and
Design, 86(3):221–232.
Li, Y., Paik, K.-J., Xing, T., and Carrica, P. M. (2012).
Dynamic overset cfd simulations of wind turbine
aerodynamics. Renewable Energy, 37(1):285–298.
MPI-Forum (1994). MPI: A Message-Passing Interface
Standard. Technical report, USA.
Norton, D. and Vlachos, D. (2003). Combustion
characteristics and flame stability at the microscale:
a cfd study of premixed methane/air mixtures.
Chemical Engineering Science, 58(21):4871–4882.
International Symposium on Mathematics in
Chemical Kinetics and Engineering.
Schroeder, Willand Martin, K. and Lorensen, B. (2006).
The Visualization Toolkit (4th ed.). Kitware, Inc.,
Clifton Park, NY, USA.
Taylor, S. J., Anagnostou, A., Kiss, T., Terstyanszky, G.,
Kacsuk, P., Fantini, N., Lakehal, D., and Costes, J.
(2018). Enabling Cloud-Based Computational Fluid
Dynamics with a Platform-As-A-Service Solution.
IEEE Transactions on Industrial Informatics,
15(1):85–94.
Weller, H. G., Tabor, G., Jasak, H., and Fureby, C. (1998).
A tensorial approach to computational continuum
mechanics using object-oriented techniques.
Computers in Physics, 12(6):620.
W
¨
ustenhagen, C., John, K., Langner, S., Brede, M.,
Grundmann, S., and Bruschewski, M. (2021). Cfd
validation using in-vitro mri velocity data – methods
for data matching and cfd error quantification.
Computers in Biology and Medicine, 131:104230.
Zajaczkowski, F. J., Haupt, S. E., and Schmehl, K. J.
(2011). A preliminary study of assimilating numerical
weather prediction data into computational fluid
dynamics models for wind prediction. Journal
of Wind Engineering and Industrial Aerodynamics,
99(4):320–329. The Fifth International Symposium
on Computational Wind Engineering.
A Distributed Mesh Generation Study Case through a Customizable Platform as a Service Framework
421