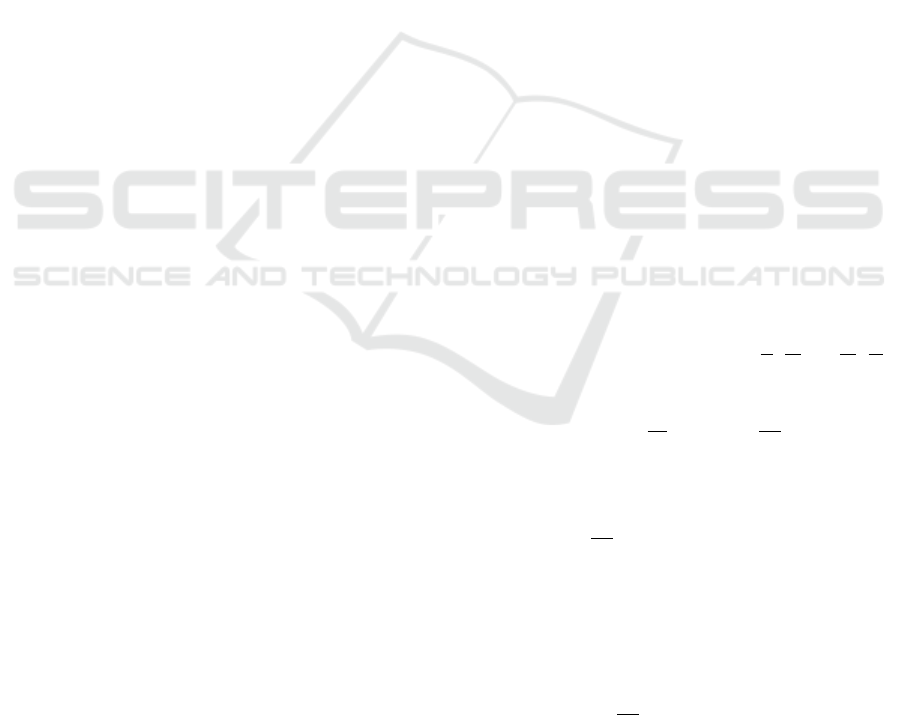
Boyer, F., Lebastard, V., Candelier, F., and Renda, F. (2020).
Dynamics of continuum and soft robots: a strain
parametrization based approach. IEEE Transactions
on Robotics.
Boyer, F., Porez, M., and Leroyer, A. (2010). Poincar
´
e-
cosserat equations for the lighthill three-dimensional
large amplitude elongated body theory: Application
to robotics. 20(1):47–79.
Caasenbrood, B. (2020). Sorotoki - an open-
source soft robotics toolkit for matlab.
https://github.com/BJCaasenbrood/SorotokiCode.
Chirikjian, G. and Burdick, J. (1992). Kinematically
optimal hyper-redundant manipulator configurations.
Proceedings 1992 IEEE International Conference on
Robotics and Automation.
Choi, W., Whitesides, G. M., Wang, M., Chen, X., Shep-
herd, R. F., Mazzeo, A. D., Morin, S. A., Stokes,
A. A., and Ilievski, F. (2011). Multigait soft robot.
Proceedings of the National Academy of Sciences,
108(51):20400–20403.
Della Santina, C. and Rus, D. (2020). Control oriented mod-
eling of soft robots: The polynomial curvature case.
IEEE Robotics and Automation Letters, 5(2):290–298.
Duriez, C. (2013). Control of elastic soft robots based on
real-time finite element method. Proceedings - IEEE
International Conference on Robotics and Automa-
tion, pages 3982–3987.
Falkenhahn, V., Mahl, T., Hildebrandt, A., Neumann,
R., and Sawodny, O. (2015). Dynamic Modeling
of Bellows-Actuated Continuum Robots Using the
Euler-Lagrange Formalism. IEEE Transactions on
Robotics, 31(6):1483–1496.
Franco, E. and Garriga-Casanovas, A. (2020). Energy-
shaping control of soft continuum manipulators with
in-plane disturbances. International Journal of
Robotics Research.
Katzschmann, R. K., Della Santina, C. D., Toshimitsu, Y.,
Bicchi, A., and Rus, D. (2019). Dynamic motion
control of multi-segment soft robots using piecewise
constant curvature matched with an augmented rigid
body model. RoboSoft 2019 - 2019 IEEE Interna-
tional Conference on Soft Robotics, (February):454–
461.
Kriegman, S., Blackiston, D., Levin, M., and Bongard, J.
(2019). A scalable pipeline for designing reconfig-
urable organisms.
Marchese, A. D., Onal, C. D., and Rus, D. (2014). Au-
tonomous Soft Robotic Fish Capable of Escape Ma-
neuvers Using Fluidic Elastomer Actuators. Soft
Robotics, 1(1):75–87.
Murray, R. M., Sastry, S. S., and Zexiang, L. (1994). A
Mathematical Introduction to Robotic Manipulation.
CRC Press, Inc., USA, 1st edition.
Ortega, R., Spong, M. W., G
´
omez-Estern, F., and Blanken-
stein, G. (2002). Stabilization of a Class of Under-
actuated MechanicalSystems Via Interconnection and
DampingAssignment. IEEE Transactions on Auto-
matic Control, 47(8):1218–1233.
Renda, F., Armanini, C., Lebastard, V., Candelier, F., and
Boyer, F. (2020). A Geometric Variable-Strain Ap-
proach for Static Modeling of Soft Manipulators with
Tendon and Fluidic Actuation. IEEE Robotics and Au-
tomation Letters, 5(3):4006–4013.
Schaft, A. J. (2004). Port-Hamiltonian Systems: Network
Modeling and Control of Nonlinear Physical Systems.
Advanced Dynamics and Control of Structures and
Machines, pages 127–167.
Simo, J. C. and Vu-Quoc, L. (1986). A three-dimensional
finite-strain rod model. part II: Computational aspects.
Computer Methods in Applied Mechanics and Engi-
neering, 58(1):79–116.
Spong, M. W., Hutchinson, S., and Vidyasagar, M. (2006).
Robot modeling and control. John Wiley & Sons, New
York.
Thuruthel, T., Falotico, E., Renda, F., and Laschi, C. (2018).
Model-based reinforcement learning for closed-loop
dynamic control of soft robotic manipulators. IEEE
Transactions on Robotics, PP:1–11.
Till, J., Aloi, V., and Rucker, C. (2019). Real-Time Dynam-
ics of Soft and Continuum Robots based on Cosserat-
Rod Real-Time Dynamics of Soft and Continuum
Robots based on Cosserat-Rod Models. (May).
Zhang, Z., Morales Bieze, T., Dequidt, J., Kruszewski, A.,
and Duriez, C. (2017). Visual Servoing Control of
Soft Robots based on Finite Element Model. In IROS
2017 - IEEE/RSJ International Conference on Intelli-
gent Robots and Systems, Vancouver, Canada.
APPENDIX
A. Deriving the Continuous Kinematics
Under Assumption 1, the configuration space of the
soft robot g is everywhere differentiable. Then, using
the equality of mixed partials, i.e.
∂
∂t
(
∂g
∂σ
) =
∂
∂σ
(
∂g
∂t
),
we substitute ∂g/∂t = g
ˆ
η and ∂g/∂σ = g
ˆ
ξ to find
g
ˆ
η
ˆ
ξ + g
∂
ˆ
ξ
∂t
= g
ˆ
ξ
ˆ
η + g
∂
ˆ
η
∂σ
. (36)
Pre-multiplying with g
−1
∈ SE(3) and rearranging the
equality above, we obtain
∂
ˆ
η
∂σ
= −
ˆ
ξ
ˆ
η −
ˆ
η
ˆ
ξ
+
˙
ˆ
ξ, (37)
where we can recognize the Lie bracket or the com-
muter between the vector fields ξ and η (Murray et al.,
1994). Since the Lie bracket [
ˆ
ξ,
ˆ
η] itself also belongs
to se(3), which is isomorphic to R
6
via
ˆ
η 7→ η, we
can rewrite the expressions as follows
∂η
∂σ
= −ad
ξ
η +
˙
ξ, (38)
where ad
(·)
: R
6
7→ R
6×6
defines the adjoint action
map on the Lie algebra se(3). This kinematic relation
is analogous to (Boyer et al., 2020; Renda et al., 2020;
Till et al., 2019)
ICINCO 2021 - 18th International Conference on Informatics in Control, Automation and Robotics
318