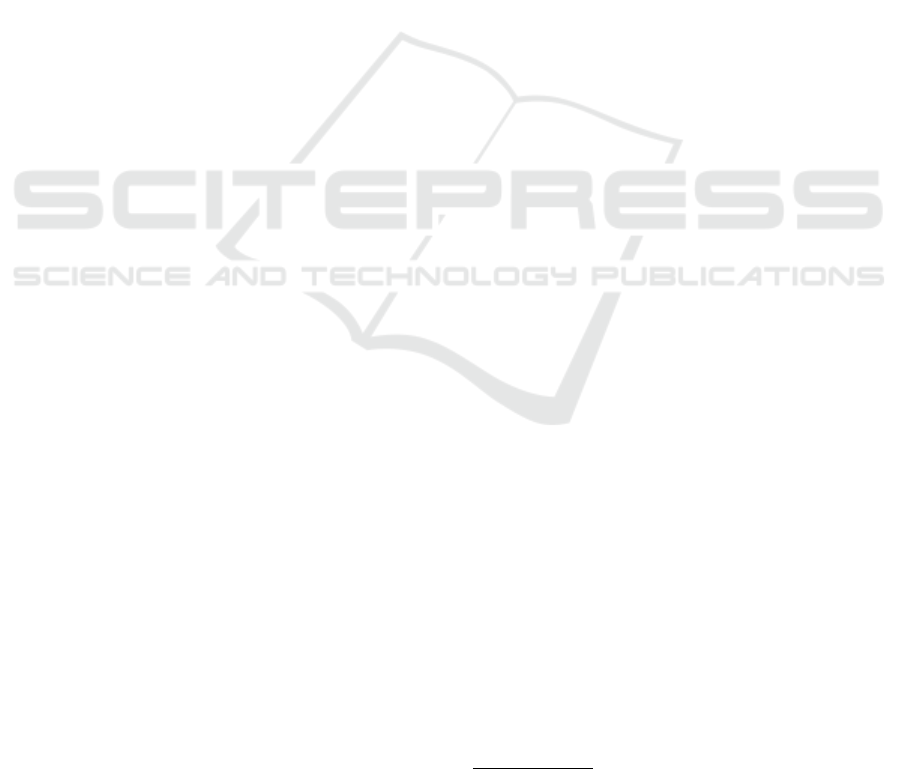
2 RELATED WORK
2.1 Bulky Waste Sorting Pilot Study
In a pilot study conducted in 2011 (the R&D project
”Efficient Sorting of Bulk Wastes with Robots”
(ROSA, 2011)), a system concept for the automatic
sorting of bulky wastes was developed. The project
evaluated the feasibility of technical solutions for
the automated removal of non-recyclable items from
large piles of bulky wastes entering the recycling
plant. It also looked at options for the automatic ex-
traction of larger items of recyclable material during
the final sorting on the conveyor belt. The focus of the
project was on the evaluation of sensors and methods
for 2D and 3D object recognition. The lack of consis-
tent form features of the often deformed and damaged
objects as well as the highly heterogeneous composi-
tion of the waste conglomerate were identified as the
key challenges for both object recognition and object
manipulation.
In support of a theoretical study, lab experiments
were conducted to recognize and subsequently ma-
nipulate objects within the waste conglomerate us-
ing data fusion of different sensors (e.g., cameras, 3D
laser scanners, NIR sensors) and standard robotic ma-
nipulators (e.g., KUKA). The lab demonstrator was
able to prove the basic feasibility of the ROSA con-
cept. However, it was not possible to adapt and test
the concept under actual working conditions due to
the lack of financial resources and available state-of-
the-art equipment at the time.
Nevertheless, the outcome of the ROSA project
provides a valuable starting point for more recent ef-
forts to implement a SmartRecycling concept. As
described in this paper, new developments in AI-
based object recognition, sensor fusion and mobile
robotics are the key to solving some of the fundamen-
tal problems with the automated extraction of large
waste objects from a heterogeneous waste conglom-
erate ROSA had identified at the time.
2.2 Automation of Large Hydraulic
Machines
Standard industrial robots as well as most profes-
sional service robots developed for indoor and field
applications use electric actuators to grip, hold, and
move objects. In these electric-powered systems,
several integrated sensors continuously monitor the
system-state and thus deliver the information needed
to automate the control of manipulators, grippers and
other sub-systems.
On the other hand, hydraulic-powered machines,
such as cranes and excavators, are more challeng-
ing to automate, since they are typically not equipped
with the necessary sensors and hydraulic actuators of-
ten lack the precision of their electric counterparts.
Despite these shortcomings, large hydraulic-
powered machines are prevalent in many industries
such as construction, mining, waste sorting, agricul-
ture and forestry, etc. Due to their high performance,
robustness, and reliability, they are used in harsh en-
vironments and rugged terrain. Also, the deployment
of automated hydraulic heavy machinery in construc-
tion, mining, and agriculture is increasing. There
already exist several automated hydraulic machines,
either as commercial products or as research proto-
types.
In project ROBDEKON (K
¨
uhn et al., 2020), DFKI
is part of a consortium that develops solutions for
the automation of large hydraulic machines. By
retrofitting a M545 excavator, build by the Swiss com-
pany Menzi Muck, with sensors and modified actu-
ators, DFKI developed the hydraulic robot ARTER
(Automated Rough Terrain Excavator Robot)
1
With ARTER, ROBDEKON could prove that a
large hydraulic excavator can be automated to suc-
cessfully handle complex tasks, like manipulating
barrels filled with hazardous waste, if equipped with
sensors that can measure the state and pose of joints,
limbs and the like. However, the project also showed
that this retrofitting does come at a high cost, limiting
the applicability of the concept for many legacy sys-
tems. Also, since the robot has to operate in a very un-
structured and highly dynamic environment, conven-
tional methods for robot control that cannot react to
changes in the environment are only of limited value.
2.3 Sensor Data Processing in
Construction Waste Analysis
In different projects, the classification of waste ob-
jects based on RGB images was studied. Kim et al.
(2019) use a modified LeNet 5 convolutional neural
network (CNN) to classify objects by RGB images in
carton vs. plastic (Kim et al., 2019). Also, some more
applications of neural networks to classify waste ob-
jects based on visual image data are presented by Kim
et al. (2019). Such an RGB-image-based classifica-
tion seems to be feasible once objects can be iden-
tified within images. In an extreme case, this could
be accomplished by scanning a barcode of an ob-
ject (e.g., when supporting people sorting their waste
1
https://robotik.dfki-bremen.de/en/research/robot-
systems/arter/
ICINCO 2021 - 18th International Conference on Informatics in Control, Automation and Robotics
494