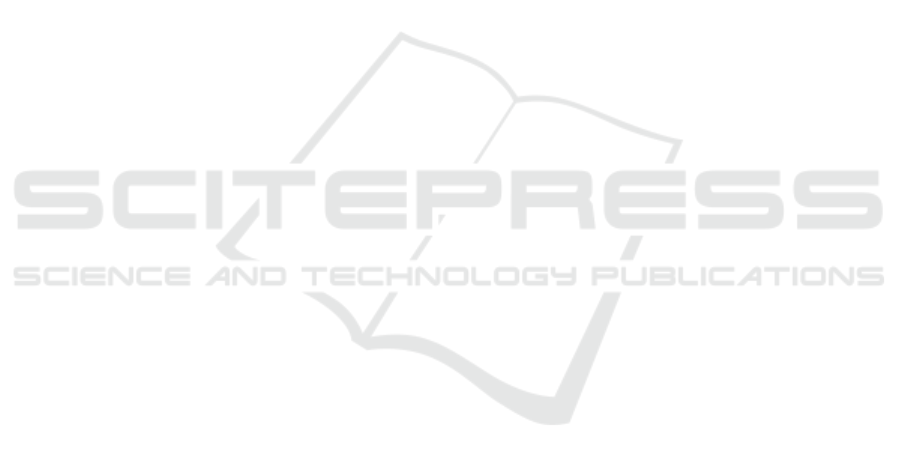
techniques in computer graphics. In Computer Graph-
ics Forum, volume 30, pages 43–60.
Dupuy, J. and Bruneton, E. (2012). Real-time animation and
rendering of ocean whitecaps. In SIGGRAPH Asia,
Technical Briefs, page Article No.15.
Foster, N. and Fedkiw, R. (2001). Practical animation of
liquids. In ACM SIGGRAPH, pages 23–30.
Geiger, W., Leo, M., Rasmussen, N., Losasso, F., and Fed-
kiw, R. (2006). So real it’ll make you wet. In ACM
SIGGRAPH Sketches, page Article No.20.
Goktekin, T., Bargteil, A., and O’Brien, J. (2004). A
method for animating viscoelastic fluids. ACM Trans-
actions on Graphics, 23(3):463–468.
Greenwood, S. and House, D. (2004). Better with bubbles:
Enhancing the visual realism of simulated fluid. In
ACM SIGGRAPH/Eurographics symposium on com-
puter animation, pages 287–296.
Hinsinger, D., Neyret, F., and Cani, M. (2002). Inter-
active animation of ocean waves. In ACM SIG-
GRAPH/Eurographics symposium on computer ani-
mation, pages 116–166.
Hong, J., Lee, H., Yoon, J., and Kim, C. (2008). Bubbles
alive. ACM Transactions on Graphics, 27(3):48:1–
48:8.
Iglesias, A. (2004). Computer graphics for water modeling
and rendering: A survey. Future Generation Com-
puter Systems, 20(8):1355–1374.
Iribe, T. and Nakaza, E. (2011). An improvement of accu-
racy of the mps method with a new gradient calcula-
tion model (in japanese). Journal of the Japan Society
of Civil Engineers(B2), 67(1):36–48.
Kim, B., Liu, Y., Llamas, I., Jiao, X., and Rossignac, J.
(2007). Simulation of bubbles in foam with the vol-
ume control method. ACM Transactions on Graphics,
26(3):98:1–98:10.
Kipfer, P. and Westermann, R. (2006). Realistic and interac-
tive simulation of rivers. In Graphics Interface, pages
41–48.
Koshizuka, S. and Oka, Y. (1996). Moving-particle semi-
implicit method for fragmentation of incompressible
fluid. Nuclear Science and Engineering, 123:421–
434.
Losasso, F., Talton, J., Kwatra, N., and Fedkiw, R. (2008).
Two-way coupled sph and particle level set fluid simu-
lation. IEEE Transsactions on Visualization and Com-
puter Graphics, 14(4):797–804.
Miller, G. (1989). Globular dynamics: A connected parti-
cle system for animating viscous fluids. Computers &
Graphics, 13(3):305–309.
Monaghan, J. (2000). SPH without a tensile instability.
Journal of Computational Physics, 159(2):290–311.
Mould, D. and Yang, Y. (1997). Modeling water for com-
puter graphics. Computers & Graphics, 21(6):801–
814.
M
¨
uller, M., Charypsr, D., and Gross, M. (2003). Particle-
based fluid simulation for interactive applications. In
ACM SIGGRAPH/Eurographics symposium on com-
puter animation, pages 154–159.
Mukai, N., Ito, K., Nakagawa, M., and Kosugi, M. (2010).
Spinnability simulation of viscoelastic fluid. In ACM
SIGGRAPH Posters, page Article No.18.
Mukai, N., Matsui, E., and Chang, Y. (2019). Investigation
on viscoelastic fluid behavior by modifying deviatoric
stress tensor. In SIMULTECH, pages 216–222.
Mukai, N., Nishikawa, T., and Chang, Y. (2018). Evaluation
of stretched thread lengths in spinnability. In ACM
SIGGRAPH Posters, page Article No.62.
Nishino, T., Iwasaki, K., Dobashi, Y., and Nishita, T.
(2012). Visual simulation of freezing ice with air bub-
bles. In SIGGRAPH Asia, Technical Briefs, page Ar-
ticle No.1.
Ram, D., Gast, T., Jiang, C., Schroeder, C., Sromakhin, A.,
Teran, J., and Kavehpour, P. (2015). A material point
method for viscoelastic fluids, foams and sponges. In
ACM SIGGRAPH/Eurographics symposium on com-
puter animation, pages 157–163.
Sims, K. (1990). Particle animation and rendering using
data parallel computation. In ACM SIGGRAPH, vol-
ume 24, pages 405–413.
Tamura, N., Tsumura, N., Nakaguchi, T., and Miyak, Y.
(2005). Spring-bead animation of viscoelastic ma-
terials. In ACM SIGGRAPH Sketches, page Article
No.64.
Tanaka, M. and Masunaga, T. (2010). Stabilization and
smoothing of pressure in mps method by quasi-
compressibility. Journal of Computational Physics,
229(11):4279–4290.
Wojtan, C. and Turk, G. (2008). Fast viscoelastic behavior
with thin features. ACM Transactions on Graphics,
27(3):Article No.47.
SIMULTECH 2021 - 11th International Conference on Simulation and Modeling Methodologies, Technologies and Applications
178